Abstract
An investigation into the thermal performance of waste aggregate concretes was conducted to answer the research question about the thermal behavior of waste aggregate concretes. Typically, the use of waste aggregate concrete has experienced a rise in the construction industry in the recent past. A detailed investigation of the mechanical properties of waste aggregate concrete typically involving the compressive strengths of the aggregate concrete, compression strength were investigated when conducting the research that was based on observing resulting experimental data to inform the research. Thermal design values were investigated, oxygen permeability of the samples was investigated, and the usage of secondary waste materials included the areas of study under examination. An investigation of the environmental and economic impact of the aggregate concrete on the economy was also conducted. Typically, a number of experimental aggregate concrete blocks were used in the study with different measurements subjected to different curing periods. The basis of the study was the setting under the WinTherm32 Version 2.18, with an Instrument Program Version 28, and an Instrument Serial Number, 185 instruments which generated the test data required for establishing performance rationale of investing in waste aggregate concrete blocks in the construction industry. Findings indicated significant satisfaction in the thermal and the mechanical performance of the waste aggregate concrete and rising demand in the use of the concrete blocks under investigation in the construction industry, further reinforcing the rationale of conducting the investigations.
Introduction
The demand for building materials in the construction industry coupled with the recent global recession and the ever-increasing emissions and other environmental effects resulting from the lifecycle of normal concrete presents new challenges in the construction industry, which depends heavily on the use of normal Portland cement and sand to make the concrete. Thus, the importance to investigate the thermal performance of the waste aggregate concrete formed the basis of the current project. Particular interest in the project was to investigate the thermal performance characteristics of the waste aggregate concrete blocks, the mechanical properties of the waste aggregate concrete, the behavior of the concrete underwater, and cost the performance of waste aggregate concrete in the market to justify capital any capital investments in the use of waste product aggregates in making concrete. To face to face the challenges due to cost and the impact due to environmental issues associated with the use of waste aggregate concrete, the use of waste aggregate concrete has been identified to provide a significant solution to the problems. Economic benefits from the use of waste aggregate concrete include employment creation and reduced landfill problems among others as discussed in the paper.
The Research Question
To thoroughly inform the study into the thermal performance of concrete made from waste materials, the economic benefits of using waste materials in the waste concrete, the advantages of the concrete blocks made from the use of waste materials, and the economic benefits accruing from the use of waste material concretes, a research design, incorporating the use of experimental data was conducted. The research problem to be answered was:
What are the mechanical and chemical properties of aggregate waste products and the resulting economic effect of using aggregate wastes in making concrete for the construction industry?
To answer, the above question, research aims and objectives were formulated to guide the literature review and the research as outlined elsewhere in the paper.
Research Aims
- The study aims to make a concrete block that is heat resistant which uses different waste materials such as glass with cement instead of sand.
- To compare the heat resistance, durability, and strength of the new concrete block.
- To preserve the environment by the use of waste materials which have the potential to damage the environment.
- To construct concrete with good thermal insulation for making buildings with minimal consumption of energy and this means lower emissions of carbon dioxide, which has substantial damage to the environment.
- Calculate the cost of production and compare the cost of normal concrete or a little more so that the consumer knows that this reinforced concrete is expensive now, but after a period when costs less because they will be energy efficient.
Research Objectives
- To investigate the design value of the thermal behavior of clay and Portland cement bricks.
- To investigate the usage of secondary materials in concrete and properties of concrete after usage of secondary materials.
- The price of the concrete block made from replaced secondary materials.
- To conduct an environment impact assessment and the importance of using waste secondary materials in making conrete and its effects. The rate of CO2 emissions.
- To investigate the advantages of the concrete block.
- To investigate the effects of the resulting concrete on the economy.
Literature Review
To investigate the usage of secondary materials in concrete
A theoretical framework of the research into the study of the thermal performance of cement incorporating waste materials was conducted by examining available literature and observations and data yielded in the laboratory. The studies were conducted to examine the thermal properties, mechanical properties, the economic rationale, and environmental issues associated with waste aggregate concrete and the projected benefits to be optimized from incorporating waste materials for the purpose of preparing concrete which is used in the construction industry. Typically, the current areas of application include the construction of walls, the construction of bridges, among other applications. Oti, Kinuthia and Bai (2009) report of theoretical and practical scientific experiments conducted in the laboratory to determine the thermal conductivity of concrete incorporating waste materials. In the experiment, Portland cement (PC), quick lime, and clay were used in the set up. The engineering characteristics of the materials used in the investigation are detailed below.
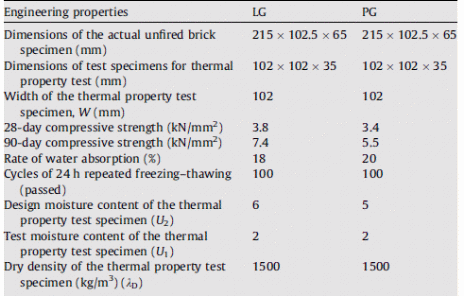
Investigating Thermal Design Thermal Values
In the investigation to determine the properties of unfired bricks, different dimensions specific to the brick were used. For the above unfired brick under investigation, the sizes of the LC and PC bricks measured 215×102×65 and 215×102.5×65 mm respectively. In the set up, the fresh materials were projected to produce approximately 450 bricks (Oti, Kinuthia & Bai, 2009). The materials were then loaded into separate tanks consisting of clay and the stabilizing materials respectively. Then, the materials were transferred into a digitalized mixing chamber where the components were mixed under controlled conditions (Shetty, 2007). Typically, the physical properties of the raw materials used in the set up are tabulated below.
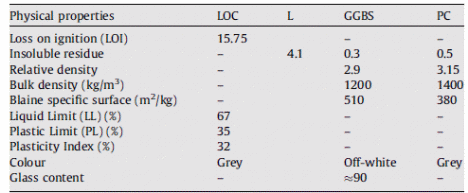
On the other hand, the oxidation properties of the materials including the chemical properties used in the set up were determined before hand as illustrated below.
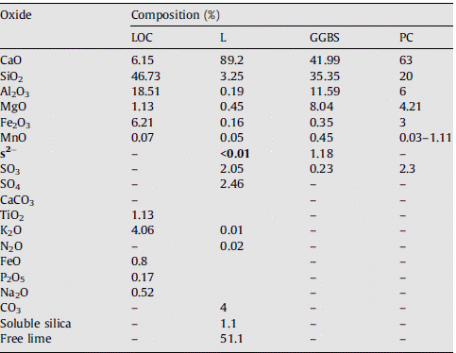
Once the set up was done, compacting of the materials was done using an industrial press that could acquire pressures of up to 120 bars. The resulting bricks from the compacting process were persevered by use of plastic sheathing to prevent the loss of moisture followed by a moisture curing process for the sampled bricks. The curing occurred at a room temperature of approximately 20 ºC with a deviation of 2 ºC on either side of the temperature. The total period of the curing process was 90 days in total (Shetty, 2007).
The resulting bricks were then subjected to compressive strengths tests at the end of the 90 curing day period against British standards of BS EN 772-1. Then, some specimen were identified and selected for further testing in accordance with the DDCEN/TS 772-22 standards which was characterized by 100 freeze/thaw cycles, typical of the British standards. Other test specimens were subjected to constant mass at an ambient temperature specific to the British standards of the BS EN 772-1 (Oti, Kinuthia & Bai, 2009).
It was important to determine the design value of thermal conductivity and resistance to heat, test specimens were hewn from the resulting clay bricks in compliance with the specifications outlined in the BS EN 772-1 standards. To ensure the test samples measured up to the BS EN 772-1 standards, an electric saw was used in the cut the test sample for accuracy. Typically, during the cutting process, care was taken to ensure an accurate test piece was obtained as the brittleness, strength, and toughness of the cutting material and the cut materials were carefully factored.
The differences between both test pieces were determined and carefully documented. Typical of the differences in the materials used in the investigation included the base materials used to make the specimens, and the mechanical and chemical properties of the materials. Typically, the LC and the PC materials involved the use of a GGBS-LOC system for stabilization mechanisms (Oti, Kinuthia & Bai, 2009).
Before the test samples were subjected to mechanical tests, the samples were subjected to a temperature of 40 ºC and dried with a CO2 carbosorb to remove ant traces of carbonation in the drying compartments of the drier. To catalyze the drying process, a constant supply of silica gel was used and the resulting moisture content and other variables were documented on a daily basis (Oti, Kinuthia & Bai, 2009).
Basically, the test was conducted to determine the design thermal value of the test materials in addition to the determining and identifying the thermal resistance of the test materials. The equipment used complied with the specifications of the British standards (Oti, Kinuthia & Bai, 2009).
In order to set the scene for the test experiment, the test specimens were set to a state of thermal equilibrium. Typically, the test equipment was equipped with electronic devices to collect the resulting test data and perform an analysis of the resulting data (Oti, Kinuthia & Bai, 2009).
Typically, the test process involved placing the samples in the actual test chamber and running the experiment. Typically, the internal test environment was well tested and identified and the temperature of the test equipment was accurately controlled. The temperature could be achieved by the use of clean flowing water into the system (Oti, Kinuthia & Bai, 2009).
The thermal conditions of the heat transfer mechanism were governed by Fourier–Biot law which shows that the heat flow is strongly correlated to the temperature. In the set up, heat transfer is achieved through the heat conduction mechanism.
The test conditions allowed for the condition of thermal equilibrium to be achieved under Fourier’s law.
According to the report by Oti, Kinuthia and Bai (2009), the results of the test experiment were identified and documented. At steady state conditions, the thermal transmittance value acquired a mean value of QLG2 = 0.2585Wm_1 K_1, while the thermal conductivity of the complied with the BS EN 1745 standards.
It was established in the set up that the density of both test bricks showed a string relationship between the thermal conductivity and the density if the bricks (Oti, Kinuthia & Bai, 2009).
Mechanical Properties of GFP Waste Powder Filled Concrete
To investigate the thermal performance of secondary materials involved a literature review of the mechanical properties of different materials including reinforced plastic waste that incorporates concrete and glass fibre. Typically, the report was on the mechanical properties of the concrete typically developed from “glass fibre reinforced plastic (GRP) waste powder filled concrete” (Asokan, Osmani & Price, 2009). On the other hand, the thermal performance of concrete typically characterized by sandstone aggregates were also reportedly investigated and reported by (Kumar, 2006).
A study by Asokan, Osmani and Price (2009) indicates that the corrosion resistance and thermal characteristics of the concrete are susceptible to deterioration due to the salinity of the operating environment to which the reinforcing steel is subjected.
Composite materials have been identified to show superior mechanical properties such as stiffness, high tensile strengths, high corrosion resistance, and high resistance to heat conductivity. In addition to that, the sources of the materials included the aerospace and the automobile industries in the UK.
Glass fibre reinforced plastics (GRP) came in the form of powder for the test experiment. The ground powder consisted of a mixture of” GRP ground powder, long fibre and long polyethylene” (Asokan, Osmani & Price, 2009). To further refine the powdered mixture, a fine holed sieve was used to reduce the powdered particles into 2 mm in thickness. An x-ray spectrograph was used to investigate and identify the chemical composition of the composite material.
Established British standards in the development of test specimens were used in accordance with the BS EN12390-2:2000 standard requirements. Typical of the specimen samples used included “normal fine aggregates (NFA) and normal coarse aggregates (NCA)” (Asokan, Osmani & Price, 2009). Samples for the test experiment were into three categories. Typically, the tests were conducted to on the tensile strength, the compressive strength, and the shrinkage of the specimens used in the construction industry.
To create an environment fit for the test experiment, a number of phases were factored into the design process. The Phases were typical in making the test samples of the concrete used in the construction process. To ensure good workability of the test samples was typical of the process, appropriate cement and water ratio was used in the sample construction. The curing process was also characterized by using water that was kept at 50 ºC and 20 ºC respectively. The aggregate duration for the curing processes was 24 hours. A slump test for the concrete was set in accordance with the British standards following amendment one and two of the standards.
Typically, the test areas included determining the density of the test specimen used in the experiment, testing the comprehensive strength of the specimen within the prevailing experimental conditions, determining the level of water absorption of the specimen used in the study, evaluating the tensile splitting strength of the specimen, and the dry shrinkage and the density of the concerned test specimen. The experimental set up was as tabulated below.
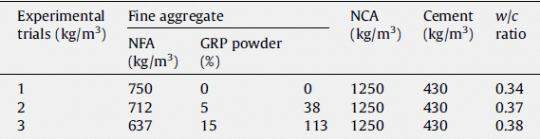
An analysis of the above tabulations indicates different test values for both NFA and GRP powder characterized by different NCA values, cement in kg/m3, and the W/C ratios. After the tests were conducted, a number of results were obtained.
Identifiably, the GRP was an aggregate mix of a polymeric material and glass fibre as raw materials. After an investigation into the physical characteristics of the mixture, the aggregate composition of the GRP substance were identifiably found to contain 95% powder with no more than 5 % fibre. The particle size of the test materials were also examined and identified to fall between 0.02 µm to 600 µm. On the other hand, an examination of the separating distances between the particles of the glass fibre was found to lie between the 0.02 lm to 20 mm range (Felixkala & Partheeban, 2010).
In addition to the findings, the research established that 50% of the GRP was composed of waste materials with a specific surface area equivalent to 0.532 m2/g and 0.961 m2/g.
The Compressive Strength of GRP Concrete
Tests on the compressive strength of the GRP concrete were conducted against the British standards as defined in the BS EN 12390-3:2002 standards. The results from the experiment indicated superior performance characteristics compared with normal concrete. Typically, the structural strength of the material was identified to fall in the range of 45 N/mm2 with an additional 2% superplasticiser (Asokan, Osmani & Price, 2009).
In addition to that above results, it was established that the water cement ratio could be minimized to a 0.38 ratio when the percentage GRP waste of the powder was 15%.
It was established that a significant improvement of the workability of the performance of the concrete was registered. Typically, the mean value of the compressive strength of the GRP concrete was found to lie between 5% and 15%.
According to studies conducted by Asokan, Osmani and Price (2009), the failure pattern typically characteristic of normal concrete were also evidently typical of the superplasticiser concrete. However, when the superplasticiser percentage was varied and reduced to 2%, the failure pattern developed different characteristics to the characteristics of the behavior of normal concrete.
On the other hand, when comparative studies including normal and GRP concrete were conducted, test results indicated that normal concrete materials when subjected to compressive forces showed cracks on their faces. However, results from the use of GRP concrete in the study indicated an overall improvement in the strength of the bonding between the aggregate materials.
A generalized conclusion from the findings indicate that the oven curing provided less superior strength to concrete compared with water cured concrete. In addition to that, an increase in the compressive strength of the concrete was observed when additional materials, particularly, the use of superplasticiser. Typically, the enhanced strength resulting from the use of additional superplasticiser was due to the creation of polymeric bonding between the surface molecules of the surface film of the resulting concrete (Asokan, Osmani &Price, 2009). In addition to that, the use of glass fibre also registered enhances concrete performance where the hydrated concrete performed better than the oven cured cement.
Other additional benefits registered when additional materials were incorporated into the concrete when compared with normal concrete included increased compressive strength. Typically, the irregular formation of the fibre glass and polymeric materials contributed to an increase in the strength of the resulting material (Neville & Aitcin, 1998).
The tensile strength of GRP concrete
To investigate the tensile splitting strength of concrete with GRP waste powder as the main aggregate component in the mixture, different specimens were developed with varying quantities of GRP waste materials incorporated in the concrete (Asokan, Osmani & Price, 2009). Repeated tests were conducted on other specimen samples to validate the resulting data. In comparison to the tensile splitting strength of normal concrete which is 3.9 N/mm2 , the splitting tensile strength of GRP concrete was determined to be within the range of 4.22 +.02 N/mm2. Oven cured and hydrated concrete were observed (Asokan, Osmani & Price, 2009).
An examination of the influencing element in the resulting behavioral characteristics of concrete showed that additional glass fibre was the contributing element. An additional factor was reduced hydration. To further improve the splitting tensile strength of the resulting concrete, the use of the polymeric materials increasing the binder strength and the adhesion strength of the material. In addition to that, the use of superplasticiser showed a strong correlation between the strength of the surface strength. It further showed enhanced bridging of the particles when GRP waste powder was added (Asokan, Osmani & Price, 2009).
In conclusion, the resulting data indicated that a strong bond was developed between the elements that formed the concrete, typically, when superplasticiser was used as the developing material. The resulting concrete showed improved tensile splitting strength when other materials were used in making the concrete mixture. On the other hand, when FRP composite materials were used in the construction of concrete, the resulting tensile strength was further noted to have appreciated significantly when compared with normal concrete (Asokan, Osmani & Price, 2009).
Effect on the Drying Shrinkage of the resulting Concrete
Studies on the effects of GRP on the drying shrinkage registered minor changes in the effect on the tensile strength of the resulting concrete. It was further reveled from the studies that there was no significant change with the use of 5% waste powder incorporate into the concrete. In addition to that, only a 0.008% expansion was registered. On the other hand, when the waste product quantities were added by 15% of the GRP waste powder, a decline to 0.003% was registered. No significant variations were recorded with both the water cured and hydrated concrete (Asokan, Osmani & Price, 2009).
Typically, the results showed little or no drying shrinkage though GRP waste powder had been added into the concrete mixture (Asokan, Osmani & Price, 2009).
Results from the tests indicated that when plastic fibre was introduced into the concrete mixture, the growth rate of plastic shrinkage was confined. The resulting problems included cracking and significant weakening of the resulting concrete matrix. Typically, it was established that the internal structure and surface of the cube was inherently affected by reducing its strength. On the other hand, enhancement of the overall performance of the concrete involved the use of additives such as silica. It is important to note that the percentage by volume of the additives is restricted to 5% only (Asokan, Osmani & Price, 2009).
However, it is important to ensure good curing is done on the concrete to achieve desirable results (Asokan, Osmani & Price, 2009).
Effects on Surface absorption of GRP concrete
Results from the experiment indicated the initial value of the surface absorption of concrete to be 0.04 ml/m2 s when an addition of 5% GRP waste powder was incorporated into the concrete. The value was, however, identified to be half of the value obtained with the control concrete. Thus, there was no significant impact on the addition of GRP waste powder on the surface absorption at the start of the test. However, as additives were incorporate into the concrete, it was observed that the levels of densification of concrete along with the adhesive strength were significantly improved. A summary of the results are tabulated below.
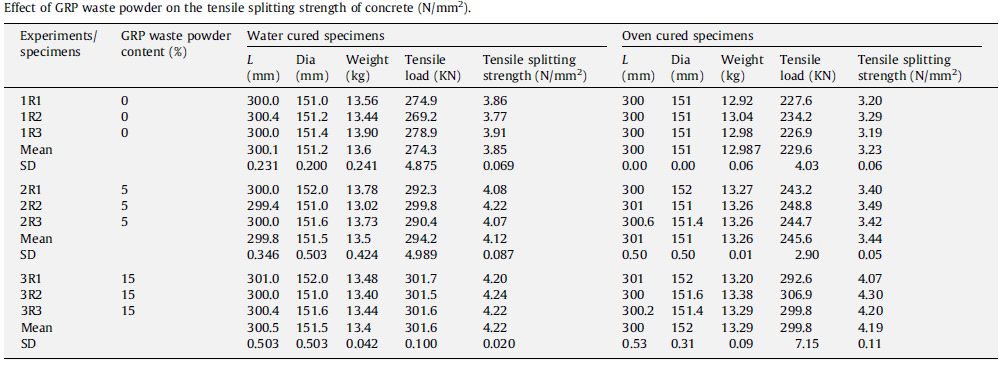
Surface Water Absorption
Typical results on the performance of normal concrete with regard to the surface absorption of water were found to lie between 0.3 % and 0.5 % of the GRP waste powder. The absorption of water was found to be above 6.15% for the controlled concrete. It is important to note that the water absorption behavior of roofing concrete to lie in the lower range of 6%. Further, water cured specimens showed lower water absorption characteristics than concrete treated with 5 % to 15 % waste powder from the GRP product (Asokan, Osmani & Price, 2009).
Density of the GRP concrete
Test data obtained about the density of concrete subjected to water curing registered a value of 2.52 gcm_3 with a 5% and 15% GRP waste powder concentration. The values are tabulated below (Asokan, Osmani & Price, 2009).
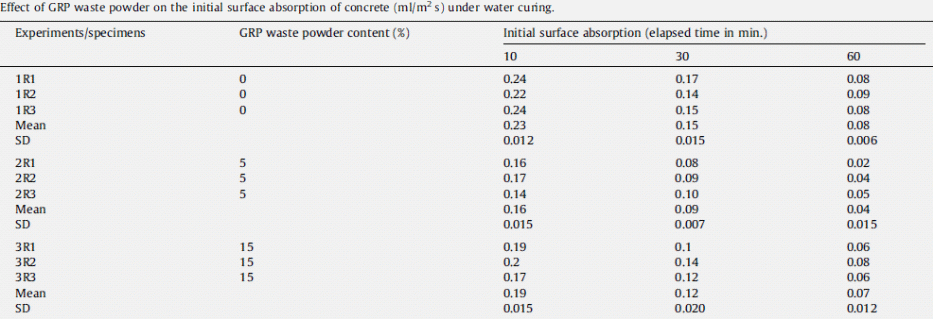
Higher consumptions of concrete and was identified to appreciate due to the use of superplasticiser when GRP waste powder was incorporated into the concrete product. On the other hand, the water cured specimen showed an increase in density. On the other hand, the synthetic effects on the density of cement appreciated further. The results were identifiably constant (Asokan, Osmani & Price, 2009).
Benefits Realized From the Use of GRP Waste In Concrete
A number of economic, technical, and environmental benefits have been evaluated and realized. According to the findings of Asokan, Osmani and Price (2009), the resulting benefits included:
- The use of GRP waste powder appreciated the mean compressive strength of concrete by a margin of 10 % compared with the mean compressive strength with superplasticiser which coild achive a 2 % rise in value compared with normal concrete.
- GRP waste powder concrete registered an enhanced tensile splitting strength compared with normal cement of up to 4.2 N/mm2.
- The use of GRP waste powder as an additive in making concrete showed the resulting concrete to register reduced water absorption capacity of up to 16%.
- An additional use of GRP waste materials appreciated the tensile splitting strength of the concrete, the water absorption capability,
On the other hand, economic benefits identifiably gained from incorporating GRP waste powder and superplasticiser lowers the ultimate cost of concrete. On the other hand, cost savings due to the transportation of waste materials further contributes to the economic viability of the use of waste materials in making concrete for the construction industry (Asokan, Osmani & Price, 2009).
A Study of Lightweight Aggregate Concrete Using Polyurethane Waste
Further studies by Fraj, Kismi & Mounanga (2010) to crystallize the benefits that come with low density concrete in an effort to investigate the usage of secondary materials in concrete and the properties of concrete after usage of secondary materials were conducted with the use of lightweight aggregate materials.
Fraj et al., (2010) reports on the usage of two categories of lightweight aggregate materials in the study. These included “natural aggregates (pumice, diatomite, volcanic cinders, etc.) and artificial aggregates (expanded perlite, shale, clay, slate or glass, hollow microspheres, expanded polystyrene or other polymer materials, plastic granules, etc.)” (Fraj et al., 2010).
Normal Cement
In the study, normal cement with CEM I 52.5 N and sand characterized by a specific gravity of 2580 kg/m3 were used. A low water to cement ratio was used to minimize the amount of water demanded for the preparation.
PUR
Typical characteristics of the light weight cement incorporated into the concrete mix include lightweight coarse particles measuring up to 20 mm in size of the PUR foam material which is also a waste material. When compared with normal cement, PUR is highly compressible after tests were conducted on a 24 hr immersion.
Concrete Mix
According to the following tabulations, four categories of the lightweight concrete incorporating lightweight aggregates were used.

The tests
In conducting the tests, the density of the concrete mixture was determined beforehand and the density of the slump were also determined. The slump was tested to evaluate the workability of the concrete. On the other hand, a calibrated machine was used to identify the drying shrinkage when examined for a period of 28 days.
The mechanical properties of the typical of the compressive strength of the cylindrical specimens were investigated and the modulus of elasticity determined in a 28 day period. In addition to that, the compressive strength of the concrete made from waste foam was examined through an electron microscope.
On the other hand, the permeability of fluid flow based on the following mathematical relation:
Basically, the flow is assumed to be steady and characteristically laminar.
According to the above mathematical relation, L is the thickness of the concrete sample under investigation in (m), the cross sectional area of the sample is represented by A (m2), and the coefficient of viscosity (µ) is 1.78 ×10_5 Pa. The viscous flow is related mathematically as follows:
Results
The tests registered a slump value of 60 and 190 mm when aggregate components of the dry lightweight were used in the process, causing a decline in the slump value. Typically, that is due to the porosity of the lightweight components used in the mixing (Mitchell, Hinczak & Day, 1998).
In addition to that, the workability of the concrete is significantly enhanced. On the other hand, the slump value registers significant decline due to the incorporation of the lightweight aggregates in the concrete product. When LWAC-1 and NWC concretes are compared in terms of the water absorption level tends to reduce the workability of the concrete products. It is important to observe that the behavior of LWAC3-sat concrete and the LWAC-2sat concrete with respect to the incorporation of the PUR foam aggregate compounds. A typical analysis of the above concrete mixtures showed lower slump values while the use of superplasticizer did not show significant improvement in the workability of the resulting concrete. However, the ratio of the mixture showed significant plastic characteristics of the resulting concrete mixture (Mitchell, Hinczak & Day, 1998).
Density
During a 28 day test process, it was demonstrated that the densities of the concretes due to the PUR-foam aggregate concrete registered a significant drop. A further decline in the density of resulting concrete was noted as the ratio of the foam aggregate increased. In addition to that, when lightweight concrete were subjected to pre-wetting, the resulting density registered a marked decline. A further examination of the mechanical properties on a 28 day period of the concrete had to be examined in detail (Mitchell, Hinczak & Day, 1998).
Compressive strength
Observations on the use of lightweight aggregate materials incorporated into the concrete shows a significant decrease in the compressive strength of the concrete on a 28 days test of the resulting strength. Typically, the low mechanical properties and the big extent to which the LWA show sigfnificant levels of porosity, explain the latter characteristics of the concrete. On the other hand, when the LWA concrete was pre-wetted, a further drop in the compressive strength of the concrete was observed.
However, it is worth noting that when superplasticizer was incorporated into the cement, there was a notable rise in the strength of the concrete. Notably, when the superplasticizer was incorporated, a 26% rise in compressive strength was noted.
Modulus of elasticity
The value of the modulus of elasticity was noted to be strongly correlated to the LWA, though LWA caused little impact on the elasticity of the concrete. That implies that the dynamic modulus of elasticity and the density of the concrete were strongly correlated. On the other hand, it was noted that pre-wetting did not show any effect on the modulus of elasticity of the PUR-foam aggregate concrete (Mitchell, Hinczak & Day, 1998).
Gas permeability
Results showed that the gas permeability of LWAC was identified to be higher than that of normal concrete in the range of 1.9 times. On the other hand, an investigation of the LWAC registered a value of 2.7 times that of normal concrete when LWAC had been aggregated with crushed ash clay aggregates (Mitchell, Hinczak & Day, 1998).
Conclusion
From the above study, it was established that making lightweight concrete from LWA materials was a technically and economically feasible undertaking. In addition to that, the technical feasibility was typical of the workability of the concrete particularly with the use of pre-wetted foam.
On the other hand, when the PUR foam was incorporated into the LWA concrete, it registered an enhanced porosity of the resulting concrete and the movement of moisture from and to the environment.
The concrete transfer properties were enhanced by incorporating LWA when making concrete by adding superplasticizer.
On the other hand, when PUR was used in making concrete, a marked decrease in the mechanical properties of the resulting concrete was registered. However, the resulting concrete measured up to the British standards typical of the LWAC standards.
Typically, it could be concluded that the use of lightweight components in making concrete was identified to be an economically and technically feasible undertaking.
When ceramic wastes are re-used in concrete
In reviewing available literature on the use of reusable ceramic waste products, Torgal and Jalali (2009) provides a detailed technical report on observations from experimental data obtained from an experimental work on the use of re-usable ceramics to make concrete. The compressive strength of the resulting concrete, the permeability of the oxygen on the concrete, durability performance, and the results were evaluated in the experimental set up (Mitchell, Hinczak & Day, 1998).
A study of the chemical and physical properties of ceramic materials indicates that the ceramic material falls into two categories. Typically, the first category is from fired factories and the second category is from waste stoneware. In addition to that, the production process of the ceramics is another categorizing factor. Typically, the experimental procedure to determine the mechanical properties of the ceramics produced a number of results as discussed below (Mitchell, Hinczak & Day, 1998).
Compressive strength
The compressive strength of the ceramics was tested against the NP EN 12390-3:2003 benchmark. The test was conducted at a temperature of 18 ºC with a tolerance of 1 ºC. The procedure involved water curing the concrete for a period of equivalent to the testing age (Mitchell, Hinczak & Day, 1998).
Findings
Oxygen permeability
Other tests conducted included the oxygen permeability by use of the permeability cell. Typically, the permeability cell measures 4 cm by 5 cm and has been reliably for some time. The tests were conducted after a curing period of 28 days. Mathematically, the oxygen permeability was determined based on the following mathematical relation:
In the above expression, L is a measure of the thickness of the specimen. On the other hand, R represents the penetrative flow of oxygen through the test concrete test specimen.
Analytical evaluations of the results of the experimental observation are detailed below.
Compressive Strength
When a 20% was incorporated into the concrete, results showed enhanced mechanical performance. In addition to that, when the curing days were longer, the resulting concrete showed improved mechanical performances. On the other hand, the temperature increases improved the pozzolanic activity of the concrete. Thus, an increase in temperature was observed to be important in pre-fabrication and in enhancing the compressive strength of the concrete.
The comprehensive strength of the normal concrete was noted to be higher than the ceramic concrete. However, the compressive strength of the ceramic mixture registered low aging rate than normal concrete.
Durability
The water permeability of different ceramic concrete’s performance was noted to be better than normal concrete. In addition to that, the performance of the specimen concrete registered high resistance to the penetration of chloride chemicals, and indicated lower water permeability.
It was further realized in the tests that the durability of the concrete specimen registered a longer lifespan particularly in moist conditions. That was due to the observations made on the capillarity of water and the ability of the concrete to prevent ingress of water into the specimen. In addition to that, it was observed that the performance from the results on oxygen permeability recorded good performance. Thus a general conclusion drawn from the observations indicated an excellent performance of concrete on all test areas designating the concrete as a good quality concrete.
Wood Shavings and the Thermal conductivity
Bederina, Marmoret, Mezreb, Khenfer, Bali & Que´neudec (2006) made fundamental studies on the thermal performance sand concretes by using wooden shavings in the aggregate mixture. Of typical importance is the reuse of locally available waste materials and the economic importance and environmental value attached to the incorporation of the waste materials.
Incorporated into the study are two types of sands. The dunes sand and river sand were incorporated into the concrete under investigation.
In order to supplement for the particle size distributions of the sand and other fillers, the use of limestone was factored. Bederina, et. al., (2006) conducted the investigative experiment using wooden shavings made from fir trees with particle sizes varying in sizes of 0.1 mm. On the other hand, the chemical analyses of the wooden shavings are tabulated below.
Matlab was used to calculate the thermal conductivity of wood based on the mathematical relation:
The parameters include in the study included D (si) as the Wheatstone bridge readings a constant value, ץ.
Findings
Findings indicate that the porosity of wood affect the thermal conductivity based on the age of the aggregate material, the amount or quantity incorporated into the concrete mixture, and the ratio between the cement and the water used in preparing the sample.
On the other hand, the fine temperature of the sample used in the study
Findings from experimental investigations indicated that the thermal conductivity of wood to be much lower than that of concrete. On the other hand, the hydration of cement was found to be a necessary when examining the effect of water on the weight ratio of the test specimen. In addition to that, observations and tests indicated good wood shavings adherences to concrete constituting cement and wood shavings matrix.
However, observations indicate a retraction of the wooden shavings due to evaporation of water introduced into the concrete by the shavings.
On the other hand, wooden additives to the sand dunes register less dense aggregates specifically due to the size of sand. The other sand registered further lower densities and the difference in density was due the dispersion of the sand particles.
Typically, the thermal conductivity of wooden concrete aggregate against the density is illustrated in the graph below.
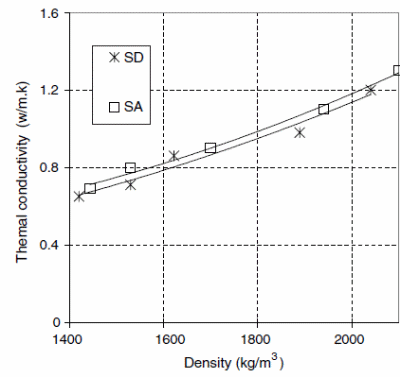
From the above graphical analysis and representation of findings, it is clear that the thermal conductivity of sand is the same and does not vary with the origin or source. That is particularly the case when the density of both sources of sand being the same. However, as the percentage or concentration of sand reduces the thermal conductivity of the aggregate concrete decreases.
Conclusion
The above studies indicate a number of findings. Typically, an assessment of the weight density ratio shows a strong correlation between the concentration of sand and the sample density. As the concentration of sand decreases, the density f the concrete mixture decreases.
The insulating capacity of wooden aggregates concrete increase as the content of wooden shavings increase. On the other hand the aggregate effect is to reduce the thermal conductivity of the concrete.
When wooden shavings are incorporated into different sand prepared concretes, the thermal conductivity of the concretes remains the same.
According to the studies by Bederina, et. al., (2006), appreciating the concentration of wooden shavings reduces the mechanical strength of the resulting concrete. Thus, a concentration typical of the mechanical strengths of the industry has to be prepared.
Concrete from Waste LCD Glass
Wang and Huang (2010) report on the tests conducted to determine the compressive strength of concrete made from waste LCG glass (Wang & Huang, 2010).
In the study, waste glass was reduced to particulate nature and to allow the powder pass through a sieve characterized by fine pores. The chemical composition of the waste LCG glass was also determined (Wang & Huang, 2010). Results showed that the waste glass had a concentration of aluminum oxide as a composite compound, iron oxide, calcium, and potassium oxides respectively (Wang & Huang, 2010).
Results of the tests showed that the toxic levels of the resulting concrete mixture were compliant with the industrial regulations typical of the British Standards.
Findings
From the experimental findings, it was determined that the LCD aggregate waste of the waste glass good flexural strengths which were shown to be strongly correlated to the concentration of the waste glass. On the other hand, a 56 day examination of the concrete established it to register a 20 k µ cm, resistivity.
On the other hand, the experimental data yielded from the study showed that the slump flow consisting of the LCD waste glass appreciated significantly. On the other hand, the compressive strength of the resulting concrete was noted to decrease with increase in the waste LCD glass (Wang & Huang, 2010).
The Price for Concrete from Replaced Secondary Materials
The following discussion will be based on calculations from an project lifespan point of view. To calculate the price of the resulting concrete has been theoretically based on the conceptual framework of the lifecycle analysis of normal and alternative materials used to make different aggregate concrete blocks. In theory and practice, lifecycle factors include project design life where the resulting concrete is to be used and the effective cost. Effective cost is a based on the first costs of the resulting concretes and the maintenance or replacement costs in the entire project lifecycle. Other variables include the inflation rate and the lifespan of the aggregate waste materials used to make the concretes (Design Cycle 25, 2007).
A typical example is where the bid price of the concrete block, P and the effective cost E, are mathematically linked in the following relation: EC = P
On the other hand, if the material used to make concrete has a lifespan less than the actual engineering project life, then the following relation holds: EC = P+ (P x IF x PVF)
In the above mathematical relation, IF and PVF are inflation and present value factors respectively (Design Cycle 25, 2007). IF = (1+I) n
From the relation, the bid price can be used to calculate costs incurred in future replacements using the waste aggregate concretes. On the other hand, the present value of the waste concrete block can be calculated from the following relation (Design Cycle 25, 2007):
In the above equation, i and n represent the inflation life and the projected lifespan of the materials used in making the waste aggregate concrete block (Design Cycle 25, 2007). The effective equation for calculating the price of the resulting concrete is shown below as:
However, if the waste aggregate concrete has been identified to have a longer lifespan than the project life, then the following relation holds:
It is worth noting that m is the total number of replaceable concrete blocks and p represents the projected lifespan of the project under consideration (Design Cycle 25, 2007).
When selecting the factors to inculcate in calculating the price of the waste aggregate concrete block, the following criteria are used in the calculations.
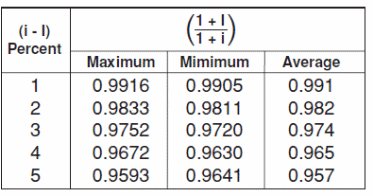
On the other hand, the following table provides aggregate interest and inflation rate calculation strategies (Design Cycle 25, 2007).
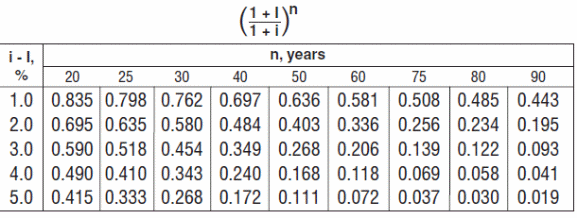
The above tabulations are aggregate interest rates and inflation calculations based on n, the number of years of the project and other variables mentioned above.
The above calculation is based on a 90 year lifespan of the project (Design Cycle 25, 2007).
Other factors to consider include the emission factors typical of the resulting concrete block. The emissions are variables of the transportation and the production of the materials. The emissions result from the energy consumption in the transportation and crushing of various waste materials incorporated in making aggregate waste concrete blocks (Concrete, n.d). The following is a tabulation of the recycling emissions that are factored into calculating the resulting price.

Typically, calculating the cost benefit of using recycled waste materials allows one to calculate the emission factor which involves calculating the cost of virgin products, the costs of the waste aggregate concrete, and finding the difference between the cost of normal and waste aggregate concrete.
In conclusion, therefore, the above strategies of calculating the EC and combining the results from calculations based on the emission factors, and the cost of waste recycling and transportation compounds in obtaining the cost of the resulting concrete block.
Environmental Impact assessment and the rate of CO2 emissions
An analysis of the aggregate effect of the lifecycle of a concrete block on the environment in terms of sourcing for the raw materials used in making concrete, energy consumption and gaseous emissions into the environment, transportation of the materials, maintenance, and up to the end of life of the concrete product is modeled below (Fernandes, Sousa & Dias, 2004).
A study of the environmental impact of waste materials on the environment can be studied based on the model. Typically, the use of secondary materials involves a chain of transportation distances, elaborate manufacturing, and effects of the resulting chemicals on the environment. For example, crushing glass into powder involves affecting the quality of water through contaminations (Fernandes, Sousa & Dias, 2004).
On the other hand, the resulting products due to waste processing in England are illustrated below.
The rate of carbon emissions due to waste aggregate concrete production can be obtained from the above cycle. The cycle involves CO2 emissions due to extraction and recycling of waste materials, emissions die to the transportation of waste materials and related products in making the waste aggregate concrete blocks, emissions due to traffic delays, emissions due to the production of the concrete block, and emissions due to the maintenance of the waste concrete project resulting from the use of waste aggregate concrete blocks. Other variables that influence the carbon dioxide emissions include emissions due to the transportation of necessary equipments to a specified site for making the waste aggregate concrete blocks.
In conclusion, further research needs to be conducted to come up with accurate data on the rate of carbon dioxide emissions due to the waste aggregate concrete entire cycle (Fernandes, Sousa & Dias, 2004).
Source: The need for Indigenous aggregate Production in England.
It is important to consider the estimated amount of carbon dioxide emissions into the atmosphere for the three regions identified in the above table (Fernandes, Sousa & Dias, 2004).
To Investigate the Advantages of The Concrete Block
A judicious use of waste materials in making concrete has been researched and identified to come with positive environmental impact leading to sustainable development. A critical evaluation of the current cement production processes is characteristically unsustainable, as the process is energy intensive of about 100-150 KWT for each ton of cement, and high CO2 emissions and is variably affected by the fuel type in use (Fernandes, Sousa & Dias, 2004).
On the other hand, sustainable incorporation of waste materials in making concrete will reduce by a significantly reduce CO2 emissions into the environment. Studies on the porosity of waste incorporated into concrete, the drying shrinkage, and the chemical penetration of chloride ions indicate enhanced pore structure, mechanical properties such as the comprehensive strengths.
Setting up new cement factory is expensive. Quarrying of raw materials for cement causes environmental problems such as contamination of ground and run-off water systems, and diminishes natural resources (Fernandes, Sousa & Dias, 2004).
Substituting waste materials to make concrete minimizes on the adverse effects on the environment, reduces the amount of CO2 emissions, reduces the damaging effect of quarrying, and allows for a flexible use of secondary materials.
The production techniques and process of the aggregate concrete are further enhanced by use of superplasticizers, improves the microstructure of the concrete, enhances the durability of the resulting concrete, reduces the cost of the overall concrete mixture, and allows for specific concrete to be tailored for specific purposes (Fernandes, Sousa & Dias, 2004).
To Investigate the Effects On The Economy
An investigation into the effects of the aggregate concrete on the economy is studied from various perspectives.
Typically, the profit motive is the main driving force in capital investments in the recycling of waste materials and the resulting profits. On the other hand, the cost of competing materials in place of the waste materials has been identified to be relatively cheaper. On the other hand, the cost of competing materials when the aggregate cost of the competing materials is calculated from the perspective of the environment is high as a factor of production is very high.
Recycling waste materials to be incorporated into the making concrete comes with additional costs and impact on the economy. Typically, employment is created in every step of the process. Employment comes in the form of workers committed in the collection of waste materials, the processing of waste materials, and the capital investment in the processing machinery.
Solid wastes resulting from the processing of waste materials incorporated into concrete can be disposed of as land fill materials, a further economic advantage as the problem of waste disposal is alleviated significantly. Eventually, the aggregate benefits in terms of reduction in the depletion of environmental resources, the direct and indirect costs involved, are offset.
The cost of importing aggregate wastes is tabulated below.
Source: The need for indigenous aggregates production in England
On the other hand, a survey of the current market for recycled aggregate wastes indicates that the 25% of the aggregate wastes incorporated into the production of concrete was majorly sourced from secondary wastes. In addition to that, the survey confirmed a significant rise in recycled aggregates in making concrete. In particular, the recession of 2008 significantly contributed to the rise in the rise and use of aggregate materials in the production of cement.
It is important to note that the strength in demand for concrete relies heavily on how vibrant the economy performs. The aggregate sales from 2005 to 2009 and the share of the market for aggregate waste materials incorporated into making concrete are tabulated below.
Source: Financial Impact Assessment of the Quality Protocol for the Production of Aggregates from Inert Waste.
Methodology
The Research Design
To investigate the thermal performance of various aggregate waste concretes, a machine set up with the following specifications was used. Typically, the machine was a WinTherm32 Version 2.18, with an Instrument Program Version 28, and an Instrument Serial Number: 185. On the other hand, the samples were cured for different periods with different results. Some of the control samples were hewn from resulting waste concrete aggregates to be used in the experimental design.
A summary of the samples with the following detailed specifications were used in the study, with more details available in the attached excel files, and the results were tabulated in the excel sheets in SI units.
A detailed summary of the experimental samples
Further details of the control samples and other samples used in the experimental investigations are in the attached excel files. Typically, the experimental samples used in the study are detailed above. The details include the measurements of the sample studies, compositions by percentage of G powder 1 and G powder 2 Gibsam, sand glass with different measurements, upper and lower temperatures, and curing periods.
Investigating Mechanical Properties
In line with spelt out objectives, the sample design was composed of concrete blocks with the aggregate materials tabulated below. The aggregate materials for each of the tests consisted of sand N.S, sand G.S, Glass powder, waster and cement in different proportions.
Table 1
The block under examination was formulated in the ratio based on the general formula, General formula= 1 (cement): 2.06 (sand): 3.09 (aggregate): 0.5 (water).The percentage compositions of other variables incorporated into the research were obtained using the approach illustrated below.
Typically, the damnations measured 0.05m ×0.2m×0.2m with a Velum content equal to =0.002 m3 after the following relation, 0.05 ×0.2× 0.2. The weight of the cement was made to be 1.54kg and was calculated based on the variables, 0.002m^3*350kg/m^3 ×1.1 ×2. The concrete incorporated the use of sand that measured 3.18 kg and was obtained by finding from the mathematical calculation, 0.002m^3×350×2.06×1.1×2=3.18kg making an aggregate weight of 4.76 kg. The aggregate weight was calculated after the relation,.002*350*3.09*1.1*2. On the other hand, the weight of water used in the examination was 0.77 kg and was calculated using the relation.002*350*0.05*1.1*2. The percentage of the aggregate glass incorporated into the concrete was equivalent to 10% only. The percentage of the glass powder was calculated using the mathematical relation: 0.002*350*0.1*1.1*2.
The next sample to be tested was formulated under the following formula with the following specifications tabulated below.
Table 2
The sample was formulated with the following ratio: General formula= 1 (cement): 2.06 (sand): 3.09 (aggregate): 0.5 (water). Other detailed specifications of the aggregate substances are listed below.
- Velum= 0.05*0.05*0.05=0.000125 m3 with a Cement weight = 0.000125m^3*350kg/m^3*1.1*6=0.288kg
- Sand weight = 0.000125m^3*350*2.06*1.1*6=0.595kg
- Aggregate weight = 0.000125*350*3.09*1.1*6=0.892kg
- Water weight =0.000125*350*0.05*1.1*6=0.144kg
- Glass powder =0.000125*350*0.1*1.1*6=0.0288kg for 10%
The next set up was to test the strength of the sample cube on a seven days curing at a uniform temperature of 20ºC as tabulated below. The applied load was calculated based on the relation, CSA * 0.6 N/mm *60= LOAD
50 *50 *0.6*60=90000 KN/min
Table 3
On the other hand, the following data details the requirements for setting up the investigation the strength of the aggregate concrete cube in a 28 day confusion period.
Table 4
Procedure
The test samples were prepared with varying proportions of water to influence the workability of the resulting concrete.
The material concentrations are tabulated in each of the four tables above. Tests results for the three samples used in the study were tabulated as shown above. The tests were iteratively conducted for different cement ratios. In addition to that, appropriate measurements of the test samples were taken in air and water and respective densities were determined. The applied loads were measured in Mpa N/mm2. Tests were conducted according to British standards.
On the other hand, simulation tests were conducted using the WinTherm32 Version 2.18 machine, incorporating an Instrument Program Version 28 with the Instrument Serial Number: 185.
Investigating Thermal properties
Detailed Descriptions of Test Samples
Test samples to evaluate the thermal properties of aggregate cement are tabulated in the excel files attached in the appendix. Double clicking on each of the files in the appendix provides the actual format and details of the data and the analysis conducted and the results from the test analysis of the test samples. Each of the files provides a detailed sample description, the tests results from the tests for varying curing periods. Detailed descriptions of the results are found in the findings and discussion section and the rationale from investing in aggregate waste concretes are further discussed in the paper.
Disadvantages of resulting concrete
Waste aggregate concrete blocks are significantly more costly compared with normal cement blocks. Typically, the process of preparing aggregate concrete compared with normal concrete is longer and more process intensive. Further studies indicate the concrete to present a typical problem of contaminating environmental resources such as the quality of water (Metha, 2001).
On the other hand, the particle size of the waste powder incorporated into waste aggregate concrete makes it a disadvantage in the stability and durability of the resulting concrete (Metha, 2001).
The physical characteristics due to the particulate nature of the waste powder aggregates make further saps the mechanical characteristics of the resulting concrete, limiting the industrial application of the concrete. In addition to that, the physical characteristics of the waste powder limit the workability of the concrete demanding for the use of additional cement in enhancing the mechanical properties of the resulting concrete (Metha, 2001).
How It Could Help the Economy
A number of economic benefits particularly to the country are bound to be realized from the use of waste materials in making concrete. Typically, the entire chain of recycling waste for the concrete blocks, and making the concrete blocks creates an employment chain. It also saves resources that could be used in disposing of municipal wastes, a positive contribution to the economy (Brown, McEvoy, Mankelow, Ward, Bloomfield, Goussarova, Shah & Souron, 2008).
Another positive contribution to the economy is in the construction of roadway design and construction and other civil engineering project which immensely contributes to the growth of the economy. Typically, the ultimate cost of aggregate waste concrete blocks has significantly reduced giving rise to the usage of the waste concretes. It has been estimated that the ultimate cost savings on the economy has risen by 50% (Brown, McEvoy, Mankelow, Ward, Bloomfield, Goussarova, Shah & Souron, 2008).
On the other hand, the use of waste powder reduces landfill costs, compensation due to environmental pollution, enforces the pursuit of sustainable development, and enables for the achievement of zero emissions (Brown, et, al., 2008).
Findings and Discussion
Findings from the literature reviews and experimental investigations in line with the main objective of the study to investigate the thermal performance of concrete incorporating waste material reinforced the rationale of conducting the study on waste aggregate concretes. Typically, the answer to the inquiry was based on the study about the mechanical and chemical properties of aggregate waste products and the resulting economic effect of using aggregate wastes in making concrete for the construction industry, and the ultimate thermal properties of waste aggregate concretes.
The thermal design thermal values of specific waste concretes made from unfired clay bricks for thermal conductivity was identified to average 0.997. Typically, the thermal design values indicate that the use of unfired bricks minimizes the demand for heating particularly during the cold seasons. One additional characteristic of the thermally unfired bricks are the breath-ability that adds to the thermal resistance of the bricks.
From the economic perspective, the use of thermally unfired bricks reduces the need for providing large amounts of heat, eventually reducing the cost of supplying heat into such walled buildings.
Typically, the thermal conductivity of unfired bricks was strongly correlated to the moisture content, the density of the waste materials, and the dimensional density of the resulting brick. The functionality of the resulting brick due to the above parametric factors makes the brick suitable for low cost masonry units.
On the other hand, an investigation into the use of PUR foam in making lightweight concretes showed high workability, high porosity, good moisture exchange rates with the environment, and the flexibility of manipulating the structural strength of the resulting concretes in compliance with British standards.
An investigation into the use of reusable ceramics in making concrete yielded information about the resulting concrete by indicating the resulting concrete to be possessing lower mechanical strength compared with normal concrete. However, the resulting concrete registered superior durability performance, but registered poor performance under water. The permeability of the resulting concrete was typically low under water.
Results from the study of the thermal performance of concrete incorporating wooden shavings indicated an increase in the porosity of the resulting concrete due to an increase in wooden shavings. On the other hand, defects due to the wooden shavings characterized the concrete brick. In addition to that, the concentration of wooden contents decreased the density of the resulting concrete, reduced the thermal conductivity of the concrete, and reduced the mechanical strength of the resulting concrete.
A study of the durability of the waste concrete resulting from LCD glass and other mechanical and chemical properties provided technical information about the resulting concrete. Typically, the study concentrated on self-consolidating LCD glass concrete.
Findings from the study indicated that the shrinkage of the resulting concrete was strongly influenced by the amount of LCD glass incorporated into the mixture, an increase in the permeability level which seemed to drop with an increase in constituent glass increased. On the other hand, the concrete provided a high resistance to corrosion particularly against the corrosive effects of sulfates, and a high degree of shrinkage with time as compared with normal concrete.
Further investigations into the cost of the resulting concrete and the environmental impact from the concretes incorporating waste products revealed a rising trend in the use of waste materials to make concrete. Analytically, it was typically due to the aggregate cost and effect on both the environment and market driving forces which were identified to be the driving forces behind the rise in demand for waste incorporating concrete in the constructing industry.
It was justifiably noted that the demand from waste incorporating concrete was increasing, after a thorough investigation of the life cycle assessment of preparing waste product cement and the benefits accruing.
Conclusion and Recommendations
An experimental research into the thermal performance of concrete using waste materials was based on an inquiry into the thermal, chemical, and mechanical properties of waste concrete incorporating a variety of waste materials. A number of experimental data from the investigations and market conditions showed a positive trend in the industry. The thermal values for unfired bricks using a variety of clays could be used to project the design values of clay bricks for different environmental conditions. On the other hand, a variety of other materials incorporated into the design in making waste aggregate concretes indicated satisfactory results of the mechanical, thermal, and chemical properties of the resulting concretes by complying with the British Standards. Typically, it was determined from the experimental set ups and tests for a number of days and varying experimentation conditions of the resulting concretes to be fit for industrial consumption. From the environmental perspective, it was revealed that the aggregate waste concrete could contribute to the reduced waste disposal problems by finding a new use for waste materials. In addition to that, the mechanical, chemical, and thermal properties of the waste aggregate concrete was found to be competitively worth when compared with normal concrete giving rise to demand for the aggregate waste concrete in the market. A significant rise in demand has been registered reinforcing the economic rationale for investing in the industry. In conclusion, the thermal performance of the waste aggregate concrete was found to satisfy industry needs under different environmental and mechanical forces to justify its usage in various areas in the construction industry.
However, it is recommended that future research be conducted in the area of the mechanical properties of unfired clay with the use of Portland cement, valorization of locally available materials, the vegetal nature of wooden shavings and the long term effect on the mechanical properties of resulting concrete, and the mechanical properties of wooden shavings concrete with long terms aging.
References
Asokan, P., Osmani, M., Price. A. D. F., 2010. Improvement of the mechanical properties of glass fibrereinforced plastic waste powder filled concrete, Construction and Building Materials, 24(4), pp. 448-60.
Bederina, M., Marmoret, L., Mezreb, K., Khenfer, M.M., Bali, A., & Que´neudec, M. 2006. Effect of the addition of wood shavings on thermal conductivity of sand concretes: Experimental study and modeling.
Brown, T.J., McEvoy, F., Mankelow, J., Ward, J., Bloomfield, S., Goussarova, T., Shah, N., & Souron, L. 2008. British geological Survey. The Need for Indigenousaggegates production in England. Nottingham: Keyworth.
Concrete. n.d. Introduction to Warm and Concrete . Web.
Design Cycle 25. 2007. Lifecycle Costs Analysis. American Concrete Pipe Association. Web.
Felixkala, T, & Partheeban, P. 2010. Granite powder concrete. Indian Journal of Science and Technology. Web.
Fernandes M, Sousa A, Dias A. 2004. Environmental impact and emissions trade. Ceramic industry. A case study. Portuguese Association of Ceramic Industry APICER.
Fraj, Amor, B., Kismi, M., & Mounanga, P., 2010. Construction and Building Materials. Valorization of coarse rigid polyurethane foam waste in lightweight aggregate concrete. Construction and Building Materials 24 (2010) 1069–1077.
Metha, P. K. 2001. Reducing the environment impact of concrete. Concrete can be durable and environmentally friendly.
Mitchell, D. R. G., Hinczak, I., & Day, R. A., 1998. Interaction of silica fume with calcium hydroxide solutions and hydrated cement pastes. Cement Concrete Res.pp- 1571-84.
Neville, A., & Aitcin., P-C., 1998. High performance concrete– an overview. Materials Structures. pp. 111 –17.
Oti, J. E., Kinuthia, J.M., & Bai, J. 2009. Design thermal values for unfired clay Bricks, Materials and Design. Pontypridd: University of Glamorgan: Bhopal. Materials and Design 31, pp.104–112.
Shetty, M. S., 2007. Concrete technology-theory and practice. S. Chand and Company Ltd, New Delhi: Prentice Hall.
Torgal, F. P., & Jalali, S., 2009. Construction and Building Materials. Reusing ceramic wastes in concrete. Construction and Building Materials 24, pp. 832–38.
Wang, H., & Huang, W., 2010. Construction and Building Materials. Durability of self-consolidating concrete using waste LCD glass. Construction and Building Materials, 24, 100813. National Kaohsiung University of Applied Sciences: Kaohsiung 807.