Introduction
Millions of tones of concrete are used annually worldwide. This industry then is very critical and plays a vital role in attaining sustainable development. The changes taking place in the political and social climate and the environment, in general, are making society cease to consider the environment to be a free resource.
Over the years, studies have been done to identify the effects of construction materials on the environment, (National Research Council of Canada, 2000). This paper has discussed the problems and benefits of using concrete as a building material. It has also analyzed at large, the sustainability of concrete as well as compared its sustainability with that of other materials in the construction industry like wood and steel.
As a result of its excellent durability properties, concrete is the most popular construction material on earth. It is the second most-consumed matter after water on Earth, (Pavlenko, S. 1998). Approximately twelve billion tonnes of concrete are processed globally each year.
Environmental benefits
Concrete over the years has successfully been the most commonly used material for construction. The chief reason behind its use is that concrete is the most effective material thus most beneficial to mankind compared to the other materials used for construction. These benefits include;
Low consumption of energy
The materials used in the preparation of both concrete and cement are normally distributed evenly worldwide and consequently, the issue of transporting concrete over long distances does not raise any significant consideration, (Uchikawa, Hiroshi, 2000). The technology that is employed in processing this product is a slight modification of that used in the mining sector.
If this was to be compared with the complex and specialized facilities needed in the plastics, glass, steel, and aluminum plants, far much less energy is used in a concrete facility. The kiln or facility for cement is energy efficient making concrete very popular, especially with the increasing cost of energy over the years.
Provision of the sink for hazardous combustible liquid waste
In the recent past, this form of waste was not being disposed of safely. This waste includes used oil, sewage sludge, solvents, and any other sludge or liquid that is combustible has some fuel value and can be pumped as well, (Mortished C., 2000). Such liquid waste is used as fuel in the cement kilns. The only waste that is contaminated with radioactive, asbestos, or pesticide is not used for fueling these kilns.
It has desirable properties for engineering
Concrete is fairly impermeable and most importantly, it can take up the outline of the containment vessel. Concrete hence becomes very effective for use in the supply of domestic water as well as in disposing of liquid domestic waste. This incidentally was the initial use of concrete thousands of years back by Romans.
Some of these facilities are surprisingly in use today. It is this property of concrete that enables it to efficiently contain hazardous wastes. Alternatively; the concrete mixture is used to immobilize objectionable matter into a concrete mass.
In comparison to clay and wood, concrete is advantageous because it can be monolithically cast into visually attractive forms. Concrete can also be reinforced effectively with steel and this just makes concrete the most suitable material for use by many designers.
Concrete is ideal for making all kinds of highways and streets. This is especially because concrete surfaces improve driving in the night, reflect light, and is not known to rot, washboard, or even pothole, (Miller, 1999).
Low maintenance cost
Properly made concrete is known of having a low maintenance cost. For example, some early concrete prepared in the year 1847 with concrete from Joseph Aspdin was found to be in good condition years on in 1983. This concrete had been prepared with a low content of water to the cement ratio and in addition, it had been well compacted. This implies that it is, by all means, possible for concrete to last hundreds of years. Concrete is resistant to thawing and freezing as a result of an additional agent in the concrete mixture that is air-entraining.
To add to the durability quality of concrete, tests have been developed which can detect and reject any aggregates that are unsuitable as well as minimize the content of alkali in cement to manageable levels.
Provision of the sink for rich industrial silica wastes
Solid waste and the slag from the blast furnace from the industries that refine metals can be dumped off and used as aggregate for concrete. The slag from the burning furnace is palletized into an aggregate with low density or even ground to powder form after which it is utilized like slag cement in place of part of or the entire Portland cement.
Concrete’s thermal mass has saving on the cost of heating and cooling
The transmission of heat through a low down thermal diffusivity material for example concrete is not fast while the proportion of heat that is stored is quite high. As a result, the material does not respond fast to the outside changes in temperature. Generally, in the majority of the places, there is the thermal fluctuation of air. Concrete buildings can even out the resulting low and high temperatures occurring at approximately six am and two pm respectively.
Disposed automobiles can be used as steel in reinforced concrete
Instead of leaving dilapidated automobiles to be a blight on the surrounding environment, they can be assembled, stripped of their copper wiring, and processed in an electric furnace. The resulting steel can then be rolled to produce steel for reinforcing concrete. In this way, there is less pollution compared to the use of fresh steel from the open hearth and blast furnace.
Green aggregates
With the effective use of aggregates that have low density like clay, shale, blast furnace slag, or slate, concrete that is environmentally friendly and light weight can be prepared. The resulting concrete is almost 28% lighter compared to ordinary concrete. This form of concrete has the advantage of being energy saving due to its added thermal resistance capacity which is normally about six times much more than the resistance of the normal concrete, (Klein, Manfred, 1998).
The aggregate with low density has stiffness similar to that of a cement paste template and as a result, there is a reduced concentration of stress in the resulting concrete therefore lesser micro-cracks in comparison to the aggregates with the normal density. The lightweight cement is as a result more durable in very severe and harsh environments and also has higher impermeability ability than the concrete of normal weight.
Environmental problems
Various environmental problems have been attributed to concrete. These among others include;
Carbon dioxide emissions
This is a serious issue due to its contribution to global warming. The concrete industry is rated high in the emission of Carbon dioxide. Concrete is produced from limestone decomposition. The cement plant has to supply electricity that turns the ball mills and the kiln that in turn grind the resulting cement.
It is approximated that for every cubic meter of this product, about four hundred and eighty Kilograms of Carbon dioxide is emitted into the environment. This totals to 7% of the Carbon dioxide that is generated in the whole world. It is not possible to minimize carbon emissions by enhancing efficiency in cement production but rather by supplementing cement with materials that do not emit carbon dioxide.
Particulate air emissions
In addition to the other emissions, the exhaust gas contains particulate emissions that are in the form of dust. If this dust is not collected, the potassium and sodium plume generated by the cement plants settles over the environment and results in acid rain. On the other hand, if the dust is collected it causes problems of alkali reaction.
Emissions of Nitrous Oxide
These emissions are generated by the combustion of coal, gasoline among other types of fossil fuels. When unstable organic compounds and the oxides of nitrogen mix in the presence of sunlight, the ozone layer is formed, (UNEP, 1997). This layer if close to the ground can result in health problems like asthma, coughing, sore throat among other health risks.
The reduction in the emission of this gas can only be attained by minimizing the high temperatures used in burning or by introducing compounds of ammonia into the exhaust stream bearing the high temperatures. This however is not practical as it interferes with the high quality of the resulting ash. This ash as a result requires further treatment to eliminate the ammonia gas and coal that remains unborn before using the ash in the concrete mixtures, (Idorn, G.M., Thaulow.N. 1993).
Visual pollution
This form of pollution comes from the quarries where the raw materials like gravel and sand for processing cement are produced, (Ruhlin, Douglas, 2000). When these materials are grained, the topography is destroyed and sometimes open pits are left glaring behind. Most of these quarries have a long lifespan making it impossible to sculpture them in an attempt to create a nonoffensive visual effect.
Noise pollution
There is a public concern about the amount of noise pollution that results from the concrete plants. It’s for this reason that the plants are located away from habited areas. Where it’s necessary to locate the plants for ready mix close to the site of use, the extent of noise pollution must be reduced to minimum. This is effectively done by the utilization of super plasticizers that involves less vibration.
Water pollution
A lot of water is used in the preparation of the ready mix concrete. In addition, solids like stone, sand and cement are washed out with an approximated 1000L of water. If this is not recycled, it is deserted in a pit either at the plant or job site.
This water that is used for wash out and for cleaning concrete trucks is usually directed or deserted in unsuitable basins where it then drains in to the natural water bodies like rivers and lakes. The polluted water is a health hazard if consumed and it’s also unsafe to aquatic life, (Howell, David, 2000).
As part of the solution to such a serious health hazard, the concrete that remains in the water should be stabilized over a weekend or even overnight by the introduction of a mixture for hydration stabilization. The resulting mixture is later used for preparing the proportions for the subsequent load. This results to reduce or essentially no water pollution.
Health effects
The processing plants negatively affect the health of its employees and workers. This is especially because of the high content of chromium in cement. The chromium mostly originates from the combustion of waste products. It is highly advised that workers in these plants avoid and at all cost prevent the direct contact of concrete with the body. This is clearly indicated in the cement containers.
Traffic congestion
When the tones of ready concrete and cement are being transported congestion of traffic commonly occurs. In some instances however, in an attempt to reduce noise pollution and in controlling the amount of dust released to the environment, the plants for ready mix concrete are located close to the place of use, (Harrison, Neil E., 2000). This as well eases the congestion of traffic.
Environmental cost of excavating materials
The materials used in preparing concrete are water, fine and coarse aggregate, sand and energy. Steel is used in reinforcing concrete during construction and wood is used for making the framework that supports concrete. The environmental cost of extracting the three key components of concrete are discussed here below.
Aggregate
This is mined from underground just like other minerals. Aggregate is generally found in almost all locations around the world and hence it is dug out in the location where concrete is required. This reduces on transport consequently easing traffic congestion on the roads.
Dust is the major waste product of aggregate and if not well disposed can contribute to visual pollution. However, the dust is used as a landfill in the ground where aggregate is mined instead of leaving behind open pits.
Sand
Sand is normally collected from river beds and this has no effect on the environment.
Water
The water used in concrete is the ordinary tap water. This does not affect the environment in any way unless the concrete plant is located in an area where water is a rare commodity. The wash water as well as the water used for cleaning after a days work normally has residual concrete and this is never wasted. Rather, it is left overnight and is used in the preparation of the first batch of concrete the following day. This then reduces on wastage of water.
Sustainability of concrete
The aspect of whether concrete is sustainable is based on three components namely economy, environment and society. For concrete to be sustainable its extraction, processing and use must maintain a healthy status of the three elements named above simultaneously, (Frost A. 2008). The points discussed here below show the sustainability of concrete as a building material.
Concrete is processed from a sand, rock, water and haudralic cement. In addition it contains some proportion of chemical admixture and at times additional mineral to supplement a portion of cement. A normal concrete formula is composed of a large proportion of fine and coarse aggregate, a fair amount of water and cement as well as a small quantity of admixture. Majority of these components of concrete are by products, manufactured products or extracted through mining.
Both the fine and coarse aggregates are mined or attained as a by product of other manufacturing processes. Quite an amount of heat is used in processing and preparing aggregate. The chief waste is water and dust of which has no considerable effect on the environment, (Buckley C, 2001). The resulting dust can be recycled or even disposed as a landfill.
The cement for processing concrete can either be Portland cement or a combination of this cement with supplementary materials like slag or fly ash. Manufacture here involves subjecting the mixture to extremely high temperatures which results in the release of ozone gases like Carbon dioxide and carbon monoxide, (Ruhlin, Douglas, 1995). Though not toxic, the gases cause to global warming on their release to the environment.
The water used in manufacturing concrete is the common tap water and requires no processing. There is no energy required and the water has no environmental effects unless it’s insufficient in the plants location.
Transportation or moving of the ready concrete from the plant to the site of use in large trucks requires a large amount of energy and the mixture produces some amount of waste. Unused concrete, wash water and dust are the resulting waste some of which can be recycled. In the structural applications of concrete steel is used for reinforcement in some occasions which may be pre-stressed.
At the site of construction, concrete consumes minimal to low amounts of energy and the only waste is the unused concrete, used framework and wash water. The steel framework used during construction can be reused while wooden framework is biodegradable and can be dumped in a landfill.
In its lifetime, a structure made of concrete has relatively poor insulating properties and it’s equally a poor conductor of heat. Concrete in addition has poor porosity compared to wood since it’s not a good insulator, (Brecher, Smith B, 2000). Concrete however, has a relatively larger thermal mass enabling it to accumulate energy and releasing it later on.
When the services of a concrete structure are no longer required, it has to be pulled down and consequently disposed off.
Depending on the nature and size of the building, the process of demolition requires a lot of energy. It may be done using a hammer for a small size or controlled blasting for larger structures. The resulting concrete can be used to provide rock for pavement base or recycled, (Porritt, Jonathon, 2000). The waste resulting from the process which is commonly fragments, dust and powder are land filled.
Comparison of concrete sustainability with other materials
The question of the cost of building materials on the environment is constant on many builders and architects today. This is very appropriate considering that there are alternative building materials like steel. It is complicated to give an explanation on how the sustainability of concrete compares to that of other materials used in building. This is because there is no one building that is fully built of one material.
The main reason for using these materials interchangeably is the effects of the environment on the building materials in the long run. Studies in this area examining critical factors like carbon dioxide and other related emissions, the total energy use as well as the quantities of water used during the construction, mining and manufacturing stages have revealed that steel is a better performer, (Alan, 1982).
The cement processing industries have in the recent past been taking significant steps towards the reduction of the energy levels consumed as well as the carbon dioxide emissions produced by the plants. In addition, the industries are increasingly using non fossil sources of energy like waste solvents, used tyres, sewage pellet, bone and meat meal; refuse derived fuel and un-recyclable plastics and plastics.
The excellent thermal mass of that concrete has makes it possible for concrete to absorb, then store and later release heat which then stabilizes the building’s internal temperatures. During summers when the temperatures are extremely high the heat generated by computers, people, electrical equipments, solar gain and lighting is absorbed by the concrete therefore lowering the temperatures, (Malhotra, V. 1996).
Ventilation used during the night cools the building in readiness for absorbing more the following day. This in most of the cases does away with requirements for air conditioning.
Concrete as well has the ability to provide natural ventilation and good lighting during the day. This is so because the concrete that is exposed reflects light right in to the interior of a building thereby reducing the requirement for secondary lighting. In addition, the concrete buildings have a high flow of air as provided by the natural system of ventilation. This leads to a good environment inside the building and air of good quality.
Compared to wood, concrete is a poor conductor of heat as well as a poor insulator. In addition, concrete has poor porosity in comparison to wood, (Alan, 1982). This makes wood more sustainable in comparison to concrete in terms of the aspects of insulation, porosity and heat conduction. It is however notable that concrete is able to accumulate energy and releasing it later on because it has a relatively larger thermal mass.
The consequences of steel and concrete on the environment can be measured in terms of the generated waste and consumed energy in all the stages of the materials right from manufacture all the way to disposal. The chart here below indicates a breakdown of water and energy required directly or indirectly to produce a single unit of steel and wood as building materials.
From the chart, it is clear that the requirement of energy for steel is higher than that of steel by far, Rose D., (2008). It is also true that the amount of water that is required for steel is higher than that of wood. Since concrete is more sustainable than steel by far, it can be concluded that concrete and wood as building materials are more sustainable than steel.
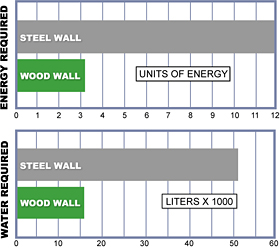
Aggregates that are used in concrete include gravel, sand and crushed rock. The industry has been pursuing a policy that will enable it to be recycling used concrete so that there is a reduced use of natural resources, (Alan, 1982). This is not viable with other construction materials like wood and steel making concrete more sustainable.
The concrete obtained from infrastructure and buildings that have been demolished can be recycled and utilized in putting up new structures. The concrete can also be used as base material in foundations, car parks, runways and roads.
Concrete unlike other materials does not need any extra coverings for fire protection as it is inherently fire resistant and has a long life, (Mortished C., 2000). The fire protection coverings used in other materials like wood may discharge organic compounds that are volatile. The compounds can negatively affect the quality of air in the building.
Concrete has been in use for centuries and dates way back to the roman times. It is used in basically almost all construction projects whether commercial, civil or residential. Concrete is more durable, flexible and sustainable than other construction materials, (Bilodeau, A.1998). These credentials make cement alone the most sustainable building material of choice.
Steel on heating softens at a temperature of 425 degrees centigrade and at around 650 degrees centigrade; steel loses more than half of its strength. Even at a loss of strength of 50%, steel still stands strong and can not collapse at that point, (Malhotra, V. 1996). However, compared to concrete, steel is not a good building material in terms of combustion. Concrete is an inorganic conglomerate is well known to be inert.
Concrete does not melt, burn, drop its strength and neither does it produce molten substance when heat is exerted. This means that incase of industrial fires, concrete is safer than steel as it can withstand any amount of heat of fire.
Estimates show that 85% of the steel used worldwide is recycled. This is a common practice due to the natural magnetism that steel has making sorting easy. Steel is recycled for use in galvanised sheet, rebar or structural steel. Riveting is used in industrial and agricultural building instead of welding or even bolting. This makes steel more sustainable and friendly to the environment.
The amount of energy required in recycling steel is less than that of producing concrete. It is much more energy saving in comparison to concrete. However, it is unfortunate that the demand for steel is high and it exceeds the supply of scrap or demolished steel for recycling, (Malhotra, V. 1996). As a matter of fact, the scrap recovered is is recycled through both secondary and primary routes worldwide. Since scrap is a raw material traded globally, it is impossible to distinguish for every nation, the virgin produced steel and the steel recycled from scrap.
Overall, concrete and steel can best be compared using the Ecopoint rating since there are so many environmental impacts of each material. The Ecopoints of structural steel per tonne is 11(elleven) points. Concrete on the other hand has 12.53 points for each tonne, (Miller, 1999).
If the operational savings of energy were to be overlooked, the use of concrete as a building material seems to have more serious effects on the environment than steel. Steel is however put at a disadvantage due to its high energy requirements during processing and production in comparison to steel.
In the concrete manufacturing industry, the waste aggregates generated can be recycled from the concrete that remains behind after completion of placing. The reclaimed concrete normally in the form of paste can be dehydrated, dried out, crushed after which it can be used as a replacement of the very fine aggregate.
The recycled concrete can be effectively used as a roadbed matter or soil conditioner. In addition, all the water that is used in washing down the concrete drum can be saved overnight in the drum for use in preparation of concrete the following day.
Demolished concrete waste can be recycled rather than be disposed. The waste concrete is crushed and sieved so that the aggregate is recovered. The debris of concrete can alternatively be crushed and used as material for roadbed rather than using more exorbitant procedures for recycling the same, (Malhotra, V. 1996).
On the other hand, It is estimated that, worldwide, more than 75% of steel is recycled at the end of its life. The process is facilitated by steel’s natural magnetism, which makes it easy to sort. In United Kingdom construction, the recycling and re-use rates of various steel products have been estimated at 85% for hot-dip galvanized sheet, 85% for rebar and 99% for structural steel. Some cladding and sections are reused in agricultural and industrial buildings especially, and this is facilitated by the use of bolted sections rather than welding and riveting. By saving on re-melting, re-use is the most environmentally positive approach at the end of a building’s life.
The energy used in producing steel from recycled steel is approximately one-third of that for new steel. Recycling steel saves energy, carbon dioxide and resources by displacing the need to make more steel from unexploited sources. Unfortunately, in the world, the demand for steel outstrips the supply from demolished or scrapped metal. In fact, all recovered scrap is already recycled through primary and secondary steel-making routes in one system. As scrap metal it’s a globally traded raw material, it is impractical to distinguish for each country between primary produced steel and steel produced from scrap.
A global view is instead taken, which avoids the impracticalities of determining the precise origin of steel consumed in the UK. ISO 14041 sets the method by which the embodied energy and product life-cycle environmental impacts should be calculated. In this way, the mix of new and recycled steel and end-of-life recycling are taken into account, taking a “cradle to grave” approach to environmental consideration.
So, using United Kingdom recycled rates, the figures are 13.1 MJ/kg for steel sections and 12.1 MJ/kg for rebar. The corresponding CO2 outputs are 0.76 kg of CO2 per kg of steel and 0.79 kg of CO2 per kg of reinforcement. Not included in these figures is the energy for fabrication, transport from factory to site and on-site construction, although these are relatively minor in comparison.
The argument from the concrete lobby is that although the figures reflect the worldwide situation regarding the proportion of available recycled steel versus steel from virgin resources, it plays down the impact of structural steel in the world, which predominantly uses steel from virgin sources.
However, this new steel will in the main be reused many times, so it could be seen as unfair to account for the initial energy cost against its first life. Most of the world’s iron ore production comes from a handful of large international mining companies and many of these have systems to minimize environmental impact. The steel although a very important component in construction industry is not readily available and environmentally friendly as compared to concrete. The overall energy of producing concrete is about 380 kg of CO2 per m³ concrete in structural components such as floors and columns. It is about 310 kg of CO2 per m³ concrete in pad foundations or the like. Increasingly, though, cement may be partly replaced by alternatives such as pulverized fuel ash (PFA), a by-product of coal-fired power stations, and ground granulated blast furnace slag (GGBS), a by-product of steel production. A substitution of cement with 30% PFA saves about 20% CO2, whereas substitution with 50% GGBS saves about 40% of CO2, but this assumes that CO2 should be entirely accounted for in steel manufacturing figures, rather than the GGBS that flows from it.
All the companies that produce cement have environmental management systems in place and programmes to minimize the environmental impact from mining activities. It is estimated by BRE’s Green Guide that 50% of concrete is crushed and recycled, 40% is down cycled for use such as hardcore in substructure works or road construction and the remaining 10% is waste that goes to landfill. Down-cycling does help to reduce the use of aggregates, but does not help reduce the supply of materials for new concrete.
Environmental summary
If we ignore operational energy savings, the concrete option appears to be about 30% worse but when operational energy is accounted for, this dwarfs the embodied energy and the appraisal is reversed showing a saving of 6% for the concrete option. This comparison has taken two common and recognized solutions but they are dissimilar in that one has a full ceiling while the other uses a predominantly exposed slab. This puts the steel option at a disadvantage energy-wise. In fact, partial or perforated ceilings are available for composite decks, which allow most of the cooling load reductions applied to the concrete building.
Conclusion
Concrete is a very important substance in the construction industry. It has been in existence for many centuries and it is rated the most popular building material. In the processing of concrete other materials like aggregate, water and sand are used to prepare the mixture and this requires an input of energy. Steel is also used sometimes to provide reinforcement while wood is used as a framework. As discussed above, most of these materials are recycled or reused in order to make concrete sustainable. On the other hand, steel is normally recycled in order to make savings on the amount of energy used. However, there is a very high demand of steel in comparison to the supply of scrap steel for recycling. This then makes concrete the most environmentally sustainable construction material.
References
Alan, (1982), Guide to Energy Efficiency in Masonry and Concrete Buildings The Masonry Council of Canada.
Bilodeau, A. (1998), High-Volume Fly Ash System: The Concrete Solution for Sustainable Development, Ottawa.
Brecher, Smith B, (2000), Globalization from Below; South EnoPress, Cambridge, Massachusetts.
Buckley C, (2001), Why Companies Get Steamed Up About the Climate Change Levy; Earthscan Publications Ltd, London, U.K.
Frost A. (2008), Cement and Concrete Sustainability Credentials; Web.
Harrison, Neil E., (2000), Constructing Sustainable Development; State University of New YorkPress, Albany, NY,
Howell, David, (2000), Bottom line of the barrel; Professional Engineering, Vol. 13, No. 23.
Idorn, G.M., Thaulow.N. (1993), Examination of 136 year old cement concrete; Cement and Concrete Research, Vol. 13, No. 5.
Klein, Manfred, (1998), International Symposium on Sustainable Development of the Cement and Concrete Industry, Ottawa.
Malhotra, V. (1996), Performance of Concrete at Treat Island; ACI Special Publications.
Miller, (1999), Environmental Problem Solving – Psychosocial Barriers to Adaptive Change; Springer, NY.
Mortished C., (2000), Carbon Emission Trading System Poised for Launch; Earthscan Publications Ltd, London, U.K.
National Research Council of Canada, (2000), Effect of Pavement Surface Type on Fuel Consumption Phase 2: Seasonal Tests, Technical Report.
Pavlenko, S. (1998), Development and Use of Fine Cement less Concretes Consisting of By-Products as One Of the Ways for Reducing CO2 Emissions; in CANMET/ACI International Symposium on Sustainable Development of the Cement and Concrete Industry, Ottawa.
Porritt, Jonathon. (2000), Playing Safe: Science and the Environment; Thames & Hudson, New York, NY.
Rose D., (2008), Forest Facts: Compare Materials; Web.
Ruhlin, Douglas, (1995), Concrete Reclaimers” A Tool for Environmental Compliance; Concrete Journal.
Ruhlin, Douglas, (2000) Compliance Matters – Storm water Permitting for Concrete Producers; South EnoPress, Cambridge, MassachusettsU.S.A.
Uchikawa, Hiroshi, (2000), Approaches to Ecologically benign System in Cement and Concrete Industry; ASCE Journal of Materials in Civil Engineering, Vol. 12, No. 4.
Schmidt L.(2001), Climate Changes Moving Faster, Scientists Say; Canadian Press, Canada.
UNEP, (1997), Steel Industry and the Environment, Technical and Management Issues; published by the United Nations Environment Program, Technical Report No. 38.