Introduction
Transparent building materials have become popular in contemporary architecture. Glass is a non-crystalline transparent solid material with widespread applications in aesthetics, tableware, windows, and optoelectronics. This material is primarily manufactured from sand which is typically melted down and undergoes a chemical transformation. The architectural glass used in construction is a transparent glazing material (Shioya, & Kikutani, 2015).
While construction materials such as aluminum, stainless steel, and steel have been widely studied, there is limited research on glass material as a construction material. This paper provides a comprehensive analysis of glass as an effective construction material. It gives an overview of its historical applications, its varied forms, its pros and cons, its manufacturing procedure, and its fundamental material properties.
History of Glass
Traditionally, artificial glass was used to make decorations, vessels, and jewelry, while fulgurite (a variation of glass) was used as weapons. Egyptians mainly combined glass fibers with clay to form beautiful vessels. Venetian glassmakers also used glasses to decorate dishes by bundling an opaque white fiber on a transparent vessel. In the sixteenth century, fiberglass was used in the textile industry. For instance, a French physicist, Rene-Antoine, wove the glass fibers to resemble a spider’s web from molten glass (Linganiso & Anandjiwala, 2016). The fabric made from glass was mainly used for exhibitions and expositions.
During the first century, Europeans discovered glass blowing, a technique used to shape and mold glass for artistic and practical uses. Later, Manganese dioxide was introduced into the glassblowing process, leading to the production of the clear glass that is now used in construction. In the eleventh century, glassblowers made sheet glass by molting the glass until it flattened before cutting it into panes. By the nineteenth century, flattened or sheet glasses were used on windows even though they lacked optical distortions. In 1958, float glasses, which are now used in modern windows, were introduced (Zheng, 2013).
The float glasses were very flat with uniform thickness, allowing light into the building, and occupants could look outside through the glasses. Mass production of float glasses started in the twentieth century, leading to their application in “smart cities.” Today, glass is used in architectural designs of domestic homes and is seen as a symbol of affluence and luxury. With innovative technology, the industry has expanded, and large manufacturing plants now mass-produce glass materials.
Types of Glass
There are different glass types, including float glass, tinted glass, toughened glass, shatterproof glass, double glazed glasses, glass blocks, glass wool, and chromatic glass.
Float glass
It is derived from annealing molten glass; it has a rupture property of 5000-6000 psi and weighs between 6-26kg/m2 (Hasanuzzaman et al., 2016). It is commonly used to make glass blocks, shop fronts, railing partitions, etc.
Tinted Glass
These are glasses that have color added to them to improve their aesthetic properties. This color addition does not comprise the glass’s strength. Iron oxide can be added to make the glass green, sulfur makes it yellow, red, or black, and copper sulfate makes it blue (Hasanuzzaman et al., 2016).
Laminated Glass
It is made by combining glass panels without adding a protective layer, making it heavier than standard glasses. It causes optical distortion, protects from 99% of UV radiation, and insulates against sound (Hasanuzzaman et al., 2016). Laminated glass contains at least two or more tempered and annealed glass panes combined with an intermediate plastic layer. Generally, laminated glasses have a thickness of 0.39 m; thus, when the glass panes are destroyed, they can still absorb energy and deflect provided the foil is still intact (Hasanuzzaman et al., 2016). Laminated glass is used primarily to make windscreens, glass beads, glass columns, aquariums, bridges, floor slabs, stairs, and overhead glass.
Shatterproof Glass
It is made by adding polyvinyl butyral to regular glass to prevent sharp edges when the glass breaks. It is used in flooring and windows.
Hydrophilic Glass
Hydrophilic glasses are porous glasses that attract water and spreads it out like a thin film. This way, water cannot leave any marks or spots on the glass. It is also made with nanoparticles to fight dirt, making it easier to wash the window.
Double Glazed Units
Double glazed glasses consist of at least two or more glass panels that enclose the cavity space filled with air or gas. The main benefit of the double-glazed units is that they provide better insulation than a single glazed glass (Hasanuzzaman et al., 2016). Air gaps are added between the two glass panes to reduce heat loss and gain
Chromatic Glasses
Chromatic glasses are designed to control light and transparency from a building. They include photochromatic, thermochromatic, and electro-chromatic glasses that can effectively control light and transparency (Hasanuzzaman et al., 2016). The glasses are mainly used in Intensive Care Units (ICU) and meeting rooms.
Glass Blocks
Glass blocks are made by combining two separate halves of different types of glasses. The two pieces are then pressed together while the glass is still molten and annealed to maintain visual obscuration.
Advantages and Disadvantages of Glass as a Construction Material
Advantages of a Glass as Construction Material
- Glass can absorb, refract, and transmit light without any clouding or weathering.
- Some glasses are created to be weather resistant and can withstand the impact of rain, wind, and sun while still retaining their appearance.
- Unlike most building materials such as construction metals, glass cannot rust or degrade due to chemical or environmental effects.
- It can save energy by efficiently insulating against heat loss and gain.
- The material is available in various colors, making it more aesthetically appealing and giving consumers more choice.
- The material is also recycled and does not degrade during the recycling process; thus, it can be reused multiple times without losing its quality or appearance.
- Some glass materials are resistant to abrasion.
- Glasses save space when used in interior design.
Disadvantages of Glass
- The manufacturing process is very energy inefficient; it requires extremely high temperatures to process the raw material. These processes have negative consequences to the environment and natural resources
- Glasses increase building costs because they are expensive.
- Glass is very brittle and breaks when frequently subjected to stress. The broken glasses pose a significant injury risk to occupants. It is also a safety risk for areas prone to earthquakes.
- The cleaning costs for glasses can be considerably high.
- The ability of the material to withstand sudden load impacts is poor.
- The material is also vulnerable to hydrofluoric acid, which could etch its surface.
- It can cause glare in a façade buildings when there is too much transparency.
- Glass can absorb radiation; therefore, it can act as a greenhouse element. Consequently, it is not suitable for areas characterized by warm/hot climates; it might also increase A/C load and air conditioning costs
Glass Production and Manufacturing
Glass Blowing
Historically, glass was made through the glassblowing technique, which involved blowing air into a molten glass through a blowpipe. The glassblowers would melt sodium carbonate and sand calcium oxide at extremely high temperatures (Shioya & Kikutani, 2015). The glass properties would be improved by adding mixtures of raw materials or coating to meet individual needs. The liquid glass obtained from this process would then be cooled in the desired shape, width, and thickness while it is still molten.
Today, glass is made through the Pilkington process, where raw materials (sodium carbonate, calcium oxide, and clear sand) are introduced into a manufacturing procedure. These materials are typically weighed and mixed as appropriate and specific admixtures are added to the mixture to give the glass desired properties, including color (Shioya & Kikutani, 2015). The mixture is heated to form a homogenous molten glass mixture, and gloated in a tin to shape the glass into the desired thickness. The method through which the glass is left to cool (annelation process) will determine its strength and durability. If the glass is cooled for a relatively short time, it becomes too brittle.
Annealing Process
This process improves the glass’s durability by slowly cooling the glass to release the internal stresses caused during the glass formation. The glass is passed through a lehr, which controls the cooling process to release the stress. The cooling process is slow; it is done by putting the shaped glass on a conveyor belt, which transports the glass to a reheating area before passing in regions with low temperatures (Shioya & Kikutani, 2015). An annealed glass has better resistance than a strengthened glass, although it bursts into small pieces when it breaks.
Tempering Process
The tempering process involves heating an annealed glass to temperatures above 600°C, followed by rapid cooling while using air nozzles to supply the tempering process with air. The material properties of the glass are compressed and held in equilibrium through inner tension. This process helps to strengthen, harden, and make the glass resistant to breakage. Working on a glass after the toughening process will shatter the glass (Shioya & Kikutani, 2015). Therefore, it is imperative for tempered glasses cut, hole drilled, and edge treated before the toughening process.
Material Properties of Glass
- Transparency: Transparent glass allows a building’s occupants to see outside. However, this property can permanently be changed by the electro-chromatic glazing method or add admixtures to the initial batch to make it opaque (Hasanuzzaman et al., 2016).
- U-value: This property measures the insulation property or amount of heat transferred through the window. For example, it measures how much the glass can block heat or cold from entering the building.
- Greenhouse effect: This property refers to the glass’s ability to absorb visible light wavelengths from the sun and infrared radiation. A glass material that traps these radiations will result in high temperatures inside the building (Hasanuzzaman et al., 2016).
- Solar heat gain coefficient: This property refers to the amount of solar radiation that enters the window as a function of heat gain.
- Visible transmittance: It measures the amount of visible light that can pass through the glass.
Mechanical Properties of Glass
Comparison between Glass’s Mechanical Property and Other Construction Materials
Glass has a density of 2.6kg/m3, an average modulus of 70 MPa, and stiffness strength of 26.9. It has the lowest density, modulus, yield, and ultimate tensile strength values than the other common building materials such as steel and aluminum.
Tensile Strength of Glass
Tensile strength refers to the maximum amount of tensile stress or loads that a material can support. Glasses accumulate internal stress during their formation; therefore, they need to be annealed to release the stress. According to Hasanuzzaman et al. (2016), the speed and accuracy of glass marble rebound make glass harder than many steel types. Glass is highly resistant to compressive stress; however, its tensile stress is low. An annealed glass has a tensile strength of 40 MPa (N/mm2), while that of a toughened glass ranges between 120 to 200 MPa (Hasanuzzaman et al., 2016). Theoretically, a toughened glass has a tensile strength of 107 kN/m2, which is higher than the tensile strength of steel. Tempered glasses have high tensile pressure because they undergo a high compression process. Glass fibers, on the other hand, have higher tensile strength than standard glasses due to the flaw reduction processes involved in making the composite materials.
High-strength glasses such as R and S glasses typically have higher SiO2 than other glass fibers. Therefore, they have higher melting temperatures in comparison with E-glasses.
Table 2: This table depicts the mechanical properties of different glass types, including E-glass, ECR, S-2® glass, Advantex® C, and A-glass.
The R and S-2®1glasses have the highest tensile strength, approximately 50% higher than an E-glass. These glasses attain high tensile strength because they are melted at extremely high temperatures in small volumes. Due to their tensile strength, the R and S-2® glasses are only used in specialty applications where thermal durability and strength retention is imperative. For example, they can be used as reinforcement material in wind turbine blades and compressed tanks. In contrast, E glasses are used to make glass bulbs and film resistors.
Glass-reinforced aluminum laminate (GLARE) is widely used in the aeronautical field; the glass is widely used by the BOEING 777. The glass’s application in the aeronautical industry is attributed to its resistance to load compression. Its high tensile strength and compressive strength also give the glass a high strain and residual strength, making it suitable in construction characterized by biaxial stresses.
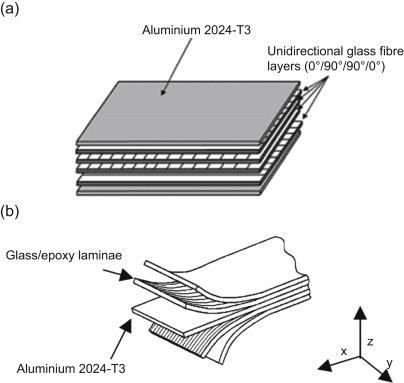
The tensile strength of Glass Fibers
Composites is made of two or more materials bonded and fused together to enhance some of their properties. The young modulus of aluminum and steel is 69 and 180 MPsi, with a maximum tensile strength of 110 MPa and 860 MPa, respectively (Lehman, n.d.). In contrast, the tensile strength of glass is 50 – 90, while that of a glass reinforced with polyester is 17 MPsi. The ultimate tensile strength of compressed glass is 50 MPa (Lehman, n.d.). These statistics show that reinforced glasses have lower tensile strength than normal glasses. This notion is supported by a study conducted by Dong and Davis (2013), which demonstrated that the flexural modulus of a composite material is reduced following the addition of more glass to the material.
Modulus of Elasticity
Tensile modulus or the young modulus refers to the stiffness measure used to compute the elasticity of materials when compressed or stressed. Tensile strength is calculated as the stress ratio per unit area against the strain (the deformation strength) along the axis. According to Hasanuzzaman et al. (2016), strain refers to material deformation due to stress or the change of the materials’ dimension from the original value.
On the other hand, stress is the force exerted on a glass material per unit area. There are three types of stress: shearing stress, compressible stress, and tensile stress (Dong & Davis, 2013). Tensile stress is the stress exerted on a material when it is stretched or lengthened. Compressible stress refers to the stress applied to an object when it is compressed or shortened, while the shearing of the glass material causes shearing stress.
These stresses occur during the lamination processes or when individual materials are fused together to form the composite material. Any defects in the glass or inhomogeneity can reduce the actual fracture strength of the glass. The stressors manifest as cracks, tiny chips, and scratches. Stress can be applied to the glass by a load that exceeds the glass’s theoretical strength, thereby causing fracture or breakage. A glass’s contact with hard objects will cause a flaw on its surface, reducing its tensile strength. Chemical attacks and thermal stress generated during the production process can also cause flaws in the glass surface. The annealing process can also decrease the strength of the glass as it may introduce crystals to the glass’s surface.
Most importantly, a thermal expansion discrepancy between the introduced crystals and the glass matrix will cause flaws in the glass. In summary, glass flaws are typical due to the nature of the production and annealing process. Extensive research has been conducted on the compressive strength of composites (Dong & Davis, 2013). Therefore, certain models were created to determine their strength. For example, Yerramalli and Waas created a model that captures the glass composite’s initial compressive strength before it is affected by shear stress (Dong & Davis, 2013).
The basic assumption underlying the model is that composite failures can occur during the combination process. The typical failure modes during flexural loading include shear failure, tensile failure, and delamination (Dong & Davis, 2013). Delamination occurs when the separation of a laminate layer causes a fracture along the glass fiber’s direction. Tensile failure is rare but happens when two monolithic materials have high tensile properties. Compression failures are the most common types of failure modes in thermal exchange mismatch (Dong & Davis, 2013). Shear stress occurs when a monolithic material is deformed through slippage. These three stressors can result in a bending failure, which measures the flexural strength of a glass composite.
As indicated earlier, the lamination, or a glass combination process, can lead to glass edges that are unevenly resulting in inhomogeneity. Therefore, achieving homogeneity when combining glass materials is not guaranteed. Models such as that created by Yerramalli and Waas are used to determine the residual stress distribution between composite materials and prevent composite failures (Dong & Davis, 2013). These models predict the compressive strength of a lamination process, taking into account the shear and tensile module of each monolithic material.
Another common model is that of Lo-Chim, which forecasts the compressive strength of a unidirectional glass-carbon laminate. The model predicts that the load stress will increase until the compressive stress reaches the compressive strength. Dong and Davis’s (2013) study showed the flexural property of glass and carbon fiber reinforced in an epoxy hybrid composite. The authors combined carbon and three glass fibers to make a hybrid composite specimen. Dong and Davis (2013) also demonstrated that the combination of glass fibers with carbon resulted in the highest flexural strength.
Adding the glass fibers to concrete can also increase the normal aggregate’s elastic modulus. According to Zheng (2013), glass in concrete will reduce the concrete’s strength but increase its elastic modulus. As demonstrated in Fig; 1, adding 20% of glass aggregate to concrete can result in the highest elastic or youth modulus values.
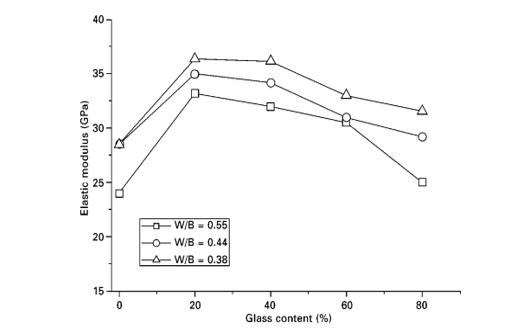
A glass fiber, commonly used as a reinforcement material, is a composite made of a mixture of other glasses. Due to the low tensile strength of monolithic materials, glass fibers are used as a structural material instead. They are commonly used in construction because they are denser than ordinary glasses and have few air and gas pockets.
Glass fibers are also stronger than glass wool; they have relatively low weight, making them attractive options for construction. The glass fibers are extensively used to reinforce polymers because they can combine high strength and low density, and most importantly, at a reasonable cost. They are used as filters and fibrous blankets for insulation (acoustic and thermal) and reinforce polymers in aerospace, sporting, automobile, and construction. Such glasses include A-glass and S-2® Glass, which have a Single fiber tensile modulus of 72.0 GPa and 85.0, respectively (Linganiso & Anandjiwala, 2016). Another typical example of the application of glass fiber in construction is its use as an architectural membrane.
The glass fiber is coated with poly(tetrafluoroethylene) and then used in airport and stadium ceilings. The most commonly used glass fibers are E-glass, corrosion-resistant glasses, and high-strength glass (S-2) fibers (Shioya, & Kikutani, 2015). The S-2 Glass is stronger and stiffer than an E-glass and has better resistance to stress and fatigue. On the other hand, the E-glass fibers have low elastic moduli and are susceptible to stress rupture and stress. The E-glass fiber weaknesses are attributed to the low modulus, which refers to a material’s ability to remain intact when stretched.
Flexural Strength
A hybrid effect refers to the positive or negative deviation of a material from its mechanical properties from the” rule-of-mixture” behavior. Before combining monolithic materials, they have to undergo testing. Glass flexural strength is determined through a three-point bend test, whereby a loading nose is used to deflect a material based on a set span and loading rate until the material fractures. During the trial, the glass material deflects so that its underside will be under tension while the upper side is under compression.
The flexural strength of a strengthened glass can reach up to 106 kN/m2, while that of untreated glass will have a flexural strength of 105 kN/m2. A study conducted by Dong and Davis (2013) indicated that replacing 33% of E glass fiber with S2 glass fibers resulted in a 26% increase in flexural strength. E-glass fiber is built as insulation to electricity, while an S-glass is a high-strength fiber. The key properties of glass fibers include high tensile strength of 1700 N/mm ^2, high modulus, shear strength, water resistance, thermal conductivity, impact resistance, low thermal expansion, less creep with time increase, lightweight and low density, and the resistance to corrosion, fire, and cracks (Dong & Davis, 2013).
Dong and Davis (2013) also revealed that a glass flexural strength and strain and energy storage and strain at maximum stress exhibit a positive hybrid effect when the glass is partially substituted with carbon fibers. C
Compressive Strength of Glass Composite
Because the monolithic materials’ mechanical properties in composite materials are different, the combination will likely result in a coefficient of thermal expansion (CTE). As previously mentioned, thermal expansion differences are process-induced sources of stress in the glass that weakens its tensile strength. According to Dong and Davis (2013), the stress caused to the glass by the thermal expansion mismatch can result in tensile stress of 17MPa and compressive residual stress of 25 MPa. If the tensile stress exceeds the compressive stress, it will cause the glass to shatter.
Compressive Strength
Glass does not have a crystal structure, so slipping cannot occur. Additionally, glasses are characterized by strong atomic bonding, giving them high compressive strength. The molecular structure of glass does not move; thus, the presence of any small crack or impaction will cause stress to localize and surpass bond strength between atoms. For example, a new bulb might not crack on its first fall, but the surface becomes damaged. Any subsequent falls will increase the tension inside the fall, causing it to fall eventually.
The theoretical structural strength of glass can range from one to one hundred GPa, depending on the glass’s composition. The strength of manufactured glass is 70 MPa, while that of regular glass is 17 GPa (Lehman, n.d.). Regular glasses typically have strong Si-O covalent bonds, yielding 435 kJ/mole (Lehman, n.d.). However, this strength cannot be used in practical applications due to various reasons. The practical strength of the material will depend on the total area of surface flaws, scratches, bubbles, and inhomogeneities.
The table above depicts glass strength when it undergoes various processes. A freshly made glass will have a compression strength of 2017-2758 MPa (Lehman, n.d.). Annealed Glass’s compression strength is 69-280 MPa, while that of the glass’s inner surface will be 104-208 (Lehman, n.d.). There are two techniques used to strengthen glass: physical and chemical processes. A glass’s compressive strength can be built through thermal tempering (quench softened glass) and ion exchange. Thermal tempering will create compressive stress on the glass surface while its interior is held together by tension. This way, the glass strength can be increased four to six-fold (Hasanuzzaman et al., 2016). A glass with such strength can be used in automobiles and bus stops. Another advantage of a glass strengthened by this method is that it crumbles when it breaks instead of shattering.
The underlying notion behind these techniques is that imperfection on the glass’s surface will not affect its strength, but it will weaken its tensile strength. This statement explains why the inner surface of the glass, as depicted by the above table, has high compression strength. The strengthening process involves prestressing the glass by inducing compressive pressure on its surface, thereby increasing it to counteract tensile stresses. The physical prestressing involves heating an already-shaped glass to a heating point below its softening point. Its surface is then cooled by blasting air, which contracts the glass immediately.
However, because glass is a poor heat conductor, its interior will not contract, mainly because the exterior will already be set. Any further attempts to contract the interior will only cause the exterior surface to be pulled together. This process leads to the development of built-in compressive stress. Any tensile stress applied to glass will meet these in-built compressive stresses (Hasanuzzaman et al., 2016). Therefore, the glass will not shatter under tensile stress unless the in-built compressive stress is exceeded. The glass will remain solid and shock-resistant provided that the surface remains intact (Hasanuzzaman et al., 2016).
Nevertheless, multiple damages or pressure on the glass surface will cause it to break into thousands of pieces. Typically, glasses are cut into 13 LN-7 sizes and have holes drilled in them to further protect them from the impact of surface stresses before the prestressing process is initiated.
The ion exchange is a chemical process used to strengthen the glass. The shaped glass is placed onto a potassium-ion salt bath, which is 30% larger than sodium ions (Hasanuzzaman et al., 2016). The large potassium ions replace the sodium ions on the glass’s surface, crowding its surface. This crowding induces compressive strain on the glass’s exterior, strengthening the glass. The ion-exchange process involves replacing potassium ions with sodium ions by immersing the glass in a potassium nitrate salt bath.
Conclusion
Glass is one of the most preferred construction materials worldwide. Its compressive strength, tensile strength, and elasticity depend on the glass’s composition. Typically, they have the lowest tensile, yield, and elasticity values than other building materials. The surface defects do not influence the glass’s compressive strength; rather, they weaken its tensile strength. The imperfections on the glass’s surface will not affect its strength, but they will weaken its tensile strength. Glassmakers can prevent flaw formation by coating; it can be strengthened by removing flaws from its surface or preventing cracks from forming. Tensile stress focuses on cracks, while mechanical load focuses on the defects caused by the load impact that exceeds the compressive stress.
References
Dong, C., & Davis, I. J. (2013). Flexural properties of glass and carbon fiber reinforced epoxy hybrid composite. Journal Materials: Design and Applications, 227(4), 308–317. Web.
Hasanuzzaman, M., Rafferty, A., Sajjia, M., & Olabi, A.-G. (2016). Properties of Glass Materials. In Beddows, C. (Ed.), Reference Module in Materials Science and Materials Engineering (pp. 1–12). Elsevier.
Lehman, R. (n.d.). The Mechanical Properties of Glass. Web.
Linganiso, L. Z., & Anandjiwala, R. D. (2016). Fibre-reinforced laminates in aerospace engineering. In Rana, S. & Fangueiro, R. (Eds.), Advanced composite materials for aerospace engineering: Processing, properties, and applications (pp. 101-127). Woodhead Publishing.
Shioya, M., & Kikutani, T. (2015). Synthetic textile fibres: Non-polymer fibres. In Sinclair, R. (Ed.), Textiles and fashion (pp. 139-155). Woodhead Publishing.
Zheng, K. (2013). Recycled glass concrete. In Pacheco-Torgal, F., Jalali, S., Labrincha, J., & John, V. M (Eds.), Eco-efficient concrete (pp. 241-270). Woodhead Publishing.