Introduction
The rapid technological advancement witnessed in the past five decades has facilitated a robust growth in Air transport. The aviation industry is now recognized as the most important transport industry that facilitates fast and efficient movement of people between and within countries. Numerous airline operators manage large numbers commercial aircrafts, facilitating the constant movement of people from one region to another. A typical aircraft is often composed of several different components that work together not only to facilitate fast and efficient transport but also to take into account the environmental and other safety concerns. The outer coat of the airplane protects interior components from corrosion and ad other harmful effects of the environment. Painting has traditionally been used to protect metal surfaces from corrosion, in addition to providing a unique aesthetic detail (Alexander 2005). Most airline companies have developed unique trademarks that are often reflected by the color schemes on the exterior of their aircrafts. The exterior color decoration is part of their marketing strategies and helps them identify with the areas they operate and their customers. Due to adverse weather conditions aircrafts are often repainted regularly to maintain the sheen. Strict guidelines are usually followed when repainting large passenger aircrafts take into account safety and other environmental concerns. The painting should be able to offer protect against corrosion that is facilitated by harsh environmental conditions.
Other methods are being developed to ensure proper protection of airplanes against corrosion. These methods include painting using plasma technology and application of nano structured coatings. This paper reports on the current methods, machinery and tools utilized in the repainting of large commercial aircraft; the research into new painting procedures; the application of nano technology polymers to paint in a bid to reduce drag; and the environmental impacts of repainting procedures and the regulations that guide repainting procedures.
Aims
The aims of this report are:
- To understand the basic procedure of repainting a large commercial aircraft
- To obtain knowledge on the different methods used to respray large commercial aircraft.
- To analyze the magnitude of the issues to be faced by airlines to paint/repaint Aircraft like the A380 and the B787 and other aircraft currently in service.
- Airline operators repainting procedures
- To assess the argument between implication of environmental laws over regulatory authorities such as the FAA versus EPA
- Assess new eco friendly methods of painting commercial aircraft with the use of chromate free paint.
- To research and understand new developments by Boeing and Airbus with regards to eco friendly efficient painting procedures
- To provide a Discussion and conclusion
Objectives of the paper
- To investigate the current and basic procedures performed by operators and maintenance organisations to repaint aircraft.
- Find and extract information on preparations and adjustments conducted on facilities towards repainting new aircraft such as the large A380 and the 787 Dream liner
- Investigate problems faced with chromium paints and environmentally harmful solvents used in paints and strippers.
- To investigate the costs for the operation of a paint hangar.
- Research regulations and requirements to operate the paint hangar.
- To contact relevant authorities to extract and gather information.
- To investigate possible problems that might be initially faced with airline operators when repainting new aircraft
- To understand the advantages using chromate free paint will provide for aviation industry
- To research how waste paint is recycled and solvents are removed for re-use.
- To investigate the regulatory aspects and environmental aspects with regards to the location of a paint hangar in the airport premises.
- To research the necessary tooling and current advanced automated machinery used in paint hangars.
- To investigate safety measures implemented to protect mechanics and engineers from toxic substances during the repainting procedure.
- To research the regulatory requirements needed by authorities for employees to operate in a paint hangar
Current methods and machinery used in repainting of large commercial aircraft
Large commercial aircrafts usually fly through different climatic zones with varying temperatures and humidity levels. These often subject the outer body surfaces to harsh environmental conditions that necessitate regular repainting. Several factors should be taken into account while repainting large commercial aircraft. Different airline companies have adopted individual policies regarding the frequency and the procedures used to repaint their aircraft. Many of them repaint on a four year cycle in preparation for the scheduled C or D check (Global Finishing Solutions 2009). The existing regulations and safety standards stipulate that aircraft should not at any time have more than two layers of paint to maintain operating efficiency. Therefore commercial airline operators usually alternate between complete stripping and scuff sanding the existing layer and applying a new coat (Thelen 2010).
The high levels of safety requirements in the aviation industry have necessitated a strict regulatory framework with regard to the type of paint that should be used and the procedure of application. Additionally, there are strict environmental laws that have to be adhered to while repainting due to the ability of the paint to emit volatile organic compounds (VOC) present in primer and paint itself (Environmental Protection Agency 2008).
It has been generally established that large aircrafts should be repainted in specifically designed hangars that are clean, adequately ventilated, and usually isolated to protect the surrounding area from the chemical fumes that are often released during the procedure. A typical paint facility that can be used to paint a large commercial aircraft is usually equipped with one to two bays. The first bay is used as a preparation bay where the masking, sanding, stripping and detail work are carried out. The second bay is reserved for the painting process where paint is applied to the surface of the aircraft using a spray gun. The stripping and masking can also be carried out in the second bay.
Painting equipment and machinery used for large commercial aircraft
There are various types of machinery and equipment that are used for the repainting of large commercial aircraft. The use of high quality rigs often results into a better quality finish (Thayer 2006). There are two conventional methods that are used in the application of paint include the use of: A conventional pressure fed gun; and the use of high volume low pressure (HVLP) systems (Thelen 2010). The High- volume, low-pressure system represents a newer technology that was developed to tackle the over spraying problem (Hansen 2012). This system makes use of a much lower pressure to propel the paint to the aircraft surface that is being painted. Ideally the pressure builds up in the paint cup forces the paint to move to the nozzle greatly reducing the overspray challenges. The HVLP often achieves this by being machined to a higher degree in comparison to the contemporary spray gun (Alexander 2005). The designing of the HVLP gun allows it to collect the air in inside it and propel it downstream with a minimal pressure drop. This implies that machining must be carried out carefully to lower the turbulence that hampers the flow of air. Two HVLP systems are currently available. The first system utilizes a turbine while the second makes use of the conversion spray gun technique.
In the repainting of large commercial aircraft there are major activities that take place. These activities may include preparation, stripping, masking ad painting. Different repainting procedures are often used by different operators but typically the paint booth has various equipments that are used for various functions. The paint booth operates by circulating a lot of air. Up to 260, 000 cfm of air can be moved during a painting operation for a large commercial aircraft. Air supply is often handled by indirect fire gas heaters that have steam injection grids to perform the introduction of humidity to the air within the booth (Global Finishing Solutions 2009). The filtering of fresh air is conducted at the air replacement unit located at the rooftop, and also at the bottom rolling pneumatically powered filter doors that are located at the front of the paint booth. Air is typically brought into the space between the filter door and the building door that is identified as the sectional overhead door (Global Finishing Solutions 2009). The fans that are used in such a system may be up to 40 HP for each heater and can be rated for up to 6 million BTUs per hour each (Thelen 2010). It is usually necessary to include moisture to maintain the relative humidity within the booth at about 40% RH 21 degrees Celsius. During the paint application mode, it’s often indicated that up to 900 Ib/hour of steam should be generated to satisfy the high demand for humidity. During the curing stage, the temperature can be raised to up to 49C and this may mean that an even higher of steam requirement. Recent systems like the global paint facility have increased efficiency through minimizing the time it takes for the system to move from room temperature to the cure temperature (Thayer 2006). Such systems also provide an eco friendly exhaust system. The eco friendly exhaust systems are installed with granular activated carbon filters that adsorb the VOCs in the exhaust stream.
The typical repainting process
As noted earlier, repainting of a large commercial aircraft should be conducted in a clean setting that is well ventilated. They should generally close off to contain the toxic fumes that will be released from the chemicals used in the repainting process. Large commercial aircrafts are often painted in specially designed hangers such as paint booth inserts, integrated paint booths or paint barns (details will be given later in the report). A typical repainting procedure for an aircraft will go through three major stages, namely stripping, inspection and the application of the new finish (Hansen 2012).
Stripping
Stripping can be described as the total removal of the existing paint down to the metal surface (Airbus S.S.S 2012). Traditionally, chemical strippers have been used to remove the existing paint on large aircraft. However, newer methods such as dry-ice blasting are slowly being adopted to replace the environmentally unfriendly chemical stripping. The personnel are often required to be in a protective gear that includes gloves, safety glasses and a respirator (Thelen 2010). This is required to protect them from the toxic fumes that are released and which have the potential to affect the respiratory system. Often, stripping of a large aircraft uses large quantities of the stripper chemical that needs to be disposed off properly. Rules and regulations on the disposal of the stripper will be outlined later in this report.
Inspection
After removal of the old finish, a thorough inspection of the aircraft is carried out by a qualified and licensed mechanic. During the inspection, any corrosion, loose rivets, cracks and other forms of damage will be detected if they are present. If any of these defects are detected, proper repair work should be performed before the application of the new paint.
Applying the finish
The new paint is typically applied in a two stage process. The primer is usually applied first followed by the application of the topcoat (Alexander 2005). Zinc chromate is the standard primer that is used in aircraft repainting procedures ad is usually applied using a spray gun. An extensive air compression system that will provide air at a required pressure during the repainting process is necessary. Other specific requirements in the repainting process include sufficient lighting that should adequately illuminate the surface of the aircraft and cranes that will facilitate the repainting of far flung areas of the fuselage. In the actual repainting multiple coats are usually applied (Global Finishing Solutions 2009). A second color is only added after the base color has dried up. The finish should be protected using appropriate masking materials. A typical large aircraft is equipped with ports on its skin to facilitate the entrance of air into the system. This additionally provides the ambient air required as the reference air pressure for the instrument (Thayer 2006). During the painting process, a painter should operate with extreme caution so as not to contaminate or cover this vital instrument.
Paint booth insert
Paint booth inserts are large rooms that have been specifically designed with ventilation systems to ensure safety during the painting procedures. The general painting process often puts into consideration the safety, health and quality aspects. These aspects are sufficiently taken care of by utilizing paint booth inserts. Paint booth insert can therefore be described as a self contained area for holding all the operations of the painting process (Airbus S.S.S 2012). Safeguarding the health of personnel from the effects of aerospace coatings is imperative (Environmental Protection Agency 2008). Painters are often required to put on a protective gear that will adequately protect them from the toxic fumes that are emitted from the cocktail of chemicals that are needed to accomplish the painting task. Coatings often contain poisonous metal compounds such as chromates and isocyanates that require absolute care when working with them.
Inserts and paint booths should be able to provide a marked control of the airflow and provide adequate lighting. These facilities provide better ways of energy management because the air flow is lowered to the minimum level that is necessary to satisfy the healthy, safety and quality demands (Luther 2007). High air consumption can result into higher costs, particularly in the in temperate regions where the air required for replacement has to be heated or cooled.
Lighting of a paint booth is a crucial aspect that still poses a considerable challenge, particularly when it comes to large commercial aircrafts. The underside of an airplane contributes exactly one half of the total paintable surface area, and thus provides a critical insert and paint booth design challenge (Thelen 2010). In a typical paint booth insert, the insert has been designed in a way that it allows the lights to get as close as possible to the surface of the plane and therefore ensure that they are properly directed to achieve a full illumination of the aircraft. Most paint booth inserts are entirely stand alone facilities that need very little or no structural from the enveloping facility (Global Finishing Solutions 2009). Thus it’s usually possible to construct a paint booth insert within a vacant hangar facility. Paint booth inserts are very cost effective in the sense that they result into a reduced overall airflow within the paint booth reducing the size of the air moving machinery. This results in the reduction of horsepower, consequentially reducing the cost of electricity. The lights are often positioned within a close range and therefore the total amount of lights required is greatly reduced. The stand alone concept of the booth results in reduced structural requirements and turn reduces the need for steel and the cost.
Paint Barn
A paint barn can be described as a compromise by the designer that is aimed at facilitating the achievement of the main objectives of a paint booth while compromising the finish quality for construction costs. In the development of a paint booth the designer sees the cost of a typical paint booth as being too high. Several factors are often considered for the designer to reach at such a conclusion. One of the factors is the access to the aircraft that is often carried out through the use of the platforms (Thelen 2010). The paint facility might be used for multiple purposes such as aircraft maintenance. In that case there will be a need to use cranes and tele-platforms which are usually hard to include into a paint booth insert. A paint barn possesses flat sports that necessitate protection against fall elaborate access structures. The top beams can accumulate overspray, dust and other airborne particles. If such particles are disturbed in the course of painting they fall onto the surface of the plane resulting into blemishes that compromise the quality of the finished work. The steel beams found in the paint barn can attract birds such as pigeons. Inner walls of the paint barn can be made of a smooth drywall or constructed with sheet metal (Hansen 2012). However, the overhead steel and other hanging items provide a considerable challenge. Lighting has been historically poor in the paint barn design. The painted barn typically utilizes high wattage lamps that hang from the ceiling. It’s difficult to carry out an electrical classification in the paint barn due to the constant presence of volatile vapors.
Large aircraft integrated inserts
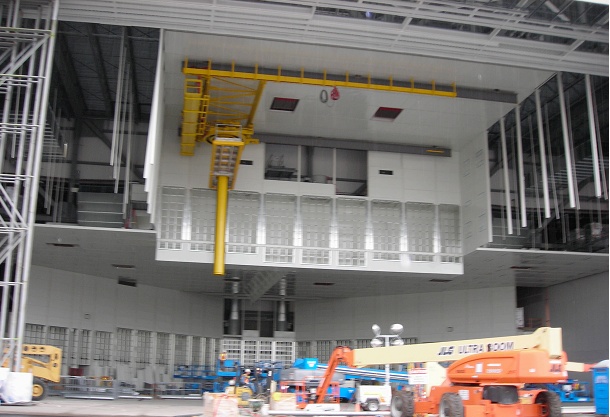
Inserts that are specifically designed for large aircraft may be shaped as the one shown in photo 1. It can be noticed that the filter wall is positioned at the rear side of the booth. The replacement is often introduced into the booth via large doors that are located on the fore side (lower left) of the booth. Large booths of this size are designed to offer airflow that is consistent with possible laminar airflow (Thayer 2006). The tail of the aircraft is often located at the back of the booth. As shown in the photo (photo 1) it is evident that the overall height is considerably different from the overall height. This aspect produces an effect that is often referred to as “conformal shaping”, and whose main objective is to adapt the shape of the booth to that of the aircraft and therefore achieve an overall reduction in the booth and turn achieve reduced energy consumption (Thelen 2010). The paint booth ceiling can be lowered to a level that it’s just above the top of the plane fuselage. The airflow in the booth is optimized for the lower cross-sectional area.
In the integrated system, many of the good features of a booth insert are included into the paint barn model. The booth support is attached to the structural system of the metal construction. The system usually requires the utilization of interior sidewall panels (Global Finishing Solutions 2009).
Mechanical equipment
The design of a paint booth must take into consideration the location of the mechanical equipment that will support the painting process. The lower roof often makes a desirable place where the mechanical equipment can be stored due to the plenty space available.
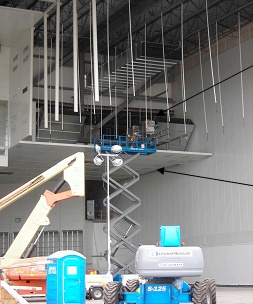
The picture above shows the location of the mechanical equipment and the position of lights in a typical paint booth. In the above photo it can be seen how off-the shelf air make up units can be arranged to provide limited amounts of air flow that is needed in the booth (Thelen 2010). The heavy mechanical equipment is carefully positioned in close proximity to more stable area of the filter chamber. As seen from photo 2, lights are carefully arranged so that they provide maximum illumination to the paintable surface of the plane. These lights are also arranged in a way that they cast light on the flow of the booth so that it’s reflected onto the underside of the fuselage and the wings. This kind of painting facility requires the use floor supported structures or devices to provide adequate access to the aircraft during painting. The structure of the paint booth is optimally designed to accommodate both the overhead and underside devices. Additionally, the structural strength of the paint booth facilitates a more feasible installation of devices that guard against fall. The cables or channels that are utilized in designs that have fall protection can be conveniently attached to the various overhead steel beams that are supporting the roof panel (Alexander 2005). The design aspect of the booth structure is sufficient to facilitate the handling of extreme loads and shapes.
Costing of a paint
A typical paint booth required to conduct repainting of a large commercial aircraft will cost about $ 8 million. The booths dimension will be 265 x 245 x 75, which is sufficient for the length, wingspan and height of a typical large commercial aircraft (C-5, B- 777). The $ 8 million includes the all site work, offices, construction of a water tight envelope and other necessities.
Hazards and environmental impact of painting procedures and EPA regulation
Repainting and other airport operations have the potential to produce several regulated pollutants that may include volatile organic compounds (VOCs), carbon monoxide (CO), and particulate matter (PM) (Luther 2007). Such operations have the potential to produce wide range of hazardous air pollutants (HAPs) (World Bank Group 2007). Clean Air Act (CAA) requires that the environmental protection agency (EPA) to ensure adequate regulation of all emissions that have the potential to pollute the environment. As stipulated by the CAA, the EPA is tasked with the responsibility of establishing the emission standards for various air pollutants based on the potential health risk and effects on the environment. Less noxious emissions have allowable concentrations that are considered safe by the EPA. The EPA has established the National Ambient Air Quality Standards (NAAQS) that determines the respective allowable concentrations of various criteria pollutants (Environmental Protection Agency 2008). In this sense a geographic area that meets a certain standard is considered to be in “attainment” for particular NAAQS (Luther 2007). Information from the Government Accountability Office (GAO) indicates that there is little contribution of pollutants from the aviation industry. Furthermore, the toxic fumes that are produced during repainting procedures are often contained and thus there is no record of their effects on the larger environment. Various agencies and communities are increasing getting concerned with the potential effects of aircraft and other airport related sources of air toxins that are otherwise referred to as hazardous air pollutants (HAPS) (World Bank Group 2007). Unlike the current detailed information on criteria air pollutants, information on emission levels, the transformation and the transport of aircraft and other airport related HAPs and their respective health impacts are currently in the developmental stage (Environmental Protection Agency 2008). As stated earlier, the law expects aircraft painting to be contacted in a contained environment. Repainting of aircraft is regarded as a maintenance practice that should be registered in the log book as directed by Federal Aviation Regulation (FAR) (Environmental Protection Agency 2008). According to this criteria state a local governments may direct the use and disposal of paints, strippers and other chemicals that are used in the repainting process.
The health risks that are associated with fumes emitted during the stripping and repainting process are generally known. The existing guidelines only stipulate how the painter should protect him/herself from contact and inhalation of the chemicals and fumes. Zinc chromate is the primary toxic compound that is utilized in conventional repainting procedures. Zinc chromate has the potential cause a number of health effects that occur shortly after exposure or in the long term (Luther 2007). Immediate effects include irritation of the skin resulting into rashes and ulcers, and the irritation of the eyes, nose and the throat (Thayer 2006). The long term effects that can occur following exposure to zinc chromate include: throat and lung cancer; reproductive hazards; skin allergy and development of sores in the nose (Luther 2007).
Regulatory frameworks stipulate that engineering controls should be used to minimize exposure to zinc chromate. The best practice is to enclose the operations that are conducted using zinc chromate or to provide exhaust ventilation at the site of chemical release (World Bank Group 2007). The personal working with zinc chromate should wear protective equipment that may include respirators, gloves, helmets and overalls (Luther 2007). Most painting facilities make use of all the three strategies to minimize the hazards associated with Zinc chromate.
Research and application of new environmentally friendly aircraft painting techniques
Aircraft painting is one of the key areas that are being addressed in a bid to tackle the environmental effects associated with the aviation industry. Research in aircraft painting has focused on the substitution of poisonous compounds such as chromates and isocyanates.
Use of Non-chromate paints
Boeing and Airbus have been on the forefront in spearheading the adoption of green practices within the airline industry. The first civil airliner to be coated with an environmentally friendly paint was a Boeing 777 that was being delivered to the Dutch operator, KLM in 2009 (Enviro News and Business 2009). The aircraft had been painted with paint that is free from the toxic chromate compounds. The development of the new paint was prompted by a new set of guidelines provided by the Occupational Safety and Health Administration (OSHA) with regard to the handling of chromium (Enviro News and Business 2009). Before then, chromate had been widely used in aircraft paints to protect against corrosion. The compound is however carefully handled due to its ability to damage the respiratory system. The eco friendly painting technique was discovered following collaboration between Boeing and Missouri University of Science and Technology (Enviro News and Business 2009). The new chromate free paint is still able to protect against corrosion.
Application of nano materials in aircraft coatings
In the recent past there has been an increasing trend that seeks to substitute metals with reinforced polymers that can support nanomaterials (Malsch 2007). The research and development of the application of nanomaterials have not however been limited to structural properties of materials, it has been extended to essentially cover other areas such as increasing durability through corrosion prevention. Nanostructured coatings are widely proposed as new tools that will increase the durability of metal surfaces. For instance, nanocoatings will adequately solve the current problems that are associated with the environmentally difficult chrome coatings that are used for the landing gear (Teo 2005). The use of nanocoatings will widen the scope of metals that can be used in the building aircraft components. For instance, magnesium is three times lighter than aluminum and about eight times lighter than steel. The metal has increasingly been used in spite of the fact that magnesium alloys are highly vulnerable to corrosion. The application of anodic or conversion coatings has widely been used to protect against corrosion (Escolano 2009). Anodic coatings that are currently in use are harder, tougher ad possess better wear properties as compared to conversion coatings but they are too costly to be produced on a large scale (Escolano 2009). The chromate based conversion coatings are less expensive but the chromium ingredient makes them carcinogenic and highly hazardous to the surroundings (Malsch 2007). As a result, there is need for the development of a practical substitute. Different programs have been rolled out towards this course. For example, the EU funded the NANOMOG project whose objective was to develop a suitable alternative through the development of clean and environmentally friendly nanocomposite coatings based on silicon oxide thin films (Malsch 2007). The resultant silicon oxide thin films are cheaper and provide better protection against abrasion and corrosion. Other nanomaterials are currently used in the aviation industry. These materials include nanoscale boron oxide and nano crystalline cobalt-phosphorous coatings. Nanocoatings are used to make paints more durable and insulate the aircraft against heat, chemicals and micro-organisms (May 2011).
Various types of nano paint such as nano graphite, nano talc powder and nano Teflon have been recently been utilized in the reduction of friction on aircraft surfaces and thus facilitating the achievement of higher speeds (Malsch 2007). The properties of nano paint to reduce drag levels were successfully tested on commercial aircraft by UK’s easy jet airliner in 2011. The airline utilized a nano polymer that facilitates the cross-linking of a solution to bond with a surface it’s being applied to. The polymer contains hard and durable acrylic elements that form a very smooth finish, filling all the pores on the surface with a special resin. Planes coated with the polymer are smoother and will glide more easily when flying and therefore resulting less fuel consumption. The application of the nano polymer takes place in two stages. During the first stage, the plane is washed using a cationic solution (dicarboxylic acid) that gives it an overall positive charge (Escolano 2009). Then the application of the main polymer coating is done using a negative charge. The two oppositely charged molecules are then pulled together into any pores on the surface of the plane and are magnetically bound there. The coating effectively locks the paint and prevents drifting fading or deprivation of the paint until renewal (Malsch 2007). The polymer has been used by the US military for quite some time but was first adopted for use on commercial planes by easy jet (May 2011).
Application of atmospheric pressure plasma technology in the painting of large aircraft
The plasma technology (Openair) has been spearheaded by plasma treat, a company based in Steinhagen. The plasma technology seeks to play a major role in the effort to reduce the use of toxic solvents and improve the quality of painted surfaces. The atmospheric pressure plasma technology is a stable process that takes place through three principles of action (Buske 2008). It causes the surface to be activated via a selective oxidation process, eliminates static charges and causes a fine cleaning of the surface. Thus it creates optimum conditions that are necessary for increased paint adhesion. The system does not have any restrictions regarding in-line integration and can function with robots. The system facilitates the treatment of both large and small areas of a plane. The system is environmentally friendly since it only needs compressed air and power supply to run and emits no emissions. The system is very efficient in the removal of static electricity and dust present on the surface of the plane and thus facilitates the achievement of a high quality painted surface (Buske 2008). The emergent beam produced from the Openair plasma has a very high intensity that can go as high as 100 m/min. Anticorrosion primers are mostly used in the interior parts of the aircraft fuselage and wing structures that are equipped with reinforcing and fastening devices as well as in the countersunk riveted assembly parts (Buske 2008). Such areas are usually difficult to clean using conventional methods. Normally, the countersunk rivet edges are easily damaged and often form the beginning point for corrosive degradation. The ability of plasma to operate without contact and to reach to these hidden areas facilitates the attainment of reliable adhesion of coatings without causing any damage to these areas that are vulnerable to corrosion (Buske 2008).
Discussion and conclusion
This paper has reported on the on the current methods, machinery and tools utilized in the repainting of large commercial aircraft; the research into new painting procedures; the application of nano technology polymers to paint in a bid to reduce drag; and the health hazards and environmental impacts of repainting procedures and the regulations that guide repainting procedures.
Repainting of larger aircraft is often necessitated by the need to protect the metal surface from corrosion and to maintain the shiny gloss that reflects the image of the operator. Most airlines repaint their aircrafts in a four year cycle in line with scheduled C and D checks. Traditionally, large aircraft are repainted in specially designed hangers that have been equipped to facilitate the achievement of various painting operations (Hansen 2012). The most important aspects of the painter facility include ventilation, lighting and provision of access to the various parts of the fuselage. The conventional repainting procedures that utilize toxic chemicals require adherence to strict containment procedures that account for the major design aspects of a typical painting facility. Painting facilities that are used for the repainting of large commercial aircraft can be classified as booth inserts barns or integrated booths depending on the aspects of the design. Painting of large commercial aircraft makes use of equipments that include mobile cranes to provide access, spray guns, air compressors and proper lighting. The process often involves chemical stripping though ice blasts can be used to strip the paint, followed by an inspection for any defects before the final paint application.
The conventional aircraft repainting procedure has a number of concerns that pertain to the hazardous effects, the durability and quality of the painted surface. As a result, there is an ongoing research into new durable, quality and environmentally friendly methods. The research areas include: the use of non chromate paints that are free from the toxic chromate compounds. Most of this research is still at the experimental stage and so far the various corporations involved in the research have not provided sufficient information regarding the specific details of the new compounds that are to be used instead of chromate. The second priority area is the development of nanocoatings and nano paints for use in aircraft painting procedures. The nano paints result into increased bonding that creates a smoother surface, effectively reducing drag and fuel consumption (Teo 2005). The strong bonds created by the nano paint results into a durable high quality painted surface that can maintain the sheen until the next painting activity. The use of nano paint for commercial aircraft application was pioneered by UK’s easy jet airliner (May 2011). Plasma technology has also been developed to provider a greener option in aircraft repainting procedures by reducing the use of toxic solvents. This system only requires a power supply and compressed air and results into better adhesion by selectively oxidizing the surface.
As research continues into the identification of new environmentally friendly painting procedures, it’s hoped that a permanent solution is established soon to prevent the hazardous effects of current procedures and provide a more lasting solution that can adequately protect aircraft metal surfaces from corrosion.
References
Airbus S.S.S. 2012. Eco-efficiency:”Life cycle” approach. Web.
Alexander, R 2005. PAINTING… Solving the Mystery, Sports Aviation Magazine, New York.
Buske, C 2008. Aircraft painting: Efficient and environmentally friendly pretreatment of fibre-composite materials by means of innovative process technology, Plasmatreat GmbH, Steinhagen.
Enviro News and Business. 2009. Boeing Airliner Wears Environmentally Friendly Paint. Web.
Environmental Protection Agency. 2008. ‘National Emission Standards for Hazadours Air Pollutats: Paint Stripping and Miscellaneous Surface operations at area sources’, Federal Register , No. 6, Vol. 73, pp. 1738-1768.
Escolano, C 2009. Shaping European Nanotechnology: S & T developments in transport, Bax & Willems Consulting Venturing, Barcelona.
Global Finishing Solutions. 2009. Global paint facility, Innotech- Excaire, Montreal.
Hansen, D 2012. Painting versus Polishing of Airplane Exterior Surfaces. Web.
Luther, L 2007. Environmental Impacts of Airport Operations, Maintenance and Expansion, Congressional Research Service, Washingto D.C.
Malsch, I 2007. Ninth Nanoforum Re Nanotechnology in Aerospace, Institute of Nanotechnology, London.
May, K 2011. EasyJet slaps on nano technology paint to make aircraft more efficient. Web.
Teo, K 2005. ‘Microwave Devices: Carbon nanotubes as cold carthode’, Nature , no. 1. pp. 437-968.
Thayer, A 2006. ‘Chance of a Lifetime’, C&EN , No.18, Vol. 84, pp. 10-18.
Thelen, R 2010. Painting large Aircraft: An integrated Approach, Global Finishing solutions, Florida.
World Bank Group. 2007. Enviromental, Health, and Safety Guidelines for Airline, New York.