Mixing
Different additives are combined with elastomers, for example, antioxidants, re-enforcing elements, pigments, processing aids, softeners, and curing agents. Dispersion kneader aids the combination since it mixes all components under high pressure, controlled heat, and stipulated mixing durations (Barbera et al. 710). The mixture generates compound lumps that are obtained from the dispersion kneader. The clumps are allowed to cool then stored for a few days to enhance the quality of the product.
The primary material of rubber compounds or elastomers is unvulcanized rubber, which is produced either as natural rubber on plantations or by the chemical industry. The remainder of the formulation consists of fillers, vulcanizers, accelerators, and antioxidants. They maintain or alter the properties of the raw materials to meet the specific requirements of a particular application. For example, thermoplastic elastomers are a physical mixture of polymers that exhibit both thermoplastic and elastomeric properties. These elastomers cover a special group of polymeric materials that are subject to a high level of elastic deformation without cross-linking (Cho et al. 88). They demonstrate the characteristics of both thermoplastics and thermoset rubbers at the same time. Thermoplastic elastomers are an essential class of materials and can be used in a wide range of industries. In general, they cover many different types of structures of polymeric materials (Cho et al. 87). Then, thermoplastic elastomers are distinguished by the fact that they are soft and flexible, like thermosetting rubber. At the same time, they can be processed both in a melt and like thermoplastics.
Extrusion
During the extrusion stage, the rubber complex sheet is introduced into the extruder, which comprises a revolving screw within a tight-fitting hot cask. The objective of feeding the rubber into the extruder is to pressurize, mix, and soften it since it is continually channeled to a shaping die at the outlet of the extruder (Yu et al. 4). The generated product has a consistent cross-section along the span of the formed items. Characteristic produced rubber items encompass seals and gasket profiles, weather stripping, and tubing.
If the melt viscosity is too high, it is difficult to obtain products by extrusion due to the high resistance to the melt flow and the emergence of an unstable flow regime. It leads to the formation of defects in products. An increase in the processing temperature can result in thermal degradation of the melt (Formula et al. 214). Then, an increase in pressure and drive power at lower temperatures may lead to mechanical degradation. Thus, elastomers with a reasonably narrow viscosity fluctuation range should be used for extrusion. It should be mentioned that the extrudate emerging from the die must be form-stable. The requirements for dimensional stability depend on the following aspects. These are the extent of deformation of the melt in a free state and a calibrating device utilized. Then, the final stability of the shape depends on the temperature and molecular weight of the elastomer.
Calendering
In the calendaring phase, a plastic or rubber product moves across a chain of rollers in an effort of smoothing, flattening, or coalescing two or more elements. Calendered pieces may have numerous layers of polymer and elastomeric compressed together. In line with the intended application and needed appearance or texture, pieces of plastic or rubber may be polished, smoothened, refined, and made to have a raised surface or wavelike pattern (Barbera et al. 712). The final surface features rely on the pressure applied by rollers, the degree of heat, composition, surface plan, and the form of cover on the product that is calendered.
Calendars are very massive due to the considerable effort required to force the plastic mass into a thin gap. They need high temperatures with a low tolerance on the shaft and high pressures. A large floor area is required due to related devices such as mixers and temperature control systems. Therefore, calendaring is a capital-intensive process, and there is a trend to create calendars for large-format products; otherwise, their price is proportionally unprofitable. In the rubber industry, calendaring is used to produce rubber sheets and plates with different thicknesses, plasticizing, heating the rubber compound and lubricating the fabric with the rubber compound.
Compression Molding
Compression molding is a stage where the compound is compressed in a hot mold to assume the shape of its cavity and undergo curing attributable to the high temperature and pressure employed on the material. It is an essential process that generates flat sheets and fabrics with rubber coating (Yu et al. 4). The compound taken into the compression molding process could be in pre-shaped blanks or putty-like substances. The pressure is applied to the compound before it is forced to fill the mold cavity with a heating system that ensures effective curing.
Thus, compression molding is a process consisting of several elements: obtaining the necessary rubber compound and manufacturing the workpiece in the shape of the final product. The workpiece provides an excess of material when the space is full. Compression molding is often chosen for medium-hard products in small-volume production or for the manufacture of, particularly expensive materials. This process results in minimizing the amount of overflow or scrap created during the molding process. When creating complex rubber products obtained by pressing, some mold designs are quite difficult for laying rubber in them (Maghsoudi et al. 619). In addition, the compression molding process of rigid rubber compounds is not well suited to the requirements for material consumption.
Injection Molding
This is the phase where the compound is compressed onto a mold cavity via an opening. Rubber products in strip form are introduced into injection molding machines. The products are then pushed forth by a feeding screw and taken into a split mold, entering its cavity through a runner system. The injection molding machine resembles an extruder with the major difference between them being in the screw action (Yu et al. 4). In the extruder, the screw turns continually to create a continuously long product, for example, a rod or pipe. However, in the injection molding, the screw does not just only keep rotating but also moves back and forth consistent with the progress of the molding cycle.
Injection molding significantly reduces the number of blank preparation operations – there is no need for cutting blanks or manual gluing – and it ensures good filling of the mold. Moreover, it accurately doses the empty according to the volume of the mold slot (Volpe et al. 3). This method is convenient in the manufacture of large-sized products or products of complex shapes. It also successfully replaces knurling or profiling in the production of hollow cylindrical workpieces. Finally, filling the mold with hot rubber reduces the vulcanization time. Thus, injection molding not only reduces the loss of raw materials but also significantly speeds up the production process. In addition, this process can be automated and performed without human intervention. Generally, “molding provides higher quality rubber bands, higher yield, and more flexibility in spring design,” if to compare with laser cutting. (Bergbreiter and Pister 3; Figure 1). At the same time, screw-type injection molding machines that are quite common in rubber manufacturing have a complicated design that limits their application.
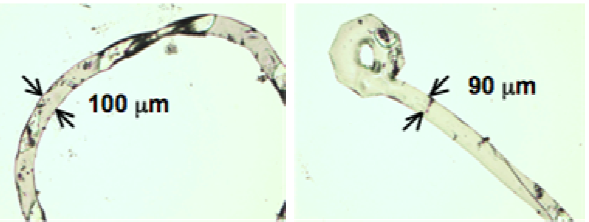
Vulcanization
This process results in valuable rubber products such as mechanical items and tires. Unvulgarized rubber is taken into the vulcanization process to make it less sticky and enable it to retract to its initial shape following deformation. Rubber and sulfur, together with other elements, are heated to over 300 degrees Fahrenheit in a pressurized mold (Barbera et al. 715). Heat and chemicals introduced in the vulcanization process harden the rubber and enable it to retract easily. The described above process is called sulfur vulcanization; sulfur atoms participate in the formation of intermolecular cross-links. When about 5% sulfur is added to the mixture with rubber, a soft vulcanizate is produced, which is used for the manufacture of automobile cameras, tires, rubber tubes, and balls. When more than 30% sulfur is attached, a rather hard and inelastic ebonite is obtained (Hassarutai et al. 1). As accelerators in this process, such as thiuram, are used, the completeness of the action of which is ensured by the addition of activators consisting of metal oxides, usually zinc.
Radiation vulcanization is still possible; it is carried out by means of ionizing radiation, using flows of electrons emitted by radioactive cobalt. Such a process – without the use of sulfur – contributes to the production of elastomers endowed with special resistance to chemical and thermal effects. For the production of particular types of rubbers, organic peroxides, synthetic resins, and other compounds are added at the same process parameters as in the case of sulfur addition.
Curing Machines
In curing machines, rubber extrudate is refined to sustain its shape and obtain essential physical characteristics. This is achieved by a chemical reaction (the joining of molecules) from sulfur curing components (Barbera et al. 713). Curing starts when extrudate temperature is increased by feeding it into media such as microwave or hot air system. The size of the rubber changes slightly in the curing process and this should be considered in the die design.
Due to the fact that rubber is not the best thermal conductor, the processes of curing machines are different because of the temperature variations of the material’s parts. Thus, in order to provide a relatively even degree of vulcanization, thick rubber is commonly vulcanized by the cautious increase of temperature for a long time. It might be assumed the latter statement emphasizes the fact that using curing machines for rubber manufacturing is quite a laborious and challenging process. It requires the highest quality of the tools being used, as well as of employees involved.
Laser Cutting
The laser cutting process is based on the local evaporation of the rubber when it is heated by a laser beam. The ease of propagation of the laser beam allows processing regardless of the spatial location of the treated surface. Laser cutting is widely used in the processes of cutting thin rubber. It provides the opportunity for high-quality, clean, and cut-free cutting. Laser cutting of rubber gives an accurate cut, and due to the fact that there is no direct contact of the cutting tool with the material, the rubber does not deform. It guarantees full compliance with the given contour; the edges at the exit are smooth and uniform.
Laser cutting of rubber also has some limitations; in particular, not all laser machines are capable of cutting the rubber. The second disadvantage is that not all types of rubber are suitable for laser cutting. For example, black butadiene styrene rubber categorically does not fit cutting in this way. In essence, the quality of the cut or engraving will be deficient, and the product will turn out to have various properties. Then, “the cuts provided by the laser result in jagged edges” (Bergbreiter and Pister 3; Figure 2). In addition, when treated with a laser (like with other thermal methods), this rubber gives substantial evaporation of harmful and carcinogenic substances. It should be emphasized that even excellent ventilation cannot wholly eliminate decomposition products.
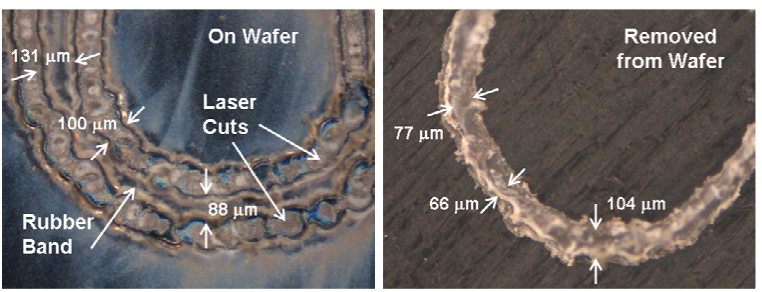
Material Testing
It seems reasonable to state that it is essential to be capable of characterizing the viscoelastic attributes and hysteresis. For gaining advantage from “the curve fitting and remeshing possibilities, it is advisable to choose the Ansys.” (Hurry 17). Then, Hurry notes that “Abaqus, Ansys, and MSC Marc seemed to be used widely for rubber products design” (17). Various kinds of rubber need the curve fitting capability and the broad diapason of the material models. Furthermore, “the remeshing possibility can be a useful tool for large deformation and the working circumstances require the contact and self contact ability as well” (Hurry 17).
ABAQUS seems to be among the most popular software to apply within the scope of rubber processing. For calculations, the ABAQUS program assumes that the loads are proportional, that is, all load values differ in only one scalar parameter. Since the boundary conditions in the shells are specified in displacements, the standard Newton-Raphson method is used, which is the main algorithm used for nonlinear boundary value problems (ABAQUS Theory Manual). For similar examples of compression of hyperelastic tubes with circular and elliptical cross-sections, a three-dimensional approach is used in modeling. In addition to the shell, a three-dimensional model of an elliptical tube is analyzed, in which elements with parabolic shape functions and a hybrid shear stress composition are used (ABAQUS Theory Manual). In ABAQUS, the Riks-Chrisfield method can be applied to solve problems of supercritical behavior with both stable and unstable behavior beyond the stability loss.
Works Cited
“ABAQUS Theory Manual.” Engineering School Class Web Site. Web.
Barbera, Vincenzina, et al. “Serinol Derivatives for the Sustainable Vulcanization of Diene Elastomers.” Rubber Chemistry and Technology, vol. 91, no. 4, 2018, pp. 701-718.
Bergbreiter, Sarah and Kristofer Pister. “Elastomer-Based Micromechanical Energy Storage System.” ASME, 2006, pp. 1–7.
Cho, Hansohl et al. “Deformation Mechanisms of Thermoplastic Elastomers: Stress-Strain Behavior and Constitutive Modeling.” Polymer, vol. 128, 2017, pp. 87–99.
Formela, Krzysztof et al. “Thermomechanical Reclaiming of Ground Tire Rubber via Extrusion at Low Temperature: Efficiency and Limits.” J Vinyl Addit Technol, vol. 22, no. 3, 2014, pp. 213–221.
Hury, David. “Finite Element Software for Rubber Products Design.” International Journal of Engineering and Management Sciences, vol. 3, no. 1, 2018, pp. 13–20.
Maghsoudi, Khosrow et al. “Direct Replication of Micro-Nanostructures in the Fabrication of Superhydrophobic Silicone Rubber Surfaces by Compression Molding.” Applied Surface Science, vol. 458, 2018, pp. 619–628.
Volpe, Valentina et al. “Smart Behavior of Elastomeric Composites Produced by Injection Molding.” Applied Polymer, vol. 135, no. 44, 2018, pp. 1–7.
Yangthong, Hassarutai et al. “Role of Geopolymer as a Cure Activator in Sulfur Vulcanization of Epoxidized Natural Rubber.” Applied Polymer, vol. 137, no. 17, 2019, pp. 1–14.
Yu, Kunhao, et al. “Additive Manufacturing of Self-Healing Elastomers.” NPG Asia Materials, vol. 11, no. 1, 2019, pp. 1-11.