Introduction
Modern organizations encounter numerous challenges due to increasing global business rivalry, rapid changes in technology, changing consumer needs, and a higher need for quality goods and services than before (Laufer 2012, p. 218). One of the ways that organizations have adapted to remain competitive and relevant has been through the implementation of effective and efficient management systems. In the last few years, the role of project management in organizations has become a central point of focus in multiple industries including construction, administration, management, and product development, among others (Upton & Staats 2011, p. 3). However, most of these projects encounter problems that involve delays and excessive budgets. Some organizations consider such delays as normal, which has a negative impact on the overall performance of the business. Delays and excessive costs interfere with organizational productivity, quality, and marketing plans, which in turn, lower the competitive advantage of the firm (Kähkönen 2011).
The concept of lean leadership and management was first implemented in the manufacturing industry in order to enhance productivity and quality. The implementation of lean practices in project management differs from their implementation in manufacturing management. Projects are short-term and distinctive, and their implementation is carried out by teams that have clear and unique individual roles (Pettersen 2009, p. 133). Manufacturing, on the other hand, involves continuing and recurring functions that are operated by production personnel. Projects can be of varying nature and involve a level of creativity that increases the level of ambiguity, uncertainty, and complexity of the operations. However, projects and manufacturing share various features such as implementation by skilled individuals, scarcity of resources, and the requirement for planning, execution and control (Staats, Brunner, & Upton 2011, p. 383). This paper seeks to prepare a study to identify the impact of implementing lean project leadership methodologies in project management.
Research Objective
The study seeks to find out the success factors of implementing lean leadership in project management. The factors that will be examined in the study include organization culture, organizational readiness, management commitment, adequacy of resources, communication channels, and strategic approach in linking the changes to organizational objectives.
Purpose of research
The study aims at examining the impact of the integration of lean thinking in project management with the view to enhancing project productivity.
Research questions
- What are the necessary concepts of lean thinking in project management?
- Can the concepts of lean thinking enhance project productivity?
- What are the impacts of implementing lean project leadership methodologies in project management
Scope
Although lean techniques were originally in manufacturing arenas, the worldwide awakening to the benefits of lean has expanded the scope and today, all areas of business management including all processes involved in the production of goods and services, are looking for schemes or plans to implement or enhance lean management. Today, one is able to find lean management applied in hospitals, supermarkets, transport, and air ticketing services, government, infrastructure construction, plant maintenance and many more. The term “lean” may not be out rightly used, but the concept still applies and all this justifies the fact that the entire lean theory is more than a system incorporated into a business; it is the manner in which it functions wholly (Schonberger 2007, pp. 410). A business or organization will change its mode of operation from the previous technique and in introducing the lean technique, it will have to undergo a complete overhaul; a process that is long-term and not readily assimilated. It therefore requires both proper planning and progressive transformation of how a business or organization operates. Furthermore, proper structured and formatted learning have been observed as two pioneers for present day trade prosperity by playing a role in firms’ rivalry. By referring to the idea and the connection between studying and lean management, I state that in the previous two decades lean management has undergone advancement both in its world of application and nature. I state that present descriptions of lean conversation have unlocked written potentials for good judgments between research and development (Alvesson & Sveningsson, 2008).
Literature review
Lean business management is a method or strategy of doing business in order to achieve optimum conditions of values generated with zero squandering of resources or if misuse happens, it is minimal and controllable. There are three very essential factors that have to be clearly thought of and considered before a business or organization incorporates the Lean Business Project Management concepts into their already working systems. One of these has to do with the functions or more precisely, the reasons for incorporating these concepts. What glitches in the system will be resolved? Another significant factor is the process of lean transformation where a business analyses the worth of each phase and ascertains that they are effective, of value, sufficient, accessible and variable. The phases within must all be correlated. Manpower is also very important. Each process has to be under the management of a specific entity who can be responsible and answerable for operations. This way, operations are run more efficiently and effectively and can be constantly upgraded because it will be much easier to point out the areas that need addressing (Winter & Szczepanek 2008, p. 97).
It is globally acknowledged that there are five fundamental stages or phases encompassing all techniques associated in creation and implementation of lean management systems in businesses (Brulin & Nilsson, 1999). The term business is general because the scope of application is wide. The following are the phases (A Brief History of Lean).
- Phase 1- Evaluations in details of all the benefits customers can gain from every category of products or services. This is Identify Value.
- Phase 2- Detection and ascertaining all the sequences of actions needed in order to achieve the above mentioned benefits as per the categories of products and services in demand by customers. This is Map the Value Stream.
- Phase 3- Designing the sequences of phase two in detailed logical steps in order to achieve efficient and uninterrupted flow of products or services with varieties of incentives in order to attract customers. This is Create Flow.
- Phase 4 – Gathering data from customers’ demands information and covering all loop holes. This is Establish Pull.
- Phase 5- Redesigning phase 3 in order to achieve perfection. This is Seek Perfection.
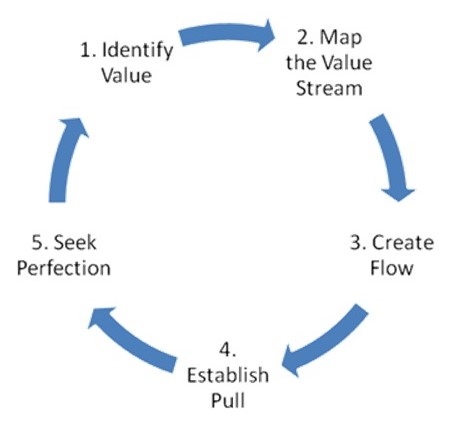
There are 4 phases of strategies in order to achieve or accomplish lean business project management (Benner & Tushman, 2003).
Phase 1- Fundamental stage – Identifying a Transformation Manager with roles to establish lean management in order to:
- Acquire lean methodologies from all sources including experts.
- Spread the good news about lean management to all stakeholders from within the company and all the associated customers in order to get support for establishing lean management.
- Start from low gear aiming to reach high gear momentum.
- Locate and record values and benefits and generate a plan how to achieve them.
- Commence the launching of strategies without any delay.
- Check results and record data without any delay.
- Go to top gear momentum and establish the lean business project management for the business concerned.
Phase 2– Establishing a structure in the business to allow smooth flow of benefits.
- Know very well the products and flow of benefits
- Establish lean marketing operations.
- Workforce in place must be assured of their job security and the benefits to reap from lean skills.
- Plan and establish growth projection.
- All sources of frustrations must be done away with/
- Make perfection your ultimate goal.
- Investigate all sources of stagnation.
Phase 3– Establish high tech systems to train and firmly adopt lean management philosophy (Björkman, 1997).
- Take advantage of the business goodwill.
- Establish a lean data sourcing and recording systems.
- Remunerate workers as per the good performance emanating from lean management.
- Make it a policy to live by the lean philosophy.
- All equipment and tools and data systems must be of high and professional standards.
Phase 4– Final stage to accomplish changes (Brulin & Nilsson, 1999).
- Customers and all stake holders must be groomed to support and take positive actions toward the strategies achievement.
- Expand scope of strategy globally.
- Establish team work in all areas of business operations.
The approaches used in lean thinking involve either full implementation of the practices or one of the tools namely rapid improvement events (RIE). Studies show that the RIE approach is more common than the implementation of full practices. This is due to the ease of organizing rapid improvement workshops in order to identify a variety of promotional actions ranging from “small, incremental quick wins, to longer term strategy changes” (Pinto, Thomas, Trailer, Palmer, & Govekar 1998, p. 34). The RIE approach has three phases. The first phase takes a minimum of two weeks and involves preparations, followed by a five day phase during which the required changes are identified. The final phase takes about four weeks to implement the proposed changes. Some of the advantages of this approach of lean thinking include fast returns on effort applied; visible prevalence; involvement of personnel, which promotes brain storming and staff morale; and minimal resistance because it does not challenge the existing leadership and management styles, compared to the full approach (Aziz 2011, p. 22). Implementation of the RIE also has its shortcomings. For instance, the quick decisions may lead to plans that are difficult to sustain since they are not integrated in the overall organizational objectives. To overcome this challenge, organizations either implement the complete lean practices, or employ multiple RIEs in various segments of the organizational, in addition to their alignment to the organizational objectives (Anvari, Ismail, & Mohammad 2011, p. 1588).
Methodology and Approach
Various qualitative research methodologies can be used for the study. This study will focus on the conceptual and exploratory design through the review of various literatures involving lean thinking and project management. The next bit will involve an analysis of organizational practices in project management. Based on the material gathered, the study will be supplemented with an in-depth case study design whereby a firm that applies lean thinking in project management will be identified for study. For comparison, two organizations will be identified for the study: one in the public sector, and the second from the private sector. This approach will be used to identify the benefits and limitations of using actual lean practices in project management for the company identified. However, since the research questions target the impact of lean thinking, it will be necessary to combine the various research designs, in order to answer questions regarding ‘what’, ‘how’, as well as, impact of the practice in project management. An overview of the research design is shown in figure 1 below.
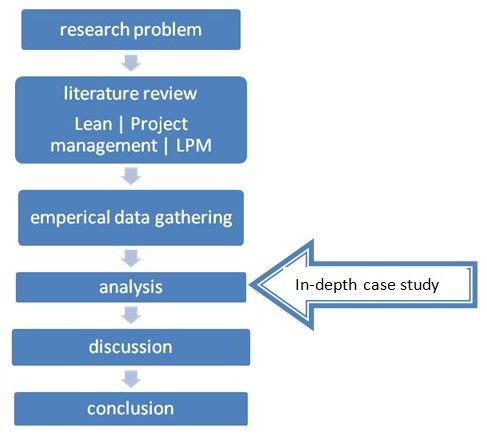
Research strategy
The exploratory bit of the research is aimed at improving on the limited supply of research on the implementation of lean thinking in project management. In addition, the information acquired will be vital in identifying other areas where more research can be conducted. The descriptive and case study research designs are vital in answering the research questions with regard to how the concepts of lean thinking influence the project management process.
Research approach
The qualitative study approach will be adopted due to its ability to provide analytical reasoning that can help the study to arrive at reliable conclusions. The qualitative study also provides a platform for the evaluation and comparison of concepts of lean thinking that are applied in project management. According to Aziz (2012, p. 5), a research employs two kinds of logical reasoning: inductive logic and deductive logic. While inductive logic observes the relationships between objects in order to arrive at theories, the latter focuses on the implementation of general theories to various cases. This research design will employ the deductive logic, whereby the concepts of lean thinking will be analyzed before examining their integration in project management.
Limitations
To begin with, lean is a wide topic that entails numerous details. The time, budget, resource, and personnel constraints imply that only a few concepts of lean will be studied. As such, the focus of the study shall remain focused on the five principles of lean thinking, and an additional two case studies to determine the impact of lean in project management. The second limitation involves the limitation of the study to an empirical research of only ten participants, and two case studies. This restricts the ability to generalize the results to a wider level. However, the participants in the empirical study will be selected from a list of consultants who are involved in multiple project management exercises, which will make their responses relevant and interpretable to a sizeable general context. The third limitation to the study involves the limited number of organizations that employ lean thinking in their project management, which limits the number of case studies to two.
Deliverables and Program
The study is influenced by a methodology proposed by Dubin (1978, p. 12), who devised a system for the evaluation of various fields including management, marketing and organization theory. Dubin proposed eight phases in his approach, though this study will only implement the phases that formulate reliable answers for the research questions. The phases to be examined in the study include: boundaries within which the theory can be applied; conditions under which the theory is operative; empirical indicators that make the propositions testable; and research that involves empirical tests of the predicted values and relationships. The evaluation of boundaries for the application of lean practices is due to the assumption that different projects require different applications of the concept of lean. Deliverables and program
The time plan and deliverables are as shown in the table below.
Table 1: time plan and deliverables
The interview process will involve asking a set of pre-determined questions to the interviewees. The interviewees will be identified from consultancies that take part in managing organizational projects. A pilot test will be conducted to determine if the questions are confusing, as well as, the duration of time that will be spent on each interview. The questions used in the interview are shown in appendix 1. The variables to be studied in the case studies include: organization culture, organizational readiness, management commitment, adequate resources, clear communication, and strategic approach.
Conclusion
The implementation of lean thinking in the provision of services varies from its use in manufacturing. While lean practices are used to standardize processes in manufacturing, service organizations employ a narrow set of tools and techniques to increase value of their systems. This study seeks to identify various approaches of implementing lean in the management of projects and their impact on the entire process by researching on lean practices, project management, and case studies that examine the practice of lean thinking in an organizational setting. Studies show that lean thinking enhances organizational processes such as team working, due to the involvement of personnel in problem identification, problem solving, and remedy implementation. The implementation of lean practices in various sections of the organization ensures process focus and understanding, which promotes the implementation of relevant remedies that reduce inefficiencies in the process. Challenges to the implementation of required change include the lack of resources necessary to effect the change, resistance to change from staff and management, lack of commitment to the change process, and slow pace of change (Radnor, Walley, Stephens, & Bucci 2006, p. 3).
The case studies should help to identify the success factors of implementing lean practices in project management. Studies show that some of the notable success factors include organization culture, organizational readiness, management commitment, adequate resources, clear communication, and strategic approach. According to Radnor, Walley, Stephens and Bucci (2006, p. 4), the development of a culture of continuous improvement that involves staff members enhances the success rate of lean leadership in project management. Organizational readiness involves developing a vision of the change process in order to formulate realistic time plans, assist staff in recognizing the impact of the change, and development of realistic measures to analyze the impact. Dedication and involvement of the management in the program also helps to shape the progress of the change process. The availability of adequate resources like finances, time and skilled personnel are vital for the successful implementation of lean practices. The empirical portion of the study examines the role of consultants in project management, as they are key participants in the implementation of lean process. Effective communication can be achieved by ensuring common language and understanding in the transformation and development process. This, in addition to a strategic approach, helps to synchronize the organizational changes with the strategic goals of the organization and make them a vital part of the organization’s core activities (Henderson & Larco 1999).
In conclusion, the study seeks to identify the instances that lean has been effective, and its impact on the project management process of the identified organizations. The study will also help to reveal the factors that make organizations suitable for lean, and how it works. In addition, the study will provide information regarding the impact of lean practices in the process of organizational continuous improvement.
Reference
Anvari, A., Ismail, Y, & Mohammad, S 2011, A Study on Total Quality Management and Lean Manufacturing: Through Lean Thinking Approach, World Applied Sciences Journal, vol. 12, no. 9, pp. 1585-1596.
Alvesson, M & Sveningsson, S 2008, Changing Organizational Culture: Cultural Change Work in Progress, Routledge, London.
Aziz, B 2011, Improving Project Management with Lean Thinking? Sweden: Linköping University Electronic Press.
Benner, M & Tushman, M 2003, Exploitation, Exploration, and Process Management: The Productivity Dilemma Revisited, The Academy of Management Review, vol. 28 no. 2, pp. 238-256.
Björkman, T 1997, Management, SNS, Stockholm.
Brulin, G & Nilsson, T 1999, Teamwork in the Automobile Industry – Radical Change or Passing Fashion? Routledge, Basingstoke.
Dubin, R 1978, Theory Building, 2nd ed, Free Press, New York.
Henderson, B & Larco, J 1999, Lean Transformation: How to change your business into a Lean Enterprise, Routledge, London.
Kähkönen, K 2011, Project Perspectives, The annual publication of International Project Management Association, vol. 33, no. 1455, pp. 10-48.
Laufer, A 2012, Practices for Project Leadership. In Mastering the Leadership role in Project Management, Upper Saddle River, New Jersey: FT Press, pp. 213-236.
Pettersen, J 2009, Defining lean production: some conceptual and practical issues, The TQM Journal, vol. 21, no. 2, pp. 127-142.
Pinto, J, Thomas, P, Trailer, J, Palmer, T, & Govekar, M 1998, Project Leadership: from theory to practice, Four Campus Boulevard, Newtown Square, Pennsylvania: Project Management Institute Headquarters.
Radnor, Z, Walley, P, Stephens, A, & Bucci, G 2006, Evaluation of the Lean Approach to Business Management and its Use in the Public Sector, Edinburgh: Warwick Business School, University of Warwick.
Schonberger, R. J 2007, Japanese production management: An evolution-With mixed success, Journal of Operations Management, vol. 25, pp. 403–419.
Staats, B, Brunner, D. J, & Upton, D. M 2011, Lean principles, learning, and knowledge work: Evidence from a software services provide, Journal of Operations Management, vol. 29, no. 5, pp. 376-390.
Upton, D, & Staats, B 2011, Lean knowledge Work, Harvard Business Review, pp. 1-10.
Winter, M., & Szczepanek, T 2008, Projects and programmes as value creation processes: A new perspective and some practical implications, International Journal of Project Management, vol. 26, pp. 95-103.