Introduction
This chapter serves as an introduction to the proposed project about its objectives and reasons for the project. It will also discuss the components of the essential supply chain practices showing how effective management of the supply chain may reduce cost and time overruns and subsequent litigations in the construction industry, especially in the United Arab Emirates.
The rationale for the research paper
The manufacturing process is an intricate one with several components being its constituent. The link that ensures a connection between the various elements in a manufacturing process is known as Supply Chain Management (SCM). In the construction industry, this link is very important. In this industry, some of the components of the supply chain include the main contractor, the subcontractors, the clients, the engineer, and the project facilitator (See figure 1)
When there is mismanagement of this construction supply chain, several consequences arise, some of the most significant being cost and time claims among the partners with subsequent litigation. The construction chain should run in an environment where there is optimized cost, time minimization, and where the products are up to the required quality (McDermott & Khalfan 2008, p. 45; Weber, Dalluege, Shamsi, & Menconi 2006). McDermott and Khalfan (2008, p. 45) “advocate the use of the SCM philosophy as a mean to effectively reduce the overall construction costs”. Lau, Huang, and Mark 2004(2004) defined the concept as “to improve the performance of the SCM Concept, it is very much required to bring autonomous companies together.”
Since the origin of supply chain management in the 90s, the application has largely been in the manufacturing industry, with the construction industry lagging (Qi, Boyer, & Zhao 2009, p.670). (“Since the early 1990s, manufacturing companies around the world have implemented a lean production strategy to increase their competitiveness”). In this industry, the purchasing concept has largely dominated, with this being because of poor coordination or lack thereof. The result of the poor coordination of the various members of the construction supply chain has resulted in delays in construction projects, an increase of the original estimated cost of the project, and overall effects on the quality of the final project. Due to these negative effects of poor supply chain management in the construction industry, the construction companies and other members of the supply chain are liable to time and financial claims from the other parties.
Another observation in this industry is the lack of clear strategy among the various construction companies on the activities that need to be integrated and those that need outsourcing (Laeequddin 2009, p. 22). (he listed nine important supply chain concerns such as lack of sophisticated Information and Communication Technology (ICT) infrastructure, insufficient integration due to lack of trust and collaboration among supply chain stakeholders, and thereby lack of supply chain effectiveness and efficiencies). For example, a firm might outsource the electromechanical activity in one project and integrate it in the other, thus leaving no chance for the company to develop its resources to strengthen its capability in that field or to sustain the relationship with the subcontractor. The construction companies are also, in most instances, unable to foresee risks such as political instability, civil unrest, and the firm’s reputation, the sustainability of relationships, human risks, and natural disasters.
One reliable way of minimizing the above problems include companies looking at the supply chain from different perspectives other than being a purchasing tool that is the traditional outlook of the supply chain in the construction industry. The supply chain has the effect of linking inter-departments together (See figure 2) with an overall improvement and change in a company’s strategy.
Another positive effect is the increase in coordination between the company and its supply chain partners. This will directly lead to finish the construction project within the predefined cost, time, and quality standards and up to the client’s satisfaction. As a result, it will minimize the litigations between various parties working on that project and thus the relationships are sustained.
Eriksson (2010, p. 396) in his literature discusses SCM techniques and states that they have been adopted in the current business market to help save on time and revenue. (Concurrent engineering increases the contractors’ understanding of customers’ needs and improves teamwork and joint problem solving, resulting in significant time savings). This is according to him is a timely war of revolutionizing the market and ensuring maximum utility for the stated factors of production. The adoption of the SCM in the construction industry and its affiliates such as the built environment is, however, not as simple as indicated above. Researchers state that it requires the introduction of innovations, complete know-how of the market, and the knowledge to manage a difficult and animated network of organizations that operate to assemble several contradictory business objectives. In this research, I will discuss why there is no coordination between those parties, what activities to be integrated and those to be outsourced, how to analyze the risks associated with each project, and other supply chain issues.
Choice of topic
The construction industry in the UAE has seen several massive developments of late and attracted the attention of construction industry managers the world over. Despite the industry starting on a traditional approach, new technologies have been adopted with new concepts being introduced. Research into this industry’s supply chain management, however, has not been forthcoming. The purpose of the research, therefore, is to establish a baseline for the studies in the supply chain management in this field and establish probable obstacles to the implementation of the supply chain management in the region and industry. The UAE hosts the world, fastest-growing construction industry, and therefore the study of the management of supply management is of benefit to other regions of the world that are on the verge of such a construction boom.
Purpose of the research paper
The approach to supply chain management in the construction industry in the UAE has been cautious, with few companies doing it as stated above. The purpose of this research, therefore, will be to evaluate the awareness of the industry in implementing the construction supply chain, the obstacles facing the industry, and reasonable benefits that can be realized in the proper implementation of this concept. The study will mainly focus on the concepts applied in the UAE construction industry about SCM.
Aims and Objectives
The research focuses on the factors below as its aims and objectives.
- To critically review and appraise existing literature on supply chain management and the relevance of this to the construction industry in the UAE
- To establish the extent of use of the supply chain management in the UAE construction industry and the limitations that exist its full implementation in this industry
- To establish the effectiveness of good supply chain management practices in the UAE and their effect in reducing litigation in the construction industry
- To provide appropriate recommendations on the most effective ways of implementing SCM strategies in the relationships between the parties in the construction industry in the UAE
Research Hypothesis
The hypothesis for this research is that good management of the supply chain is useful in avoiding time and cost variations, and thus litigation among the construction supply chain partners
Research Methodology
The research methodology for this paper will mainly be used to compare the use of supply chain management as presently exists in the world, and that in use in the construction industry in the UAE. The chapter will therefore include research design, sources of data, and tools for data analysis. The research will adopt a descriptive survey design to investigate the construction industry in the UAE. The research will cover the construction and supply chain partners. The research design will entail data collection from a specific population of the partners who will be used to determine the position of that population concerning various variables. A random sample will be collected including project managers, MEP and Cladding subcontractors, clients, the engineer, and the project facilitator. After collecting all the data, the researcher will proceed to code the collected data for purposes of analysis. Descriptive and statistical procedures will be applied in analyzing this data. Percentages and means will be adopted as statistical analysis procedures for this research. Finally, the results will be presented in a summary form using bar graphs and frequency tables. The results of the survey will then be analyzed statistically.
Literature Review
Overview of Supply Chain Management
According to Lummus and Vokurka, a supply chain is a sequence or order of flows and processes, which when considered contribute to the meeting of the customer’s final requirements (1999). (Supply chain encompasses a series of events and processes at various levels leading final customer service). The supply chain consists of several partners, with the main ones being the producers and the suppliers. It also includes other participants such as retailers and consumers, all of who ensure a flow in the services or products in the industry in focus. The manufacturing industry was the first to adopt the concept of supply chain management. As Geoffrey et al. state, Toyota was among the first companies in any industry to adopt Supply chain management in its delivery system (2004). (In the manufacturing sector, particularly automotive, Toyota Production System or Lean Manufacturing became very popular…When similar principles when applied to supply chain, it helps to reduce cost). The effects of this timely adoption of SCM by the auto manufacturers increased production line interaction with the inventories used during this period significantly reducing.
Cooper and Ellram (1993, p. 22) introduced the Triple P (People, Planet and Profit / Prosperity) concept later on as shown below, which was also significant in the SCM development (See figure 3).
According to them, triple p deals with people, planet, and profit, and this has a great impact on the SCM processes but there, are still additional characteristics which may be considered for example social, environmental, and financial problems (Cooper & Ellram 1993, p. 17). (Triple P deals with people, planet, and profit, which has a great impact on the SCM processes but there, are still additional characteristics which may be considered for example social, environmental, and financial problems). Some of the other authors that detail the use of SCM include Love, Irani, and Edwards (2004, p. 53) who provide the literature that is necessary for the understanding of SCM. (supply chain management is an emerging concept in the construction industry…the proposed model is not different from some of the construction procurement systems).
Hong-Minh, Barker, and Naim (1999, p. 91) differentiate SCM key decisions in three ways. (There are three essential points which constitute business processes:
- the process always has a customer, internal or external,
- processes may cross organizational borders, and
- process must be evaluated from the customer’s point of view)
They state that they constitute Supply chain business process, supply chain network structure, and the supply chain management. Any industry has to undergo a series of changes and adaptations to ensure that it integrates SCM in their existing systems. It is, therefore evident that there are differences between the traditional management strategies and the Supply Chain Management as illustrates by McDermott and Khalfan (2008, p. 50). (The historical or traditional procurement process was the acceptable process in the construction industry for many decades. The process had made a specific culture within the construction industry relying on a mere lowest price focus and project-based approaches contributing towards inefficiencies of the construction process).
Some of the other authors that highlight the principles of SCM include Maturana, Alarcon, and Vrsalavic (2000, p. 13) who stated seven principles that were significant in the SCM. (Some of the principles suggested in the approach to supply chain management will be discussed in this paper). They include Segmenting customers to the industry based on service needs, customizing the logistics network, listening to signals of market demand and plan accordingly, differentiating product closer to the customer, sourcing strategically, developing a supply chain technology strategy, and adopting channel-spanning performance measures. According to them, these time-tested principles combine to compel any company to adopt the SCM in their organization and that each of the principles has benefits. These benefits are three in each of the principles and include growth of revenue, utilization of assets, and cost reduction. The more than obvious fact that a company should tailor the supply chain based on the requirements of the clients is stated, and this is explained as leasing to the improvement of revenue growth in the organization (Anderson et al. 2007).
According to Jalbani (2010, p. 16), there are several viewpoints encountered in an industry, and these include the 4C’s in supply chain management that he listed as being communicative, coordinated, co-operative and collaborative viewpoint as shown in figure 4. (…and 4C’s in supply chain management these are: communicative, coordinated, collaborative and co-operative).
Barriers in Implementation of Supply Chain Management
No clear strategy for the project
The first challenge that is evident in the literature review is that of the absence of a clear strategy for the projects that are in progress in the construction industry. As Decelle et al. state, the construction industry is one of the most disorganized in the world and this holds in the UAE (2007, p. 74). (The UAE has one of the largest and most organized construction industries in the world). In most of the projects that have been carried out, there exist no clear strategies on the course of the project about time, materials, and cost. The industry, however, relies on estimations of cost materials and labor, and this often exceeds the capacities of the companies carrying out the tasks. In most of the researches that were reviewed, the presence of strategic planning in the implementation of a project seemed to be part of good supply chain management. The construction industry, in general, is known to underperform its potential with the most cited reason for this being the unavailability of a concise project strategy. Since the application of strategy in the construction industry is demonstrated to save on resources if applied could also lead to reduced costs and time of completion of projects.
Lack of coordination between partners and among the departments of the same partner
The other evident problem afflicting the construction industry in the UAE and elsewhere, in general, is the lack of coordination between partners and among the departments of the same partner in the construction industry supply chain. The construction industry all over the world is characterized by opportunistic behavior with little if any vertical cooperation. Lack of horizontal cooperation is also evident in the construction industry, with many firms and organizations only working to maximize their profits. In their paper, they observed that individuals work best when they deal with different people in the construction industry, and are, therefore, likely to change the people they interact with during projects. The researchers used the game theory to explain the phenomenon that they observed people being able to deal with different people when working on projects. In one of the experiments, managers in large construction companies individually rarely deal with the same individuals as subcontractors. As Lo¨nngren, Rosenkranz, and Kolbe state, repeated personal level contacts across organizational boundaries is enough for a minimum level of courtesy and consideration between parties (2010, p. 408). (Strategic partnering can be defined as long-term cooperation between two or more organizations to maximize the effectiveness of the respective resources and to reach specific business objectives). This strategy applies to the construction industry. It may be accomplished through good supply chain management.
Poor communication between partners and among the departments of the same partner
Most of the problems experienced in any project in the construction industry may be attributed to some extent to the breakdown in communication between the partners (Hong-Minh, Barker &Naim 1999, p. 88; Khalfan, McDermott & Swan 2000). (Communication/information problems: as the different trading partners cannot completely trust each other, they try to limit the exchange of information as much as possible.)Since this industry has many key players involved in the delivery of a single project, communication serves to link them together and provide a basis of interaction and completeness. The stakeholders are in a dynamic environment that is the construction industry, and this is driven by the existence of contracts (Hong-Minh, Barker &Naim 1999, p.87). (The TSMs clearly showed a problem in the construction culture, namely the presence of poor/adversarial relationships between key players, such as the client, main contractors, architects, and sub-contractors). The communication breakdown can exist at different levels of the construction cycle, with different individuals being involved.
Some of the areas in the construction industry where there need to be improvements include the communication between the building team, the project teams, and between the project manager and contractors. If communication is improved between the above-mentioned parties, the output would be greatly improved and better innovations and technical solutions found for some of the problems in the construction industry.
Lack of trust between partners and among the departments of the same partner
Trust is also a significant influence on the output of any industry, and for such an industry such as the construction industry where many stakeholders exist. It defines the relationship between them. With so many financial and material components at risk, the relationship between the participating partners in the industry can be that of suspicion between partners and within an organization anywhere in the chain of supply. There has been little focus on previous studies on the effects of trust within the supply chain in construction projects. The effects have however been evident in the form of project delays and litigation. They describe the main reason for the rampant lack of trust within the industry as the complexity of this industry and the magnitude of fragmentation.
Poor Management of Tendering Stage
The tendering stage in the organizations participating in the various chains in the construction projects has been one of the limiting ones when it comes to the completion of construction projects. This stage has been the subject of controversy in this industry in the past, with courts being used as a tool to solve some of the difficult problems. Can good supply chain management lead to improved tendering and management of this stage? Many authors have dwelt on this question for years in the construction industry, and this has resulted in an unending wealth of knowledge on the same. Some of the authors argue that the tendering stage is significant in the construction industry and any organization or business that succeeds in obtaining a working tendering strategy ends up succeeding in the industry.
Jalbani recognizes several areas in tendering where the mismanagement may occur, and these are subject to control along with different areas too (2010, p. 10). (The construction industry and highlighted the trust of the built environment industry on the competitive and transparent tendering process for the subtle work. It also illustrated the sign to the related and different approaches that generally existed in the process). Various members of the construction supply chain in the industry have criticized the awarding of tenders, with each side citing their reasons for the apparent failure. One recognized outcome of poor tendering is the escalation of coast in the construction projects and the outcomes where poor tendering contributes to high prices. In such cases, the contractor is subject to litigation from the clients and different parties along the chain.
Poor Procurement
Another recognized stage aside from the tendering stage is the procurement stage that follows. This step is an equally significant stage requiring similar attention and management, and should anything go wrong, a lot is at stake during the construction process. As Arif, Egbu, Alom, and Khalfan state, the procurement efficiency may determine the level of performance in a construction company (2009). (…the efficacy in construction determining performance)This method is also under the influence of many elements and people both within and without the construction industry. These may combine to ensure a positive or negative construction project outcome. The procedures used in the procurement of materials in the construction industry are tedious and with many parties involved. This argument is one of the reasons why this stage is a source of litigation for construction companies. As they claim, one of the major sources of litigation in the procurement stage is the delays experienced due to the whole process. This may be attributable in part to the poor tendering and the procurement process on many levels of the construction ladder.
Separation of design phase from the execution phase
The design phase of any project is very important and defines the expected outcome in the construction industry. The design of a project gives the client the expectations that they should have of the contractor and the kind of work that is to be expected. Due to the fragmentation that is existent in this industry, however, the design phase may be separated from the execution phase in a variety of ways. The organization of the two phases may be the only separation that exists, and this causing a discrepancy between the expected outcome and the actual outcome. In some of the arrangements in the projects, different companies may be involved in the design phase from those executing the ideas. Some argue that this kind of separation ensures maximum benefit for the parties since the companies can specialize in a single thing and do it to their level best. However, some researchers have argued against this notion and have found out that there are delays that may be experienced if the two processes are delinked.
Separation of the design phase from the execution phase has largely resulted from the presence of subcontractors in the industry. The establishment of subcontractors means that there are firms that have sub-specialized in particular areas, and the main contractor only deals with the structural and managerial aspects of a project. The establishment of a good supply chain management should be focused on linking the two phases to ensure continuity and reduced delays.
Lack of partnerships between construction supply chain partners
Lack of collaboration between supply chain partners has also been singled as a cause of litigation indirectly in the construction industry. As stated above, the industry is dominated by several subcontractors and parties, all involved in the same construction process. According to Jalbani (2010, p. 6) and Grant (2010), the traditional organization in the construction industry involved the execution of the projects by the main contractors through laborers that they hired directly (2010, p. 6). (Traditionally, construction related management focused on supply chains each representing a process such as built-up, delivery, etc.). This has, however, been overtaken by the modern practice of hiring subcontractors to do the main job for the organization that is hired as the main contractor.
Based on the fragmentation stated above, a single subcontractor can frustrate the efforts of other subcontractors or the main contractor in a project, causing an overall project delay. The existence of non-collaboration between the subcontractors may also be linked to the high litigation observed in this industry in the recent age. Jalbani states that, due to the existence of very strong cost competition and the traditional adversarial customer-supplier relationship, the actors of the construction project usually change significantly from one project to another complicating collaboration between these actors (2010, p. 23). (organizations approach a contract with a non-adversarial attitude). The reason for the lack of collaboration between the partners in the supply chain in a construction project may be due to several factors, but these are mainly due to competition and strengthening of profit margins.
The construction industry has seen the rise of many companies offering similar services and instilling competition in this industry. Despite some of the partners in the supply chain offering complementary services, there has been little partnership between them, which has affected the industry in one way or the other. Maturana, Alarcon, and Vrsalavic quoted several authors that suggested that the construction supply chain is important in propelling innovation and sustaining improvements in the construction industry (2000, p. 11). They claimed, “For an organization to set and achieve ambitious performance targets, some of the recommendations in the report included the adoption of strategic methods, such as partnering, which has for many years been applied in the manufacturing sector successfully” (Maturana, Alarcon & Vrsalavic 2000, p. 11; Bankvall, Bygballe, Dubois, & Jahre 2010, p. 391; Mohammed 2003, p. 18). (The methodology supports an interlinked relationship between onsite management).
Partnering as applied here meant the use of integrated production terms and continual monitoring of the effect of performance improvement measures. Partnering has successfully been applied in other industries such as the manufacturing ones along their supply chain, and this has ensured that they become the best and increase output. It could be done temporarily where contractors partner on a project or even temporarily where mutual benefit is considered. Partnering on a single project was categorized as ‘project partnering’, while long-term partnerships were regarded as ‘strategic partnering’ by Maturana, Alarcon, and Vrsalavic (2000, p. 11) (Objectives as a pre-selection/selection system). They suggested that before the organizations and companies could partner, they should first merge their objectives to ensure that there is mutual benefit in the partnership, problem-solving measures in the partnership, and improve their organizational culture to ensure that it works for mutual benefit.
Incomplete and unfair contracts agreements among the partners
Incomplete and unfair contract agreements among the partners in a construction chain have been present for decades, and this has led to the breakdown of many partnerships. The major causes of unfair contracts include the presence of clauses in the partnership agreements that are unclear on both sides of the partnership leading to trust issues. Some organizations in the construction industry have entered into a contract with other organizations, and the terms of the contract, may not be clear to one of the partners in the partnership. This has led to disagreements in the past between these partners, leading to legal battles, which are costly and end up delaying the construction projects. As Blos, Quaddus, Wee, and Watanabe claim, the construction industry is one that is characterized by contract agreements between the interacting companies, and though this has its advantages, unfair agreements constitute some of the major shortcomings of the practice (2009, p. 250). (Contracts mark the nature of agreements in this field).
When a firm is agreeing with another organization of its nature or one that has similar objectives, the terms of the contract have to be spelled out for both partners. In the case where the two parties fail to reach an agreement, several options are presented depending on the type of relationship that exists. Dainty, Briscoe, Millet, and Neale suggested that the lack of clear strategies in the construction industry has meant that the participants are free to engage in any practice that they wish, and this has driven the existence of unfair agreements between the partners (2004, p. 193: Aloini, Dulmin, Mininno & Ponticelli 2012). (Of the construction sector on competitive tendering for subcontracted work and drew attention to the adversarial attitudes that commonly exist between main contractors and their suppliers). Albaloushi, Helal, and Skitmore suggest that the unfair practice has been present for a long and needs to be brought to an end through legislation to streamline the industry (2008, p. 67). (The construction industry here needs revision through legislation). One of the measures that have been suggested is the adoption and utilization of supply chain management strategies, which are effective in other industries around the world.
In the UAE where the construction industry is abuzz with activity, many organizations working here are foreign and working under the supervision of their mother companies elsewhere in the world. This means that the rules may be applied in their favor. Dubai, one of the states constituting the UAE has embarked on an ambitious plan to legislate the laws governing the construction industry. This move is aimed at streamlining the sector to ensure that the local organizations are protected from unfair contract terms with their partners. Dubai and Abu Dhabi are two of the emirates with the largest share of investment in the UAE, which is estimated at 78% of the total investments in the UAE (Jalbani 2010, p. 31; Segerstedt & Olofsson 2010, p. 350) (Focus on the two emirates that hold about 78% of all the investments in the UAE). Based on this, the industry must be protected from exploitation through unfair and incomplete agreements between the participants.
In the previous decade, the existence of construction partnerships in the industry was not as rampant as the present experience, and the organizations used to work in exclusion. This meant that any agreement or contract was between the contractor or company and the employees (Olsson 2000, p. 3). In the current state, however, the fragmentation has meant that the existence of contracts and agreements is unavoidable. The adoption of adequate supply chain management is one of the things that will ensure that dealings between organizations in the construction industry. This will be beneficial to the companies working in the UAE construction industry.
Lack of astute project managers
Project managers are a significant factor in the success of any industry, and as such determine the success observed here. In the construction industry, for example, the success that some companies have established can be attributed in part to successful management. Faridi and El-Sayegh claim that some of the most important functions of a manager in project management include the development of skills that will ensure the success of a project (2006, p.1165) (a manager should therefore be responsible for the functioning of the project in…). While these qualities may be present in several people, those processing them may not necessarily make good managers. The construction industry, in particular, is one that needs adept management to ensure that the projects are completed on time and that any challenge that arises is dealt with amicably. One other characteristic that the project managers are required to have is that they need to be astute
A lot of training has been done for project managers, with the job description being very clear. However, there are discrepancies in the results on the field and the actual performance of the managers, with most of them being involved in activities that do not necessarily benefit their organizations. The figure below shows the four basic functions of managers.
Over the last decade, research done on the role of management in the construction industry revealed that the managers are the reason for the success and failure of most organizations. To ensure that decision-making is inclusive in management, the construction companies have embarked on teams and boards that are involved in managing their activities instead of relying on a single individual. This is the case with most of the construction companies in the UAE (Al-Hajj & Hamani 2011, p. 267; El-Sayegh 2008; Jaffar et al. 2007, p. 256). (The material waste in the UAE construction companies is a major problem…). Whereas this method of management has improved the quality of decisions made, the time taken for consultations has increased leading to slow decision-making. It is, therefore, essential that the construction companies elicit the control of managers that are astute in their decision making and planning.
The construction companies and any other companies that engage in a form of trade have four basic functions of managers, and these are planning, leading, organizing, and controlling (Laeequddin 2009, p. 26). A project manager should be able to perform all these functions for the organization to succeed in its quest and establish itself. Most researchers agree that a project manager and their ability to perform these functions make one of the most important factors in project success. Some continued and observed that good project management by the managers can reduce costs by as much as 10% (Olsson 2000, p. 3; Mitra, & Tan 2012, p. 321). This is despite little literature existing on the role played by the construction project managers as compared to other industries and trades. The leadership styles have been the subject of several studies, and these relate directly and indirectly to the function of managers (Northhouse 2010). One outcome of poor leadership styles in the construction industry is the apparent lack of leadership that inspires other employees to work towards the achievement of organizational goals. This will then be discussed below with the probable causes.
Lack of leadership that inspire the employees
As stated above, the construction industry needs leaders that inspire the employees below them at various levels. In the recruitment of leaders in this industry, one of the requirements that are stressed is the technical knowledge related to the subspecialty in the industry and not on the qualities of leadership processed. This means that though most of the leaders in this industry may be competent when it comes to the execution of the projects, the lack of or presence of inadequate employee interaction in their training limits their employee motivation. The employees may therefore develop an organizational culture that is not beneficial to the organization. This will then lead to the poor output. In some of the studies on construction management and supply chain management, the motivation of employees was recognized as a major drawback, with the source being high up in the management. Unlike in other industries where the managers are specially trained on the motivation of employees, the construction industry is relatively poor at this. This has resulted in the litigation observed in the sector and the high cost and time wastage.
One way of arresting the situation and ensuring that the industry achieves the best in terms of management is the institution of proper supply chain management. In the UAE, for example, the presence of a large number of organizations and companies participating in the construction industry has led to the development of the need for many construction project managers. Since the training is not up to the standard, the managers are just workers who excel in one area or establish their own company and are not necessarily trained on the managerial aspect. Strategic supply chain management in this place would ensure that the managers are equipped with the best skills on how to motivate the employees and the subcontractors below them.
Inability to know the personal needs of employees
In the same area of management, organizations have been accused of being oblivious to the needs of their employees. This fact about the industry has led to the development of many issues among the employees and between them and their superiors. An observation is that the management is not aware of the personal needs of the employees. More frequently than not, this has resulted in go-slows and other activities that may slow down construction projects. Almost all of the construction firms in the UAE have witnessed a form of action by the workers demanding what they consider their rights.
One of the suggested reasons why the construction companies are unaware of their employees’ personal needs is due to the nature of interaction that exists between them. In most of the construction projects taking place in the UAE, and especially in Abu Dhabi and Dubai, the employees are employed through employment agencies and not directly by the contractor. This means that the managers that are working with them on the projects are not aware of their problems. This is one of the reasons for the poor performance of the industry because of the delays. The relationship between the employees and the organizations has also been the subject of many legal battles as the employees seek compensation where their rights were interfered with. Supply chain management should be an adequate method of dealing with such problems ensuring that managers are aware of their employee’s needs.
Poor Risk Management
Another factor that has resulted in the poor performance of the construction industry worldwide is the poor risk management that some of the players have portrayed. In the UAE and elsewhere, ambitious projects are being rolled out. Some have however remained on the drawing board due to the inability of the industry players to take the necessary risks and ensure that the projects are completed. In the UAE, some of the projects that have stalled have increased, with the bulk of them stalling in the past decade. The stated reasons for the stalling of these projects include the harsh economic status experienced, especially in the wake of the global financial crisis. This qualifies as one of the factors that have discouraged risk-taking in the construction industry with several projects currently.
For any organization that aspires o be successful in the industry, there must be an analysis of the strengths, weaknesses, opportunities, and threats, and this should then be used to evaluate the amount of risk that needs to be taken. In the past, companies that can manage their risks have emerged victorious in the field and managed to conquer the industry. Despite the availability of other factors determining the success of an organization, the ability of the management to take risks is important in the success path of the industry. The institution of proper strategies in the supply chain management may improve the risk-taking and risk management of organizations in the future.
Daily operations are not organized
Another recognized problem of construction companies in the UAE and elsewhere in the world is the lack of organization and coordination of the daily operations within the industry. The planning and scheduling of activities are one of the activities that hinder the performance of the construction industry in the UAE, and the planning in the industry has not been adequate and well-controlled, with different parties involved both directly and indirectly. This has resulted in the wastage of time between the planning and execution phases and an overall delay in the delivery of projects. Another of the effects of poor planning and coordinated planning is the incurring of extra costs. This pushes the construction funding to a higher than expected limit drawing legal implications, and this being a basic principle, it should be reduced (Jalbani 2010, p. 9; Vrijhoef & Koskela 2000, p. 172). (The most vital goal of the SCM concept is the full protection and fulfilling of consumer requirements, optimizing the profit for the company, and reducing the extent of waste in terms of three basic principles: time, cost, and quality.)
Another stage of the construction process that is often poorly organized and coordinated is the execution of procurement and commercial activities such as contracts and in purchasing. Most companies that were surveyed in a particular survey were found to be dependent on a single criterion for awarding contracts and tendering. This is observed to be a poor influence on the time and cost for the projects, with the overall result being discouraging. The poor organization is recognized as being a source of litigation in the UAE and elsewhere in the construction companies, and the adoption of strategies in supply chain management is a recognized solution.
Planning and scheduling of activities emerge as a necessity in any project in any industry. If organizations are disorganized at this stage, the whole period of the project may be full of disappointments for the management. Some of the probable ways of ensuring that the firms and organizations involved in the construction industry as proposed by Chan, Chan, and HO include the adoption of supply chain management strategies that will ensure adequate planning (2003, p. 131). (Adequate planning is one of these strategies…)If an organization managed to schedule her activities during a construction project based on realistic factors, it is possible to provide an accurate period for completion of the projects to the clients and other interested parties. This would also allow for more time so that an organization works at a rate that is manageable on their side.
Other activities that an organization may be disorganized on including the carrying out of finishing services such as blockwork, plastering, painting, application of marbles and tiles, ceiling construction, and cladding among others. If these activities are delayed, the entire project may be delayed with the above-stated effects. Most of the construction projects in the UAE that have been delayed or are experiencing delays of any form have one of these stages to blame. Vidalakis, Tookey, and Sommerville (2011, p. 69) suggested that one way of avoiding the delays is adequate planning beforehand as stated above. A supply chain should be constructed in a way that any delays are prevented and adequately tackled.
The laying of concrete in the construction of slabs, beams, and columns may be delayed because of the disorganization in a company as stated above. Some of the other areas that may experience delays include the execution of electrochemical activities and technical activities such as drawings, material submittals, and requests for information. These carry a lot of significance in that the quality of the final project is dependent on the accurate execution of these functions. The development f a supply chain management strategy in the industry is a move that the researchers have suggested to be a deterrent to disorganization (Wong & Fung 1999, p.206; Jalbani 2010, p. 35). (Supply chain environment two or more organizations independently to work jointly can align their processes, to gain more value for the end customer, however, this can only work if organization involve should act as a single entity that means organizations must collaborate intensively). Quality of work is assessed in several ways in the construction industry, but observation is that the work is applied only applied to construction activities though it should cover all other activities. For this move to achieve the desired course, there should be adequate supervision in the industry.
Current Status of UAE Construction Industry
According to Jalbani, “The application of SCM in the UAE construction industry is still infancy, most of the researchers focus on the business process projects and little or no research has been done on the UAE construction industry” (2010, p. 31). He continues to state that, “As SCM is not a new concept in the business community and for the UAE construction industry” (Jalbani 2010, p. 31; Cheng et al 2010, p. 400). The current practice in the UAE is the traditional form of management in the construction industry. This is also evident among the neighboring countries.
Conclusion
The construction industry in the UAE is experiencing several challenges, despite the boom in construction over the last decade. The problems that different authors in the literature research have listed are manageable through adequate management policies and especially if the supply chain management strategies are adopted. It is the goal of this research to establish whether good management of the supply chain is a way of ensuring that the problems are dealt with.
Research Methods
Introduction
This chapter deals with the approach that will be used to carry out the research and describes the research techniques. The methodology, consisting of the specific tools that the research will utilize will be explained in this chapter with the explanation for the choice of the methodology being provided. The research will ask questions that will be answered through appropriate data, and this will then be analyzed to conclude.
Qualitative Research Technique (QRT)
Qualitative research technique, according to Terrell, is carried out through observation or unstructured questionnaires Performa (2012, p. 257). (Qualitative purists support a constructivist or interpretivist paradigm and “contend that multiple constructed realities abound, that time and context free generalisations are neither desirable nor possible…”). This research will utilize some of the qualitative methods including direct observation, interviews, and questionnaires. The qualitative technique of carrying out research is simple to apply and acquire information in a survey, and the data collected is regarded as adequate to draw appropriate conclusions. In most of the researches into supply chain management in the construction industry, the application of qualitative research techniques is universal with favorable results.
Quantitative Research Technique (QNRT)
The quantitative research technique is widely regarded as statistical analysis. According to Terrell, the Quantitative research technique entails the designing of a questionnaire, which is then sent to relevant Companies, or a direct interview conducted in these companies(2012, p. 257). (Quantitative research (i.e., a positivist paradigm) has historically been the cornerstone of social science research. Purists call for researchers to “eliminate their biases, remain emotionally detached and uninvolved with the objects of study and test or empirically justify their stated hypotheses”). The technique uses statistical figures to support the inferences that are discussed in the literature review. He explains that quantitative research technique is more powerful to get practical and significant value for the objects and also it gives a clear picture to observe, access the phenomenon of association between the various relationship facts and their association with theories and conclusion of research conducted in the literature (2012, p. 258).
Selected Method for Data Collection
The selected method of data collection was based on the time available for the research, the number of companies and organizations that were to be significant enough for a conclusion, and the resources at disposal. The study uses a representative sample of 46 respondents selected from a population of the management supply chain sector through a random sampling method to reduce biases. A combination of interviews and questionnaires were used in the research as the methods of choice due to the limitation of time and resources. The questions raised are interview questions
Questionnaire Design
Mixed methods are suitable in any academic study. Terrell describes them as “Studies that are products of the pragmatist paradigm and that combine the qualitative and quantitative approaches within different phases of the research process” (2012, p. 256). It is with this consideration that the questionnaire to be used in the survey was designed, with the main intention being to make it as simple and comprehensive as possible. It is recognized that a badly designed survey contains poor or meaningless questions in the survey, which becomes raw information and the survey may be affected by the meaningless questions. The questions were therefore selected after a pre-trial session on some of the participants of the survey.
Data collection and Analysis
Introduction
After the pilot study and testing of various data collection tools, the research went further to collect and analyze data. After data collection, the researcher coded all the data and entered it into the computer for analysis using the statistical package for the social sciences (SPSS). The data was then analyzed using both descriptive and statistical analysis procedures. The descriptive analysis procedures employed included frequencies and percentages. The results are reported in summary form using frequency tables and bar graphs.
Results and Discussions
The research realized that the sampled engineers, project managers, cladding managers, clients, and main managers had been working with the company for more than 10 years. Such a group was, therefore, better informed than new employees who did not know much about the construction company. The research sought to know the views of various stakeholders concerning the importance of finishing projects within time, cost, and up to the quality standards. The research narrowed down to a comparison of the results of three functions: the clients, cladding managers, and MEP. The results were analyzed as follows:
Analysis based on the Response by Cladding Project Managers, Main Contractor, and MEP Subcontractors
Table 1.0 Importance of finishing projects within time, cost, and up to the quality standards as responded by cladding project managers, main contractor, and MEP subcontractors.
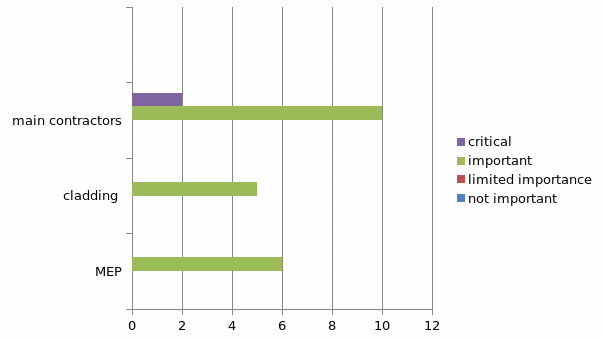
Analysis of the importance of finishing the project within time, cost, and up to the quality standards by comparing cladding project managers, main contractor, and MEP revealed various points. From table 1.0, it is clear that the cladding managers, main contractor, and MEP scored above 0 on important rating in the three functions. The indication is that all three categories regarded time management, reduction of cost, and improvement of quality standards as important to their work. There were variations in the degree of importance rating among the three. Inferring from graph 1.0, one can deduce that MEP had the highest importance rating at 6 out of 6, which was a 100% translation. The indication is that the representative MEPs that were interviewed affirmed that it was important to complete projects on time, deliver quality projects, and reduce the cost of projects. The cladding project managers also scored 5 out of 5, which also translated to 100%. The researcher deduced that from table 1.0 and graph 1.0 the project managers also had high regards for finishing projects on time, reduction of cost, and improving the quality of projects.
Having all the sampled members rate the factors of cost, time, and quality as important indicates that they all appreciate the role that the three factors play in the success of construction companies. Cladding managers are on the ground to deliver projects. They, therefore, understand how crucial time management is in reducing conflicts with the main managers and clients. Cladding managers also understand the importance of delivering a quality project in making up the image of the company. Besides, reducing the cost of projects ensures that the projects are put at reasonable prices for the clients. The entire sample main contractor also rated time, cost, and quality as important with a rating of 10. The main contractor’s perception as the main developer of the projects was an important indicator. The three factors, therefore, appeared important. According to Cao, Yin, and Kaku, (2010, p. 3429), the main contractor would want timely, quality, and cost effective projects. The graph indicates that the other rating factor of not important, limited importance, and critical scored 0 hence the percentage was also 0. One can therefore deduce that cost, time, and quality are important. The main contractor would want to make the most out of their finances. It is therefore important that the contractors deliver a less expensive project that is timely and of high quality.
Table 2.0 Importance of proper risk management by MEP, Cladding, and Main Contractors.
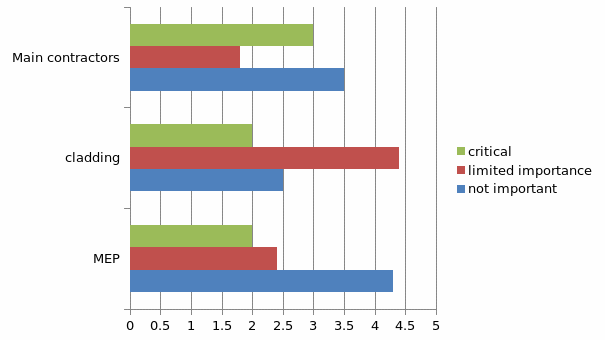
From the above table, it is also clear that out of the 5 cladding managers that were sampled when gathering information all of them rated risk management as important factors. This translated to 100%. The table also indicates that 8 main contractors out of the 12 sampled rated the issue of risk management as important. The remaining 4 rated risk management as critical. This finding translated to 66% scores rating it as critical under the four-point rating scale. Besides, 24% of the main contractors thought that time, cost, and quality was not only important to the construction industry but was critical. This finding indicates that the main contractors attach high value to proper risk management. The graph also indicates that the MEP valued proper risk assessment. Out of the total of six respondents, 6 of them rated risk management as important. This translated to 100%. In comparison, all three members of this group had high regard for risk management by the construction chain. In each player, there was an above average score on the rate of importance. 24% of the main contractors thought that risk management was critical. However, graph 2.0 indicates that none of the main contractors, the cladding officers, and the MEP rated the issue of risk management as not important or of limited importance.
Table 3.0 Importance of communication and coordination among SC members by MEP, cladding, and main contractors.
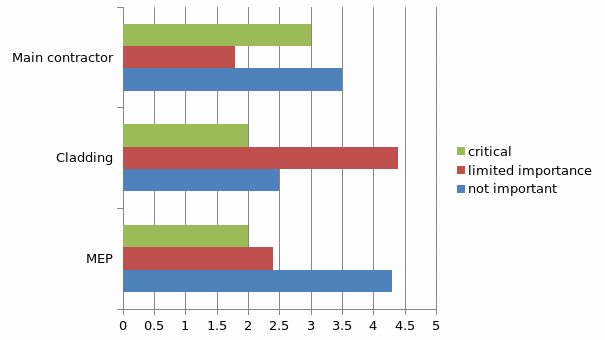
From graph 3.0 above, one will realize that 6 out of 6 MEP rated the need for communication and coordination of SC members as important. This translates to 100% on a four-point rating scale. In comparison with the main contractors, a difference is evident in the number of respondents that cited communication and coordination as important. Table 3.0 indicates that 8 out of 12 respondents under this category rated communication and coordination as important. This translates to 66% of the main contractors. The remaining 24% rated communication and coordination as critical. The percentage of those who rated communication and coordination as important is, therefore, lower on the side of main contractors in comparison with the MEP. However, the MEP scored zero in those who rated communication and coordination as critical to the supply chain. The number of cladding subcontractors that rated communication and coordination as important were 3. This translated to 60%. The remaining 40% rated coordination and communication as critical. This was also above the number of both the main contractors and the MEP that rated communication as critical. We can therefore deduce that coordination and communication were more regarded by the cladding subcontractors than the main contractors and the MEP.
Analysis Based on the Responses by clients, project facilitators, and engineers
Table 4.0 Importance of finishing project within time, cost and up to the quality standards comparison of clients, project facilitators, and engineers.
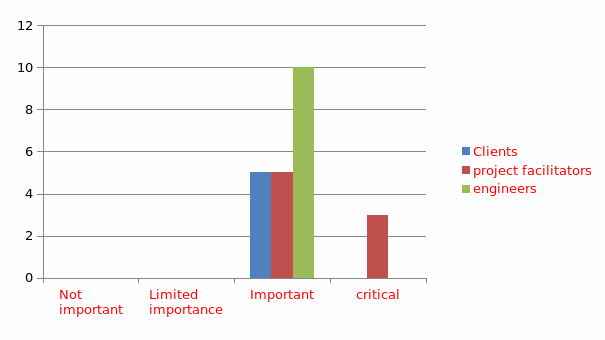
From graph 4.0, one can also deduce that the rating for importance is above average for the clients, project facilitators, and engineers. All the three members of this group of construction supply chain rated the importance of completion of projects on time from important to critical. It is also clear from graph 4.0 that a higher percentage of project facilitators would want to deliver projects on time and with minimal cost. Graph 4.0 indicates that all the project facilitators had a sense of the importance of time and quality in construction. Further analysis of questionnaires indicates that 100% of the project facilitators have worked for the construction supply chain for more than ten years. One can therefore deduce that they responded to the questionnaires under points of knowledge and experience. Table 4.0 indicates that 5 out of eight project facilitators rated the delivery of projects on time as important.
A reduced 3 out of 8 rated it as critical. The two ratings indicate that the project facilitators would want delivery of quality, timely, and cost-effective projects. In comparison, the graph also indicates that 10 engineers rated the delivery of timely, cost-effective, and quality projects as important. This translates to 100% of the engineers in the supply chain. However, the percentage of project facilitators that rated it as important and above was higher than that of the engineers. We can therefore deduce that the cause of delays in delivery of projects that leads to cost increment and lawsuits have little to do with the project facilitators. It can be argued that engineers would generally want delivery of quality and timely projects since they rated it as important. All ten engineers had worked on more than 20 projects since employment in the supply chain and had handled more than five projects within the past ten years. This indicates that the engineers were popular and handled many projects hence the importance of monitoring their opinion on time, quality, and cost. In comparison with the clients, the score for the project facilitators and the engineers was above average under the rating- important. The clients scored 5 out of 5, which translates to 100 percent, which is equivalent to the rating of the engineers who also scored 100%. All the other points in the rating scale scored 0 indicating that none of the clients would like their projects to be delivered late, under low quality, or very high cost. The lower levels of not important and limited important scored
Table 5.0Importance of breaking down barriers by clients, project facilitators, and engineers.
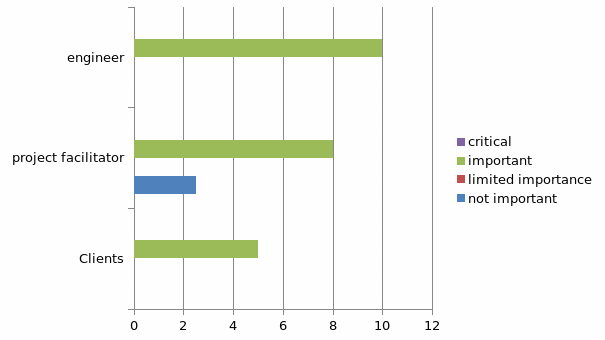
From graph 5.0, all categories of the supply chain under this group scored above average in rating. In all categories, the respondents scored 100%. The clients scored 5 out of 5. This means that all the responding clients cited breaking down of barriers of SC as important. This translated to a 100% rating of importance by the clients. Similarly, project facilitators scored 8 out of 8 under the importance scale. All of the responding project facilitators rated breaking down of barriers as important. This again translated to 100% on a four-point rating scale. The engineers also rated the breakdown of barriers as important with a 100% rating. This means that all the responding engineers’ respondents that it is important to break down barriers that hinder the effectiveness of the supply chain. The research can therefore argue that breaking down barriers in the supply chain is an important area of concentration in enabling the success of the construction industry.
Table 6.0 Importance of risk management by clients, project facilitators, and engineers.
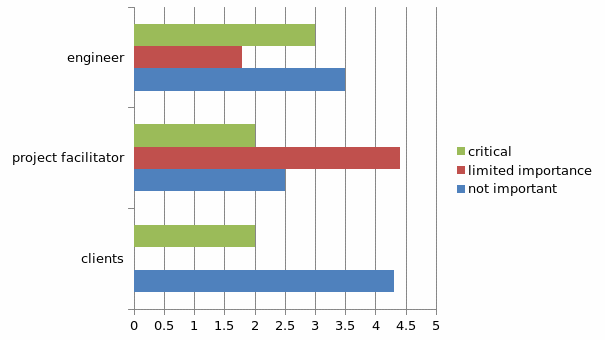
The above table and graph indicate a variation in the number of clients, project facilitators, and engineers that rated risk management as important, and critical. However, it is observable from graph 6.0 that 2 out of five clients rated risk management as important. This translated to 40% on a rating scale of four. Another 2 of the five respondents responded that it was critical to managing risks. One respondent did not know whether it was important or not to manage risk so he or she left a blank space on the particular question. Similarly, 10 engineers took part in the interview. All 10 engineers responded that it was important to manage risk in the construction supply chain. This translated to 100% of the total respondents in this category. Similarly, graph 6.0 and table 6.0 indicates that 8 project facilitators indicated that it was important to manage risks. This finding was 8 out of the total 8. Hence, it translated to 100% on a rating scale of four. The indication is that more engineers and project facilitators that rated risk management as important were more than the clients who did the same. The graph also indicates that only the clients had some of their members rating risk management as critical.
Analysis based on the responses by clients, engineers, project facilitators, main contractors, cladding subcontractors, and MEP
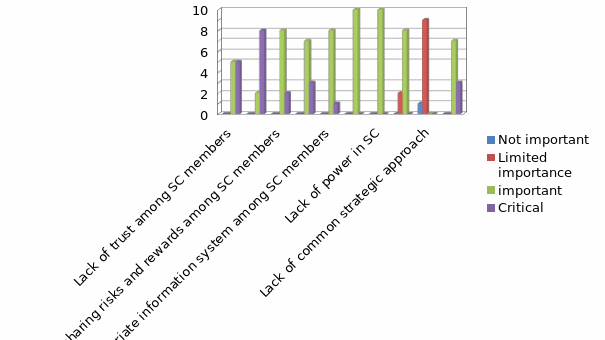
There are various barriers to the effectiveness of supply chain management. Graph 7.0 indicates that barriers such as lack of trust among members scored 5 (50%) and 5 (50%) under important and critical respectively. Halman and Voordijk (2012, p. 1444) affirm that the lack of trust among members is one of the major barriers to the performance of the supply chain (SC). Lack of cooperation as a barrier scored 2 as important and 8 as critical. The inference is that it is critical to promote the cooperation of members of SC to achieve success. Lacks of commitment also act as a barrier to effective SC performance; it scored 7 and 3 under important and critical scales. Some members of the SC were disinterested with the SC activities standing at 10 scores as lack of interest among members. Gosling, Naim, and Towill (2012, p. 102) affirm that having a member that is not interested in what the group is doing is detrimental. Moreover, when members lack a common strategic approach, it becomes a barrier to the success of the group.
Most of the players in the supply chain would cite reasons like the scope of work not being clear, no proper communication and coordination, and no proper cooperation amongst others. It is out of this that most respondents rated the main contractors as incompetent. The response from most of the clients was that these incompetent contractors were awarded the contracts out of low charges and relationships with clients. Graph 7.0 indicates that the lack of a common strategic approach scored 1 under not important, and 9 under limited important. All the other rating points scored 0. Lack of risk assessment scored 7 as important and 3 as critical. It is therefore important to assess risk since it can act as a major barrier to SC success. The question of rating various supply chain management also revealed that several aspects of communication are important for the success of the supply chain. Xu (2011, p. 183) affirms that proper communication is integral in supply chain management.
Objectives of Supply chain management
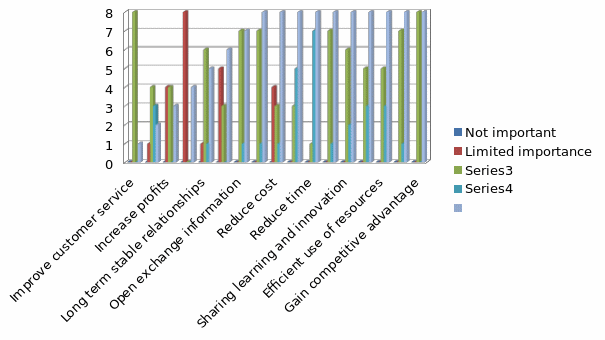
Graph 8.0 below indicates that various objectives of Supply chain management were rated differently by different functions of the construction company. It is critical to evaluate the objectives that various players had. Since all of them had worked on projects worth more than $10. Others were working on projects worth over $200. The research also indicated that very few projects were completed on time in the past ten years. It could go to a minimum of two or even zero under some players like the project facilitators. The number of projects that had cost and time overrun was also many. For example under the project facilitators out of an average of 5 projects, 5 of them had time and cost overruns. For example, the graph indicates the ratings by project managers.
From the above graph, one can deduce that the project managers rated improvement of customer service as important with 8 out of 8 translating to 100%. This finding indicates the commitment of project managers to improve customer service. However, the managers had divided feelings about bureaucracy reduction. One rated it as of limited importance, 4 rated it important, and 3 rated it as critical. Bureaucracy hampers interaction, openness, and trust among members of a team. Protocols also reduce the speed of communication.
To them, there was little need of breaking the prevailing barriers and the projects would excel under the existing conditions. The graph also indicates that the project managers rated continuous improvement as important with 7 scores and as critical with one score. According to Tennant and Fernie (2013, p. 83), it is important to continually improve the quality and quantity of their service in the construction supply chain. This aspect was at a rate of 7 and 1 under important and critical respectively.
Problems during the survey
The survey was successful in gathering and analyzing data. However, it encountered various problems. It was difficult to approach senior members of the SC since protocol had to be observed. It involved booking a date with them to fit in their tight schedules for example the project managers, engineers, and main contractors. The other hurdle was the bureaucracy of the organization. The researcher had to seek authority from one office to the other to be allowed to research the company. This involved screening and vetting. In some instances, the managers filled the questionnaires in a hurry hence this could have resulted in the inconsistency of the data.
Findings of the Survey
The findings of the survey were that most of the SC members had worked with the company for more than ten years. All the interviewed members had done so. It was also worth noting that all the members sampled (100%) believed that it was important to deliver projects on time, and with good quality. Other findings included the ratings of various objectives of SC management and barriers to effective SC performance. Xu (2011, p. 183) affirms that it is important to put in place various communication mechanisms, improve the quality of projects, deliver projects on time, and reduce the cost of the projects. It was also clear that some members of the SC act as barriers since they are not committed to the projects. Proper coordination of members can break the barriers.
Conclusion and Recommendations
Introduction
The survey realized that it is important for supply chain managers to deliver projects in time, deliver quality projects, and reduce the cost of projects. It was also found that some members and groups of members from the supply chain might never like to break down barriers to ineffectiveness. A good number of others are completely disinterested in the undertakings of the group hence they keep on drawing the group back. The clients scored high rates on the need for quality, timely, and cost-effective project. Delivery of projects on time was paramount to the clients since they were the final consumers of the product from SC.
Conclusion and General Summary
The research concludes that supply chain management is a good business venture that is promising to employees. Every supply chain management should endeavor to honor various factors such as being timely, being cost-effective, and delivering quality services. Supply chain management is set to achieve various objectives. Such objectives may have both liking and dislike by the members. The research realized that there were some objectives of the construction supply chain that were rated as not important and of limited importance by the majority of the respondents for example allowing the contractor and the sub-contractors to be part of the early deliberations about the projects. The main contractors did not disclose information about the tendering process. It was also not possible for the other functions to be involved in the initial stages of tendering and contract signing to avoid delays. Uncertainty is a significant source of delays in construction supply chains, this being influenced by the performance at each of the levels.
Dissertation Aims and Objectives Overview
This dissertation aimed to investigate whether good management of the construction supply chain helps in avoiding variations in time and cost, which occasionally results in legal suits among various supply chain partners. The paper aims at enabling the construction supply chain to reduce risk, cost, and time taken in delivering projects. The rating of such barriers was analyzed. Halman and Voordijk (2012, p. 1444) affirm that through deep analysis of the data gathered a researcher can recommend the important activities that supply chain managers should integrate and those that can be outsourced depending on their ratings. The objectives of this research were realized through field research where data was gathered and analyzed. Also, the research offered recommendations for further research areas. The research was also able to analyze recommendations for changes by key players in the construction supply chain. For example, on the question on what the Engineer could do to change the status, over 50% of the respondents cited the release submittals on time, certifying of payments on time and avoiding asking for changes in scope and advising the client to provide a clear scope of work.
Hypothesis Authentication
This dissertation hypothesized that most construction supply chains face litigation due to poor management that waste time, keep on altering the cost of projects, and deliver low-quality projects. Authentication of the hypothesis was done through field research that involved gathering data and analyzing it. The research realized that the hypotheses were true by the evidence of the analyzed information. Data analysis realized that most of the supply chain partners rated the completion of projects in time as either important or critical. Also, most of the supply chain partners rated the delivery of the project according to the agreed cost of contracts as important and critical. Most of them rated the issue of cost as critical. According to Tennant and Fernie (2013, p. 83), partners would want their organizations to improve information sharing, to enhance coordination and communication between various supply chain partners, and to create compatible information systems.
Research Limitation
Although the research was highly effective and successful, various limitations also hampered its success. The major limitation of this study was finance. The financial cost involved money paid as fare, typesetting, and printing, purchasing of research materials, and stationery. Finances limited the scope of the research since the research involved meeting various supply chain managers who were not at the same point. Reaching the partners involved a lot of money especially as fare. The research also required finances for editing of the dummy and the final research report. The other limitation of this research was time. Time is an important investment. The research required time for various aspects. There was a need for enough time to prepare the questionnaire, the respondents, and even analyzing the results. It took a lot of time to move from one office to another, some of the functions would not be met within time. In some offices, high levels of bureaucracy led to time wastage. In some cases, the managers would prefer that the researcher visit their office when they were not very busy.
Recommendations for Future Research
The process of research is cyclic. After carrying out research on a certain hypothesis and analyzing the results more questions emerge from the major questions. Since the research was empirical and it had to narrow down to a particular area, the sub-questions were left out for future researches. Various emerging questions were also left out for future investigations. The following are therefore the recommended areas for further research. There is a need to research the relationship and the interdependency of various functions in a construction supply chain. Risk assessment and management is important in building trust and confidence in the investors and clients.
References
Albaloushi, H & Skitmore, M 2008, ‘Supply chain management in the UAE construction industry’, International Journal of Construction Management, vol. 8 no. 1, pp. 53-71. ISBN: 1562-3599.
Al-Hajj, A, & Hamani, K 2011, ‘Material Waste in the UAE Construction Industry: Main Causes and Minimisation Practices’, Architectural Engineering & Design Management, vol. 7 no. 4, pp. 221-235. Web.
Aloini, D, Dulmin, R, Mininno, V, & Ponticelli, S 2012, ‘Supply chain management: a review of implementation risks in the construction industry’, Business Process Management Journal, vol. 18 no. 5, pp. 735-761. Web.
Arif, M, Egbu, C, Alom, O, & Khalfan, M 2009, ‘Measuring knowledge retention: a case study of a construction consultancy in the UAE’, Engineering Construction & Architectural Management (09699988), vol. 16 no. 1, pp. 92-108. Web.
Bankvall, L, Bygballe, L, Dubois, A, & Jahre, M 2010, ‘Interdependence in supply chains and projects in construction’, Supply Chain Management, vol. 15 no. 5, pp. 385-393. Web.
Blos, M, Quaddus, M, Wee, H, & Watanabe, K 2009, ‘Supply chain risk management (SCRM): a case study on the automotive and electronic industries in Brazil’, Supply Chain Management, vol. 14 no. 4, pp. 247-252. Web.
Cao, D, Yin, Y, & Kaku, I 2010, ‘A criterion of production model selection for building material with delivery delay’, International Journal of Production Research, vol. 48 no. 12, pp. 3429-3443. Web.
Chan, A, Chan, & Ho, 2003, ‘Patnering in Construction: Cirtical Study of Problems for Implementation.’ Journal of Management Engineering, vol. 19 no. 3, pp. 126-135.
Cooper, & Ellram 1993, ‘Characteristics of SCM and the implications for purchasing and logistics strategy’, The International Journal of Logistics Management, vol. 4, no. 2, pp. 13-24.
Cheng, J, Law, K, Bjornsson, H, Jones, A, & Sriram, R 2010, ‘A service oriented framework for construction supply chain integration’, Automation In Construction, vol.
Dainty, F, Briscoe, H, & Millet, & Neale, H 2004, ‘Client‐ledstrategies for construction supply chain improvement’, Construction Management and Economics, vol. 22 no. 2, pp. 193-201. Web.
Decelle, A, Bob, I, Das, P, Case, K, Shahin, R, Anumba, J, & Bouchlaghem, M 2007, ‘A review of approaches to supply chain communications: from manufacturing to construction’, ITcon, vol. 12 no. 1, p. 74. Web.
Dubois, A, & Gadde L 2000, ‘Supply strategy and network selects; purchasing behavior in the construction industry’, European Journal of Purchasing & Supply Management, vol. 6, pp. 207-215. Web.
El-Sayegh, S 2008, ‘Risk assessment and allocation in the UAE construction industry’, International Journal Of Project Management, vol. 26 no. 4, pp. 431-438. Web.
Eriksson, P 2010, ‘Improving construction supply chain collaboration and performance: a lean construction pilot project, Supply Chain Management’, An International Journal, vol. 15, no. 5, pp. 394–403. Web.
Faridi, A & El-Sayegh, S 2006, ‘Significant factors causing delay in the UAE construction industry’, Construction Management & Economics, vol. 24 no. 11, pp. 1167-1176. Web.
Geoffrey, H et al. 2004, ‘Client‐led strategies for construction supply chain improvement’, Construction Management and Economics, vol. 22 no. 2, pp. 193-201. Web.
Gosling, J, Naim, M, & Towill, D 2012, ‘Identifying and Categorising the Sources of Uncertainty in Construction Supply Chains’, Journal of Construction Engineering &Management, vol. 139 no. 1, pp. 102-110. Web.
Grant, R 2010, Contemporary Strategy Analysis, John wiley & Sons Ltd, Publications, New York. Web.
Halman, J & Voordijk, J 2012, ‘Balanced Framework for Measuring Performance of Supply Chains in House Building’, Journal of Construction Engineering &Management, vol.138 no. 12, pp. 1444-1450. Web.
Hong-Minh, M, Barker, R, & Naim, M 1999, Construction supply chain trend analysis,26-28 July 1999, University of California, Berkeley, CA, USA. Web.
Jaffar, A, ElKhatib, H, Hesson, M, & Radaideh, M 2007, ‘A proposed strategic alignment of IS/IT with supply-chain management for UAE dates industry’, Business Process Management Journal, vol. 13 no. 2, pp. 247-262. Web.
Jalbani, A 2010, Supply chain management in UAE construction industry, A Dissertation submitted in partial fulfillment of the requirements for the degree of MSc in Construction Project, Heriot Watt University, UK
Khalfan, A, McDermott, P, & Swan, W 2007, ‘Insight from industry; Building trust in construction projects, Supply Chain Management’, An International Journal, vol.12 no. 6, pp. 385–391. Web.
Kotler, P & Keller, L 2009, Marketing Management, Pearson Education Limited, New Jersey. ISBN 10: 0132102927.
Laeequddin, M 2009, ‘Supply Chain Partners Selection Criterion in United Arab Emirates: A Study of Packaged Food Products Supply Chain’, Paradigm (Institute Of Management Technology), vol. 13 no. 1, pp. 20-27. ISSN 0971-8907, ZDB-ID 14208544.
Lau, J, Huang, G, & Mak, N 2004, ‘Impact of Information on Inventory Replacement in Contrary Supply Chains,’ International Journal of Production Research, vol. 42, pp. 900-950. Web.
Lo¨nngren, H, Rosenkranz, C, & Kolbe, H 2010, ‘Aggregated construction supply chains: success factors in implementation of strategic partnerships’, Supply Chain Management: An International Journal, vol.15. no. 5, pp. 404–411. Web.
Love, E, Irani, Z, & Edwards, D, 2004, ‘A seamless supply chain management model for construction’, Supply chain management, vol 1 no. 1, pp. 43-56. Web.
Lummus, R & Vokurka, J 1999, ‘Defining supply chain management: a historical perspective and practical guidelines’, Industrial Management & Data Systems, vol. 99, no. 1, pp. 11–17. Web.
Maturana, S, Alarcon, L, & Vrsalavic, M 2000, ‘Achieving collaboration in the construction supply chain’, A non-site subcontractor’ evaluation methodology, vol. 2 no. 4, pp. 1-15. Web.
McDermott, P, Khalfan, M, 2008, ‘Achieving supply chain integration within construction industry’, The Australian Journal of Construction Economies’ and Building, vol. 6 no. 2, pp. 42-53. Web.
Mitra, S & Tan, A 2012, ‘Lessons learned from large construction project in Saudi Arabia’, Benchmarking: An International Journal, vol. 19 no. 3, pp. 308-324. Web.
Mohammed, S 2003, ‘Web-based technology in support of construction supply chain networks’, Work study, vol. 52, no. 1, pp. 13-19. Web.
Northhouse, P 2010, Leadership, Theory and Practice, SAGE Publication Inc., London. ISBN-13: 978-1452203409.
Olsson, F 2000, Supply Chain Management in the Construction Industry- Opportunity or utopia?, Thesis for the degree Licentiate in Engineering Lund University, Department of Design Sciences, Logistics. Web.
Qi, Y, Boyer, K, & Zhao, X 2009, ‘Supply Chain Strategy, Product Characteristics, and Performance Impact: Evidence from Chinese Manufacturers’, Decision Sciences, vol. 40 no. 4, pp. 667-695.
Segerstedt, A, & Olofsson, T, 2010, ‘Supply chains in the construction industry, Supply Chain Management’, An International Journal, vol. 15, no. 5, pp. 347–353. Web.
Tennant, S & Fernie, S 2013, ‘organizational learning in construction supply chains’, Engineering Construction & Architectural Management, vol. 20 no. 1, pp. 83-98. Web.
Terrell, R 2012, ‘Mixed-Methods Research Methodologies’, Qualitative Report, vol. 17 no. 1, pp. 254-280. ISSN: 1052-0147.
Vidalakis, C, Tookey, J, & Sommerville, J 2011, ‘The logistics of construction supply chains: the builders’ merchant perspective’, Engineering Construction & Architectural Management (09699988), vol. 18 no. 1, pp. 66-81. Web.
Vrijhoef, R & Koskela, L 2000, ‘The four roles of supply chain management in construction’, European Journal of Purchasing & Supply Management, vol. 6 no. 2, pp. 169-178. Web.
Weber, F, Dalluege, C, Shamsi, T, & Menconi, F 2006, ‘Improving Bid Preparation in Supply Chains in the Construction Industry, Supply Chain Management’, An International Journal, vol.15. no. 5, pp. 404–411. Web.
Wong, A, & Fung, P 1999, ‘Total quality management in the construction industry in Hong Kong: A supply chain management perspective’, Total Quality Management, vol. 10 no. 2, pp. 199-208. Web.
Xu, L 2011, ‘Information architecture for supply chain quality management’, International Journal of Production Research, vol. 49 no. 1, pp. 183-198. Web.