Abstract
In answer to the quest for a sustainable and secure supply of combustible liquid hydrocarbon fuels and gases, the development and recovery of oil from oil shale provides a fundamental answer to the need for meeting current energy demands for use in industry and other areas demanding fuels oils. Oil shales typically resulted from organic matter that underwent thermal modifications altering the arrangement of hydrocarbon molecules leading to the formation of long chains of hydrocarbon molecules from which oil could be recovered.
A study of oil shale and its formation with the kerogens forming the main constituent chemical components, the basis of liquid hydrocarbon fuels and gases on demand, and the chemical structure of kerogens reinforce the rationale for investing in the recovery of oil from oil shale as a commercially viable venture. Typically, the organic matter that led to the formation of oil shale had its origin in the remains of algae and other organic matter chiefly carbon and hydrogen the fundamental elements in the formation of oil shale.
Different countries have different oil shale deposits with the largest deposit lying in the Green River formations of the USA. Geological examinations of oil shale deposits put Brazil as the next most largest with oil shale deposits, followed by Russia with the third most largest deposits, followed by Zaire, then Australia with an estimated 17 billion bbls, and Canada with an estimated amount of 16 bbls of oil shale. However, the estimates are not accurate as further developments, geological surveys, and estimation techniques keep evolving.
Several technologies including the in-situ technology for the recovery of oil shale from oil have been developed. In the recent past, many countries with specific companies have developed their technologies tailored to address technological, environmental, and water needs challenges and problems that come with the recovery of oil from oil shale as discussed in the paper. Typically, oil shale is a fine grained sedimentary rock dominated by significant amounts of kerogens which when subjected to a thermal destruction process yields significant amounts of combustible liquid hydrocarbon fuels, gases, and byproducts.
The kerogens are rich in chains of hydrocarbon molecules, the target source of combustible hydrocarbons and gases. A typical infrared spectrography (IR) examination of kerogens reveals the kerogens to be composed of significant amounts of phenolic compounds which are largely dominated by a significant percentage of flash pyrolysates. Recent pyrolytic analysis of the Estonian kerogens has further revealed the Estonian oil shale to be significantly microfossil-rich in composition.
Despite the environmental, land uses issues, government legislations, huge amounts of water needs, the oil shale economics, and technical challenges experienced with the recovery oil from oil shale, the recovery of oil from oil shale are picking momentum. That is due to continually evolving innovations in new technologies which are more efficient and less water and energy intensive. The research and development of oil shale are gaining in many countries and chance of oil shale as a competitive resource for oil is gaining ground.
Introduction
One of the most challenging issues in modern economies, in domestic life, and industry is the need for cheap, sustainable, and reliable supply of combustible hydrocarbon fuels. The compelling need for an economically feasible and reliable supply of energy is the underlying reason for the study of oil shale and oil shale recovery technologies, the formation and extraction of oil shale in various countries, and the economic and technical rationale of investing in the recovery of combustible liquid hydrocarbon fuels and gases from oil shale.
Typically, oil shale is a carbon dominated sedimentary rock with significant quantities of kerogens. Kerogens form the main source of combustible hydrocarbon fuels and gases when subjected to thermal distillation of the constituent hydrocarbon molecules. The chemical properties of kerogens from different oil shale deposits have no significant variations. Analytically, kerogens are composed of long chains of hydrocarbon molecules which when thermally modified provide the desired hydrocarbon fuels. Kerogens were formed due to the thermal micro-organism modifications of organic matter particularly due to river inflows and outflows with variations in temperature and chemical conditions.
Typical examples include the Green River oil shale formations, the Estonian formations among others. One such example includes the Estonian kukersite kerogens. The source of the Estonian kukersite kerogens has been identified to be the thick walled organic sheath formations. An infrared spectrography (IR) of the kerogens reveals the kerogens to be significantly composed of phenolic compounds with the larger percentage being flash pyrolysates.
Recent studies and pyrolytic analysis of the Estonian kerogens have further revealed the Estonian oil shale to be significantly microfossil-rich in composition. Different technologies have been used to recover oil from oil shale. However, due to the ever increasing demand for combustible fuels and liquid hydrocarbons, the technologies have experienced an exponential evolution, with each interested company designing and developing typically tailored technologies to meet their oil shale development needs.
Exemplified companies include Chattanooga Corp, ExxonMobil, Anadarko Petroleum Corporation, among others. However, different technologies have different water needs as estimates in the paper indicate, cause different environmental impacts, and come with various associate problems as discussed in the paper. In addition to that, Governments express differing political views for the development of oil shale. Nonetheless, due to the compelling need for sustainable and secure sources of fuel for use in various industries, different countries have sanctioned the research and development of oil from oil shale. Typical example includes the US.
The United States has so far sanctioned the development of oil shale, which, according to some authors, has the largest oil shale deposits of commercial value concentrated in the Green River Basin. Despite the technological difficulties that have been experienced in the recovery of oil from oil shale, environmental issues and challenges, large amounts of water needs, effects on land formations, infrastructure development with the long term economic and security benefits accompanied with new and proven development in new and efficient technologies, the need to continue an unabated research and development of oil shale should continue.
Oil shale and its formation
Oil Shale
The rationale of developing oil from oil shale is reinforced by conducting an analytical examination of oil shale; a carbon dominated sedimentary rock rich in kerogens. Kerogens are carbon dominated compounds which when subjected to thermal destruction distillation processes yield combustible liquid hydrocarbon fuels and gases. The formation of oil shale, its chemical properties, and a study of the kinetics of the thermal destruction of kerogens with special emphasis on the structure and origin of the Green River formations, Estonian kerogens, and the Yanchangzu oil shale formations as case studies will inform the study.
Oil shale is a sedimentary rock which is a misnomer carbonate-dominated kerogen that has not been subjected to the organic phases of high pressure and temperature changes and associated microbial activities necessary for the formation of crude oil. Oil shale is a fine grained sedimentary rock that is a derivative of depositional organic matter which has been thermally modified through the application of intense heat leading to the conversion of organic matter dominated with hydrogen rich kerogens. The existence of oil shale in fine grained sedimentary rocks is in the form of long chains of hydrocarbon molecules discussed later in the paper.
The microbial activities mentioned above and other chemical processes occur at low temperatures during which the formation process of heavy oils is achieved. That is usually after the parent organic raw material has already undergone intense thermal modifications altering the arrangement of the constituent carbon and hydrogen atoms. When the resulting kerogens are subjected to intensive thermal destruction and distillation processes, liquid hydrocarbon fuels are produced. An analytical examination of the chemical structure of oil shale reveals it to be richer in the content of hydrogen compared with other heavy oils.
A common characteristic of kerogens is that the organic compound in its various forms is more energy intensive when being converted into the liquid hydrocarbons and fuel gases compared with t the refinery process of crude oil. The additional energy requirements needed to process oil shale makes crude oil to be a more suitable substitute for fuel oil and gas than oil shale. However, crude oil as a major source of fuel oil and gas has been overridden in the recent past due to political, financial, and other economic factors coupled with advancements in new developments of more efficient and cost effective technologies for mining and converting oils shale into combustible hydrocarbons.
History has it that the extraction and use of shale oil as a source of oil is a development on record to have started in the early 17th century. Its extraction is documented to have first been patented in 1694 in England. Successive years of developments and extraction are scanty and scattered. In addition to that, successful mining of oil shale and extraction on a commercial scale had never been fully realized in successive years.
That was particularly due to limitations and inefficient recovery technologies and low oil prices from petroleum. It was during the oil crisis of the 1970s that renewed interest sparked the development and extraction combustible hydrocarbons from oil shale with renewed vigor. Close to the 1970 period, the interest in the mining of oil shale and extraction of hydrocarbons was short lived when crude oil prices subsequently plummeted drastically. However, following an exponential rise and demand for oil and characteristic political instabilities and wars in many petroleum producing countries, interest in the mining and extraction of oil shale was again renewed. A number of multinational companies were urged to reconsider the potential viability of extracting oil from oil shale deposits.
Formation
Oil shale is an organic-rich sedimentary rock derived from aquatic organisms leading to the formation of kerogens. Numerous deposits are found all over the world with different geological and chemical characteristics (Smith, 1983). However, the chemistry is closely similar with different oil shale deposits. Taking the Green River oil shale formations as the object of study, descriptive information about their formation informs the general knowledge about oil shale formations (Smith, 1983).
Green River Formation characteristics
The green River formations are composed of sedimentary rock deposits rich in organic matter which was a result of natural consequence of natural chemical activities coupled with the physical limitations of stratified organic materials. A stable profile of the organic stratification led to the continuous nature of the Authigenic formations. These depositions occurred for millions of years leading to the oil shale deposits with an average organic content of 25 percent by volume of the hosting oil shale rock. An evaluation of the carbon-to-hydrogen in the Green Valley oil shale deposits reveals it to be equivalent to concentrations in the petroleum spectrum. However, it is worth noting that other oil shale deposits comparatively have lower carbon-hydrogen content than the Green River valley formations.
Evidence from intertonguing of marly lacustrine strata within the Green Valley formations was influenced by the fluctuations of inflowing streams of water. During the inflows, large expansions of lakes with consistent disturbances were formed. During the formation stage, lakes could lose large amounts of water particularly in semi-desert environments. In addition to that, large land derived depositional materials consisting of sandstones and silt was left. Then, variations in climatic conditions caused regional contractions of lakes increasing the salinity and alkalinity of the water deposits (Smith, 1983).
Typically, the occurrences and changes of climate related conditions led to the formation of soluble carbonates gradually precipitating Ca+Mg+Fe carbonates. During the drier periods, nahcolite crystals, silicate minerals, dawsonite, and shortite formations occurred. However, the authigenic sulfate could not be formed during the above discussed process (Smith, 1983). A typical chemical oxidation-reduction process is generalized below.
2CH2O + SO4–2 → 2HCO3–1 + H2S.
The sulfate was the dominant contributor of anions during the oxidation reaction process though the anion was later consumed by a sulfate reducing bacteria as demonstrated in the above generalized expression. One active bacteria ((cyanobacteria) was the dormant precursor to the inorganic materials that led to the formation of oil shale in the Green Valley Basin.
Different oil shale formations with different characteristics occur in different parts of the world. One other example to learn from is the Yanchangzu stratification illustrated below (Yun-lai, Yingcheng, Long, Jun & Yu-hu, n.d).
The diagram below illustrates the stratification and characteristics of the Yanchangzu oil shale formations.
An explanation of the above tabulation may provide further insight into the generalized conceptualization of the characteristics of oil shale formations. An examination of the above table indicates the lower parts to be dominated by silt, oil shale layers embedded into the stratifications, and sandstones that are characteristically fine grained. The Ty3 deposits are dominated by a bed-massiveness that is grey green in color. On the other hand, the Ty1 and Ty2 sections both are below the lower part of the strata and are characterized by black grey, yellow green, brown, green, and yellow-green depositional organic matter. Oil shale deposits dominantly occur at the Ty2 section. Measurements taken of the middle layer constituting oil shale indicate the thickness to be averagely 28 cm.
Different formations carry different quantities of oil shale deposits. During the Green River Basin formation process, a lateral and vertical consistency was registered across the 65,000 km2 sedimentary rock. It was a time of warm temperate climate when the deposition of organic matter leading to oil shale formations occurred. Typical of the formations were the Lacustrine sediments.
The characteristic formations occurred in two huge lakes with Uinta Mountain uplift separating both formations with an eastward extension. Elsewhere in the paper are discussed further chemical compositions and characteristics of oil shale formations. Some of the properties of oil shale that form the basic reason for firms and governments to invest in the recovery of hydrocarbon liquid fuels and gases for commercial and other industrial uses are discussed below.
Properties of Oil shale
An examination of the chemical properties of oil shale vindicates the rationale of exploiting oil shale for the production of commercial quantities of oil and gas for the energy market. That reinforces the need to study the properties of oil shale to crystallize the physical and chemical properties specific to the raw material. These properties allow oil shale to be considered as a feasible option and as sources of hydrocarbons (Volkov, Gerasimov, Ter-Oganesian & Samuilov, 2010).
The molecular weight of oil shale obtained from the thermal cracking process is variably influenced by the applied temperatures in the oil shale retort process. The temperature variations affect the chemical structure of the resulting kerogen. To further provide detailed information about the chemical structure of kerogens, a detailed study of the structure of the Estonian kerogens was conducted as discussed below (Volkov, Gerasimov, Ter-Oganesian & Samuilov, 2010).
Structure and Origin of the Estonian Kerogen
It was in 1917, when conducting a microscopic study of oil shale, that the botanist Zalessky coined the term kukersite descriptive of the molecular structure of Estonian kerogens. These kerogens identifiably typical of the Estonian origin were identified to consist of an arrangement of molecules connected in a polymeric chain of carbon and hydrogen atoms (Gavrilova, Randla, Vallner, Strandberg, Vilu, 2005).
The sources of the Estonian kukersite kerogens have been identified to be the thick walled organic sheath formations. An infrared spectrography (IR) of the kerogens reveals the kerogens to be significantly composed of phenolic compounds with the larger percentage being flash pyrolysates. Recent studies and pyrolytic analysis of the Estonian kerogens have further revealed the Estonian oil shale to be significantly microfossil-rich in composition (Volkov, Gerasimov, Ter-Oganesian & Samuilov, 2010).
A typical reconstruction of the benzaldehyde of the G. prisca microfossils is illustrated below.
However, several researches into the organic fauna of the Estonian oil shale have shown a significant constitution of limestone and clay. Dolomite marl occurs in rare quantities and is thought to have been formed from marine fauna in sea water. These sources are thought have been augmented by calcification in sea water with an eventual accumulation in the littoral zone (Volkov, Gerasimov, Ter-Oganesian & Samuilov, 2010).
During the formation of the Estonian oil shale deposits, organic-walled plankton governed the entire process of the Ordovician phytoplankton activities. That led to the formation of a single sedimentation during the oxic period to late Middle Ordovician formations among other formations (Lille, 2003). The anoxic depositions were characterized by arylisoprenoids compositions of the organic matter. The dominant player in this case was the siliciclastic lithology. On the other hand, oceanic currents and variations in temperatures led to the phototrophic formation of organic matter during the anoxic period.
That was the genesis of the Estonian oil shale deposits. Concrete evidence lacks on the actual biological sources of the Estonian oil shale deposits. However speculation adds that the activities of green sulfur bacteria led to the elevation of hydrogen content. During the multilayered microbial formations, intensive cyanobacteria activities lead to intensive oxygenation of the environment replenishing the environment with oxygen (Volkov, Gerasimov, Ter-Oganesian & Samuilov, 2010).
In the study, a detailed observation of the 13C CP MAS NMR spectrum of the Estonian kerogen modeled on a two dimensional structure revealed the following structure (Lille, 2003).
On the other hand, the distribution of the constituent components of the Estonian kerogen is graphed below.
An observation of the above data reveals the aromatics of the kukersite kerogen to be identifiably defined by low atomicity (Volkov, Gerasimov, Ter-Oganesian & Samuilov, 2010).
A detailed examination of the characteristics of oil shale and a detailed examination of different oil shale deposits have produced different results for different samples. These are characteristic of varied geological formations. To gain an insight into the variations in physical and chemical properties of the oil shale, a study of an investigative report from the United States Department of the Interior into the properties could be helpful. In particular, it is based on the examination of the chemical structure of kerogen as the chief organic compound and oil as a shale raw material (Lille, 2003).
A critical evaluation of availed information on the formation of Estonian oil shale deposits reveals the deposits to have been the result of single extinct photosynthetic micro-organism activities. These formations seem to have stemmed from the chemical activities and decomposition of green algae and additional activities of cyanobacteria. In addition to that, the oil shale formations seem to be largely composed of a high concentration of aliphatic macromolecules dominated by alkyl chains. On the other hand, oxygen containing functional groups of heteroatomic structure are dominated by hydroxyl and alkoxy components which form a third of the entire group (Volkov, Gerasimov, Ter-Oganesian & Samuilov, 2010).
Studies have been conducted to reveal detailed information about different models of kerogens. Results reveal these kerogens to be three dimensional polymeric materials consisting of a chain of hydrocarbon atoms. These atoms typically consist of aromatic chains that are linked to hydroaromatic chains to heterocyclics by aliphatic chains.
The objective of the study was to investigate the distribution of nitrogen and sulfur in crude shale oil. Typically, it included an examination of vacuum fractions. Distillate analyzes equipments were set up. This assembly included a flask used to collect the distillate from crude oil and the quality of the resulting gas from the distillation process. In the laboratory method, 500 ml of oil shale was served to provide the sample to be examined. However, the analysis does not provide estimates for commercial yields from the tested samples.
The testing equipment notably varied from that used for testing petroleum due to the large number of compounds that occur in oil shale but sparingly or without trace in crude oil.
The setting consisted of drying equipment to remove water which is an assembly of distillation devices and equipments to determine the properties of the resulting oil and gas. Without detailing the set up of the equipment and how it was conducted, different results were obtained and reliable information was assumed to be reasonable as tabulated below (Volkov, Gerasimov, Ter-Oganesian & Samuilov, 2010).
Several pyrolytic, spectroscopic, and microscopic studies and observations of kerogens have revealed structural differences between different classes of kerogens and their constituent components. The infrared spectra for the classification variables include carboxyl/carbonyl with concentration levels equivalent to (1710 cm–1), aliphatic concentrations, and aromatics.
Typical classification examples of kerogens include the Ordovician oil shale whose formation resulted from a marine environment. Typically, the Kukersite shale resulted from an organic maturation of organic microorganisms referred to as Gloeocapsomorpha prisca. These biological components gave the resulting kerogens its organic structure. Typically, aromatic components specific to the phenol class identifiably are also prevalent in thermally decomposed shale particularly under fast pyrolysis. The constituent aromatics are highly oxygenated and correspond to the chain of 3-n-alkylphenols among others (Volkov, Gerasimov, Ter-Oganesian & Samuilov, 2010).
kukersite kerogen which is cyclically structured is linked to each other by a chain of linear alkyls which are up to 19 molecules long. However, when these molecules are subjected to the pyrolytic treatment, they thermally decompose into smaller molecular chains and fall under the group of aliphatic hydrocarbons. In general, these molecular classifications fall into the n-alkenes-1 and n-alkanes chains.
On the other hand, Alkylated phenolics result from the condensation of alicyclic rings that define the molecular structure of the kukersite kerogens. This model of kukersite kerogens shows a carbon concentration of over 65%. Spectrographically, a significant part of the oxygen molecules are constituted in the hydroxyl groups. The hydroxyl molecules form a chain with aromatic and hydroaromatic molecules which acts as links between the chains (Volkov, Gerasimov, Ter-Oganesian & Samuilov, 2010).
It is important to conduct an investigative study of the kinetics of kerogens when subjected to thermal destruction process when undergoing the conversion process. Typically examples of the distribution of sulphur from oil shale distillates and the distribution of nitrogen in the respective distillates are as tabulated below on the global reserves (Stevens, Dinneen & Ball, 1952).
Kinetics of Thermal Destruction of Kerogens
During the thermal decomposition of oil shale of the bitumen category to extract the constituent kerogens, the thermal process results in a mixture of hydrocarbons, coke, and smoking gas. The constituent components of each of the resulting products vary in their organic structure and the specific substances characterizing each of the constituent components. In particular, the kinetic properties are significantly influenced by each component’s organic constituents or compositions. In addition to that, when bitumen is pyrolyzed (a thermal process that proceeds at low temperatures) a significant amount is transformed into coke. However, to achieve a complete transformation of bitumen to its volatile components, the bitumen is flash pyrolyzed.
A number of descriptive kinetic models provide an insight into the construction of flash pyrolysis models. On the other hand, chemical changes that occur during thermal pyrolysis can be analyzed based on different methods. Typically, these analytical methods include the Friedman Procedure, the Arrhenius Method, the Maximum Rate Method, and the Integral and Differential Methods. A study of the thermal decomposition of a kerogen indicates that a number of chemical changes modeled after a number of chemical reactions occur. Typically, the use of model functional groups provides a detailed view of the pyrolysis of coal and other synthetic compounds (Volkov, Gerasimov, Ter-Oganesian & Samuilov, 2010).
Typically, when oil shale is practically subjected to thermal decomposition, the constituent ring clusters decompose and provide substitute groups when exposed to a fast heating mechanism. The abstraction process leads to the formation of chains of different hydrocarbons and sulphide (H2S) groups. Aromatic hydrocarbons, high-molecular aliphatic, and asphaltenes are some of the resulting organic compounds formed in the process.
The radicalized atoms and hydrogen atoms combine to form the combustible organic compound dominated by hydrogen and carbon molecules. The resulting hydrocarbons are stabilized by the hydrogen molecules donated by both Hydroaromatic and aliphatic compounds during the thermal decomposition process. As a first order chemical process, a model of the functional groups shows how constituent chemical components are released leading to the mathematical modeling represented by the relation shown below. This mathematical representation is typically a universal representation of the kinetic model (Volkov, Gerasimov, Ter-Oganesian & Samuilov, 2010).
…………………i
Analytically, Gi represents the yield of oil shale expressed as a function of oil shale in kg/kg. Thus the kinetic component of the product can be determined based on the following kinetic equations.
…………………………..ii
In the above equations, Yi represents the contents of the ith functional group whose rate constants are represented by the Ki in S-1. The initial conditions can be modeled in the mathematical relation:
During the thermal decomposition process, different constituent components are released into the gaseous phase (Volkov, Gerasimov, Ter-Oganesian & Samuilov, 2010). The lighter constituents which are specifically defined by individual rate constants are also produced. Under isothermal conditions, where the rate constants are independent of time, the expression, Gi = Gi(t) analytically leads to the expression:
Analytically, therefore, the macromolecular decomposition of oil shale expressed in relation to the functional groups of the yields Gi is mathematically related below.
It is important to note that the analysis was conducted under isothermal conditions within the parameters specific to an isothermal environment.
The above modeling was done in view of the flash pyrolysis parameters and typically applied on the Kukersite Oil Shale.
Findings from the above modeling provide detailed and varying behavioral characteristics of the composition of constituent components in oil shale under varying temperatures. The optimum oil shale yield can also be determined under these models with an application of appropriate temperatures values. Typically, kukersite oil shale was the main oil shale component used in the modeling process. In a typical environment, the composition by percentage of N = 0.4 wt, C = 67.6, S = 4.8, and H = 8.2 constitute the organic component under investigation.
During the pyrolysis of the oil shale, saturated and unsaturated hydrocarbons and other gaseous components are formed with very high calorific values of about 33 MJ/Nm3. The percentage composition of the resulting gas also varies with varying temperatures. An examination of the behavioral characteristic compositions of the resulting gas with varying temperature gradient shows a characteristic feature where the unsaturated hydrocarbons attain optimum content at 930 K at a 26.5 % volume.
To establish the rate constants, k2i, for the above processes, a small modification of the mathematical relation has to be done on the following equation:
That provides the following relation:
These modifications indicate that varying the processing time with varying process temperatures allows the relation k2i = k2i (T) to hold for established and specific values of Yi0. That leads to the conclusion that the thermal decomposition of shale oil and thermal destruction of kerogens leads to the formation of hydrogen molecules. These molecules are the combination of hydrogen atoms donated from the aromatic reactions of the hydroaromatic structures. Each -CH2 chain yields a single hydrogen atom. Different gaseous compounds such as methane are formed in the process during the abstraction process of the methyl (–CH3) group.
The elemental composition of the Yi0 functional groups is determined based on the percentage of carbon dioxide and oxygen specific to the structural formation of the kerogen under investigation. A detailed examination of the Yi0 gaseous components of the kukersite kerogen is typical of the following compositions, CO = 0.0463, H2 = 0.0024, and CH4 = 0.0161.
If Arrhenius coordinates are used with a rate constant equivalent to k2i a minimum scatter plots on the graph is observed as illustrated on the graph below.
The scattering is minimal when experimenting at fixed temperature with a rate constant equivalent to k2 = 1.7×1010 exp (–20480/T) s–1 (Volkov, Gerasimov, Ter-Oganesian & Samuilov, 2010).
Conclusively, therefore, modifying the processing conditions and variables such as the temperature varies the chemical compositions and characteristics of the produced oil shale. Typically, it has been established that appreciating the thermal energy of the processing environment varies the yields oils shale correspondingly. It is important to note that temperature modifications vary the concentration of the maximum yields that happen at 830 K for phenols. However, it is also worth noting that the percentage composition of oil shale reaches a level where the content level of aromatics decreases with increasing heavy constituents.
When the abstraction of aromatic fragments occurs, phenols that belong to the hydroxyl group are formed. Typically hydroxyl groups are derivatives of the macromolecules that form the basic structural elements of kerogens. A typical experimentation provides the data tabulation below.
Typically, a comparative analysis of the results based on the kinetic model with supplied experimental data shows a rapid variation of the organic composition with temperature variations. As the temperature rises, the organic mass of coke, as illustrated in the graph below diminishes. That confirms the fact that flash pyrolysis provides the best condition for converting the organic components of oil shale into gaseous and volatile products.
One of the chemical properties of bitumen that distinguishes it from kerogen is its solubility characteristics in benzene a characteristic not inherent in kerogens.
Research findings have identified the properties of oil shale to be relatively influenced by the preparation methods used in the production process. One of the influencing factors is the thermal element used in the production process. Typically, the condensing temperature characterized by the retorting system and the separating temperatures is the influencing variables which determine by a significant extent the molecular weight of the resulting hydrocarbon. Significant differences in the physical and chemical properties of oils produced using different technologies are revealed in the study.
Potential of oil from shale
Countries with Oil Shale Formations
During the Cambrian, Ordovician, and Devonian periods, a number of geothermal processes occurred leading to the formation of oil shale in different quantities and qualities (Dyni, 2006).
Arguably, oil shale deposits exist in many parts of the world. Estimated deposits vary in quantities with the largest quantity existing in the Western part of the United States within the region covered by the Green River. It is estimated that the world to be having close to 409 billion tons in-situ of shale oil distributed over 33 countries of the world. However, it should be added that these are conservative estimates and further research needs to be conducted to provide further information on unexplored and undocumented quantities.
The economic rationale of exploiting oil shale is based on the depth from the surface the deposits from the earth’s surface. Typically, the depth allows for the use of the open or in-situ technique. The exploitation of these deposits is further reinforced by the economic potential of the by products that are obtained during the thermal processing of shale oil to obtain the appropriate hydrocarbon. These are byproducts that add economic value to the extraction of oil shale.
The byproducts include nahcolite (NaHCO3), copper, aluminum, and a range of other chemicals. Different sources of oil shale yield different oil shales with different chemical characteristics with gross heating values differing significantly. The heating value of oil shale is estimated to lie between 4000 kcal/kg and 2200 Kcal/Kg on a dry-weight basis. Different countries have different quantities of oil shale formations and distributions as discussed below.
Percentage of Oil Shale Formations
Regional variations in the goegraphicstratification of oil shale across the globe significantly vary in magnitude, distributions and yield values as illustrated in Fig 1 below (Boak, 2007). However, different authors provide different figures for different countries and regions.
Despite oil shale being prevalent in many parts of the world, yet little exploratory progress has been done to identify and quantify the reserves. Many attempts to provide global estimates of oil shale deposits have largely been speculative.
The difficulty nature of estimating global quantities has further been reinforced by the use of a wide variety of analytical units. However, recent times have experienced new developments in estimating the quantities by a number of countries including USA, Canada, Israel, and Australia as some of the outstanding examples. Typically, current techniques used for estimating available oil shale quantities rely on the use of imperial gallons and short or metric tons of shale oil, among other techniques. Different countries have varied estimate yields of shale oil with different qualities and quantities of shale oil. These countries come with different oil shale deposits that are discussed below (Kleinberg, 2007).
Countries with shale formations & the areas
The USA
A typical example that illustrates the formation of oil shale deposits is in the Western part of USA, the Green River as illustrated in fig. 1 below.
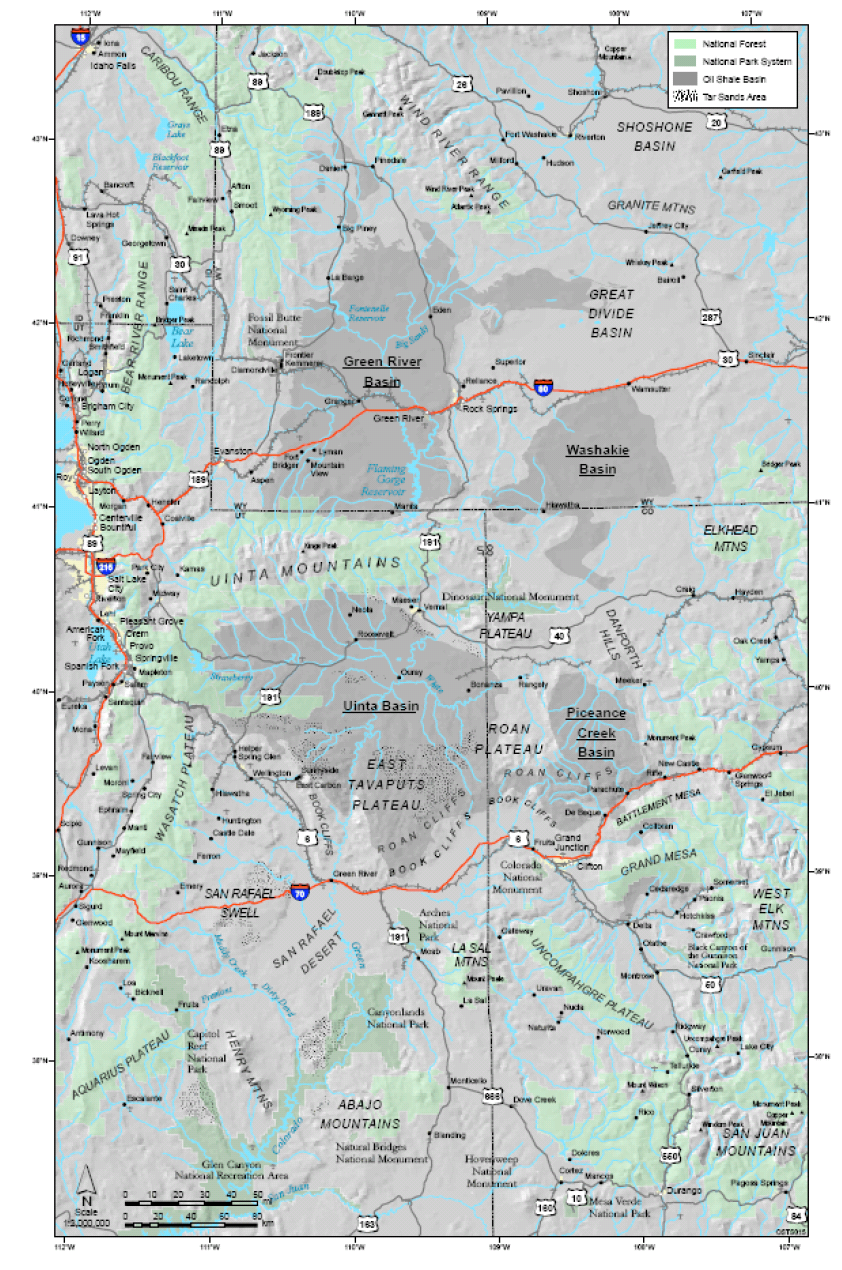
The lacustrine deposits are among the most prospective deposits with quantities of commercial value.
Historical development in the USA
During the 1900, oil shale deposits had been identified to be prevalent along the Green River Basin, though its commercial value could not be estimated at the time. Other sources of oil shale had been evaluated at this time and their commercial value was thoroughly investigated to evaluate the potential for commercial exploitation. It was in 1967 that the US government renewed its interest to investigate the commercialization of these deposits by leasing two tracts to oil companies for further exploration and evaluation process (Kleinberg, 2007).
A number of facilities with different mining techniques were constructed at the time by prospecting oil companies. These mining facilities included the construction of vertical shafts and entry pillars as access points. However, the Government was disappointed when no oil was produced at this time. However, other experimental sites were initiated by the U.S bureau of Mines to study and evaluate the prospects for oil shale between 1977 and 1978. Again, further disappointments were experienced as a large sum of money had been spent in the sinking of shafts and purchase of equipments without experiencing any positive results. The site had the closed eventually in 1980.
In the Green River region, sedimentary deposits occurred along the great Green River Basin when the Green River was being formed during the Eocene age. These deposits extend to the Piceance and the Uinta Basins within the greater Green River Basin. The rationale for conducting the survey and geological mapping and mining of the oil shale was due to the high quality and thickness of the deposits of oil shale in the region. Typically, the deposits in the Colorado and Utah regions are projected to yield 25 gallons of shale oil for every tone of sedimentary rock. Each rock is 25 or more inches thick (Kleinberg, 2007).
A number of challenges have to be overcome if, at all, geological prospects of mining oil shale within this region are to be realized on a commercial scale. Different mining approaches will have to be used specific to different geological formations of oil shale. Studies indicate that the oil shale formation along the Colorado region of the USA has an overburden thickness of 500 ft, making the mining commercially viable.
However, this region is severely limited by the narrow strip of land, along which the organic rocks lie, making it the mining process a technically and commercially restricted process. On the other hand, the concentration line of oil shale makes it difficult for prospecting companies to assemble the required logical units making the surface mining of oil shale in this region rather difficult (Andrews, 2006).
A detailed mapping of the geological setting of the Piceance Basin region indicates higher concentrations of oil shale in the North and isolated deposits in the south.
Typically the development process in the USA had its genesis in the exponential rise in oil prices in the world market. That prompted the US federal government to consider the option of mining the oil shale deposits largely occupying in federal lands. It was then that the oil shale field in California and Wyoming were seriously considered and separated as candidate fields for the raw shale oil.
A Synthetic Liquid Fuels Act of 1944 paved the way for the development of demonstration plants to evaluate the economic potential of investing into the mining and processing of oil shale. It was the US department of defense that developed earnest interest in oil shale as an alternative source of energy that accelerated the development of heavy oil s from oil shale for commercial purposes. It was when the Petroleum and Oil Shale Reserves Office (NPSRO) and the department of defense of the US started evaluating the suitability of exploiting oil shale to satisfy the demands of oil for military use.
Different companies were contracted at the time to carry out oil shale explorations and produce allowable distillate quantities. One such company was Tosco. Another company which showed vested interest was Development Engineering Inc. occupied the Naval Oil Shale Reserve 3 region and extensively conducted surveys through a company it had formed at the time named Paraho Development Corporation. These companies were formed in 1972 and 1973 respectively.
The study by Paraho Development Corporation involved setting up two pilot projects for evaluative research. Successful attempts by Paraho Development Corporation led to the production of an initial 100,000 of oil shale distillates that were later processed into various categories of jet fuels. Extensive tests on the jet fuels were conducted and the resulting data was collected and documented for further analysis. The results were not immediately published (Andrews, 2006).
Later years saw the air force get deeply involved under a project known as Project Rivet Shale. The Ashland Research and Development Company were among the companies awarded the contract to produce jet fuel from oil shale. Other companies awarded the contract included UOP, Inc. and Suntech, Inc. That was in 1982. Over 10,000 gallons of jet fuel was produced by these companies and tested by the military at the same time. Following further tests, the air force resolved to adapt the JP-8 program instead of the JP-4 program as it demonstrated it to be of commercial and technical value (Andrews, 2006).
It was after these developments that the department of energy (DOE) initiated large scale programs for the recovery of oil from oil shale. Two program initiated by the DOE included the Piceance Basin as discussed elsewhere and the Colorado (NOSR tracts C-a and C-b).
It was later when the P.L. 96-294, Title I, Part B of the energy security act was established solely to provide financial assistance to project that was successful in producing synthetic fuels particularly from oil shale. A number of proposals had been put forward for the procurement of oil shale contract projects between 1981 and 1984 under the Synthetic Fuels Corporation of the United States (Andrews, 2006).
It was in 2005 that congress embarked on a serious consideration of appropriate oil shale exploitation technologies which were considered to be environmentally friendly. A number of discussions cover a number of issues discussed elsewhere in this paper that include political considerations, legislative, and other legal obligations. The next country with oil shale deposits considered in the research is China.
China
In China, the formation of oil shale deposits occurs in the Ordos basin in deposits that are of commercially viable quantities. In addition to these oil shale deposits, uranium, coal, and ground water are value added deposits that reinforce the rationale of looking into the prospects of exploiting these deposits on a commercial scale. Many researchers have established the fact that Ordos basin is a giant treasure for the exploitation of oil shale.
A study of the distribution of oil shale within the Ordos basin reveals that up to 34 percent of the nationwide deposits are concentrated in this region. The oil shale deposits within this basin occur in different geological age formations. These geologic formations distributions in age have been identified to fall into the Permain, middle and late Triassic age, and the middle Jurassic periods.
A survey of these deposits indicates that the most economically and technically viable oil shale recovery approach is the open cast method. However, deposits found deeper into the ground are best suited for underground mining methods.
Distribution characteristics of Oil shale
An analysis of the formation of the oil shale deposits within the Ordos basin indicates the basin to be structurally layered in relation to the depth. These layers vary in depth from deep to shallow formations. Prevalently, these formations are distributed along the Shanxizu, Yanchangzu, Andingzu, and the Wayaobaozu whose formations are distributed according to the age when the formations occurred.
Each of these formations is characteristically distributed in different regions according to the period when they occurred. The Shanxizu formation occupies the region specifically within the Shanxi and Ningxia provinces where oil shale and coal have been identified to be co-existing. A close examination of the oil shale layers within these areas indicates variations in depth and thickness characteristically unique to each layer.
Oil shale deposits within the Shanxizu province are the richest in the level of hydrocarbon contents compared with other deposits in other provinces. Estimates indicate variations in the depth of oil shale deposits to be between 600 m in the eastern part to 2200 m in the western part. That has allowed for the speculation that the western part may be richer in gas deposits than the eastern part. However, these deposits are by far not economically and technically worth exploiting. Another region with evidently large oil shale deposits is the Yanchangzu province.
Formation in the Wayaobozu and Yanchangzu provinces are geologically symmetrical synclines with significant upwarp and cropping differences which are registered towards the eastern and western parts of the provinces. The Huachi and Huanxian counties register the most significant dips. However, the eastern and southern parts register a crossing that is characteristically arc shaped.
The Yananzu formation is another prospective source of oil shale. Distributions within this region vary in quantity under different geological settings ranging from the western to the eastern parts. The Western part has significant distributions of coal deposits interspersed with oil shale deposits. In the eastern part, oil shale deposits are due to geological formations due to lake deposits. On the other hand, the formations in the Andingzu province are buried deep and the exploitation relies on the depth of the formation from the surface. Studies conducted on the oil shale formations indicate variations in geological characteristics of the oil shale with characteristics that have been significant influenced the stratigraphic classification of the geology of oil shale distributions.
The Yanchangzu crop formations are dominated by green-grey and light red deposits.
These distributions have different substance concentrations. A close examination 0f the deposits indicates the concentrations vary from thick green to greasy luster with a red surface finish. Layers of green and flaky crop dominate different parts of the distribution. However, an uneven distribution conchoidally characterizes the geological setting of these formations. Conchoidal distributions are often represented by fractures, greasy luster, and brown streaks.
A glossy luster defines the bedding plane as one of the characteristic features of this distribution. However, variations in the sand content affect the coarseness of the bedding plane with varying characteristics due to variations in geological settings. Depositional matter is evident along the line of oil shale formations. These depositions vary from deep lacus to anaerobic deposition as the source of the oil shale formation is approached. A microscopic examination of the blastopelitic reveals a planar structure to be dominant in these distributions. A deeper examination reveals a combination of planar and directional structures.
Silt and Microaphanitic clay that belong to the family of clay appear with different structures varying from angular, sub-angular to rounded clay. These distributions appear to have undergone different levels of developments during the formation process of the oil shale. Further examinations reveal significant variations in the sizes of the grains to be up to 0.15 mm. In addition to that, the mineral content of these deposits varies significantly. The percentage content of clay, silt, and ferrum in oil shale within the region are 92%, 3%, and 5% respectively. On the other hand, the mineral composition in oil shale deposits is tabulated in the table below.
The above tabulations indicate SiO2 +Al2O3 to be the main chemical components constituted in oil shale. Significant traces of ash are also evident. However, further investigations into the quality of the oil shale deposits in these areas are necessary to vindicate the rationale of embarking on an economically feasible recovery.
The calorific value and oil yields have been the basic evaluating criteria for the quality of oil shale deposits in the Ordos region. An investigative evaluation of available data on the oil shale deposits in Ordos varies between 1.8% and 13.7%. The average value of this data is 7.70% reinforcing the quality factor for commercially viable exploitations. The hydrocarbon production content is estimated to be 400 Kg/t with a density of 2.59 (Average Relative Density) whose layers are approximately 10%.
Parametric aggregations of these findings prove that oil shale deposits in the Ordos are of a commercially acceptable quality. The genesis of oil within the region in Ordos provides a distinct profile for each of the areas. Typically, the areas in focus include the northern Tongchuan and the Tangshan regions.
Investigative reports identify the thickness of oil within the northern Tongchuan region to be 2 meters thick with variations in color between black and brown. Dominantly, the deposits are of the passive continental type which is sparingly distributed within this region. Oil yields from these deposits are of high quality, producing up to 20% hydrocarbons, though its prevalent occurrence is quite low. The thickness varies between 2 and 3 meters.
Another dominant type is black whose formation results from batho-lacustrine facies. A close examination of these deposits indicates a variation of up to several meters thick with a very low yields, of up to 10% hydrocarbon contents. During the formation stage, these deposits underwent a geological process involving water related organisms under the influence of cyclic climatic changes. Other formations occurred along the paludal facies forming upper and lower distributions with coal deposits of different oil shale qualities.
On the other hand, the Middle Jurassic has its dominant concentrations of oil shale found in the western part of the Ordos Basin. The areal geology shows faults distributions descriptive of the discordogenic fault that occurred and is prevalent in the western region of Ordos.
An assessment of the oil shale formation within the Ordos region in China falls into four descriptions specific to the age of the crop formations. Each of the formations is dominated by specific qualities and quantities with commercial value varying significantly from one formation to the other. These formations vary from middle to late Triassic whose oil formations occurred in the lacustrine environment. In addition to that, the thickness of oil formations varies between 13 and 16 meters with oil yields varying accordingly. Another country with commercially feasible deposits of oil shale is Israel.
Israel
A number of political, environmental, and economic reasons have prevailed upon Israel to join other nations in the research on the viability of mining oil shale as an alternative source of oil. Typically, the concentration of oil shale in the state of Israel has been estimated to be close to 20 billion tonnes.
A geological survey of the deposits of oil shale in Israel, illustrated in the map below, shows these deposits to be of commercial feasible. The organic distributions of oil shale crop formations occur at varying intervals with economic concentrations confined to Upper Cretaceous Mount Scopus. The primary sources of these formations were the activities of micro-organisms within the formations.
Australia
A geological survey of Australia reveals vast depositional formations of oil shale in Tasmania and New South Wales. Statistical estimates of the deposits are 270 million bbl of oil shale. These deposits have been identified to have high concentrations of the hydrocarbon molecules that produce the requisite organic compounds when subjected to thermal processing. It was far back in 1862 when the government of Austria had started mining oil shale in commercial quantities.
However, it was not until 1917 that the Government intervened by providing subsidies for the mining of oil shale. Nonetheless, in subsequent years, the mining of oil shale had been halted until sometime later when the mining again resumed. In the coming years until 1947, the mining of oil shale had accelerated to new levels with the aid of the government of Australia. The mining and processing rose in the subsequent years to 3% of the total gasoline composition demand of the Australian government. However, again a closure of the mining of oil shale was experienced due to the high costs associated with mining and processing for the highly needed hydrocarbon.
Recent estimates of oil shale deposits in the recent past are about 58 billion tons with recoverable amounts in the range of 3.1 billion tons as tabulated below. The formation of oil shale deposits in Australia range from the Tertiary to the Cambrian ages. New studies indicate that oil shale deposits occupy one third of the Australian country. These regions cover Victoria, and Tasmania, Queensland, New South Wales, among others as detailed in the map below.
Despite significant distributions of oil shale deposits evident in many parts of Australia, deposits with the potential for economic development have been identified to be concentrated Queensland. These deposits are largely of the Tertiary age dominated by the Condor and lacustrine Rundle deposits. More importantly, significant deposits in Queensland are of the early cretaceous age. On the other hand, the mining of oil shale deposits in the News South Wales ceased in 1980’s when the deposits were evaluated and identified to be of no commercial value.
Production of oil shale in the New South Wales was from the torbanite oil shale deposits. The mining of the New South Wales within this region occurred in the early 1860’s and 1960’s. The mining technique included the use of torbanite as a source of gas enrichments and source of gasoline. It was only 16 deposits out of 30 deposits that proved commercially viable. Other oil shale deposits in Australia included those in Tasmanite, Eastern Queensland, and Toolebuc (Schmidt, 2003).
In the Toolebuc region, oil shale formations are of the Early Cretaceous age. These deposits were identified to cover the Carpenteria and Eromanga basins in Australia. These deposits have been estimated to be 6.5 meters thick and largely of commercial value with an in-situ estimate of 1.7 billion barrels. Different deposits provide different favorability for the mining process (Schmidt, 2003).
It was during the oil crisis in 1973 that further explorations for oil shale were conducted in Australia. Of the several companies involved in the exploration process, none proceeded further with the exploration when the price of oil later dropped. However, deposits had been identified within the Yaamba and Mt. Coolon regions. A detailed analysis of these deposits revealed it to be composed largely of clay. Other investigations included the survey conducted by the Central Pacific Minerals (CPM) Company and other investigations by the Southern Pacific Petroleum (SPP) oil company (Schmidt, 2003).
Another location of special interest in the extraction of oil shale is Estonia as discussed below.
Estonian Oil Shale
An illustrious example of a strong dependence on shale oil is the Estonian economy. The dependence is particularly specific to the chemical and power plant industries. However, the economic rationale of overdependence on oil shale as a resource for the Estonian economy is based on an assessment on the environmental impact of the mining, production, and use of oil shale (Sabanov & Pastarus, 2006).
Data obtained from the mining and usage of oil shale from Estonia estimate up to 90 billion tons of oil shale to have been mined from the Estonian oil shale deposits up to date. It is estimated that the total area under oil shale deposits in Estonia is approximately 400 km2 with significant concentrations found in the North Eastern part of Estonia. Statistical estimates of the amount of oil shale usage in Estonia shows that 28% is used in the chemical industry while rest 72% is being used for the production of electricity. Significant concentrations are found in the north–eastern part of the country (Sabanov & Pastarus, 2006).
The main company with vested interest in the mining of oil shale in Estonia is Eesti Põlevkivi. Typically, the company has interests in the mining and recovery of appropriate hydrocarbons in Estonia. It further carries out all the activities associated with the distribution of oil from the two operational mines in Estonia. These include Narva and Aidu which with deposits recovered through the open cast method. Typically, there are two methods used to recover oil shale from the earth.
These include open cast methods which contribute up to only 47% of the recovered oil while 53% of the oil shale is recovered from underground. Statistical estimates put the annual recovery of the oil shale to be 10-14 tons from both above ground and underground recovery methods (Sabanov & Pastarus, 2006).
The operational efficiency of the recovery technologies in use allows opencast mining to be done to a depth of 5-20 m and allow above ground methods to be used to a depth of 20-70 m. However, mining technologies evolve dynamically. One such evolution is the use of blasting (Nikitin & Sabanov, 2005). Typically, this approach uses an emulsion technology to apply explosives on oil shale rock from which hydrocarbon oils are recovered. The powerful LHD machines are used to load and transport the blasted rocks into the appropriate site for the extraction of oil. The average productivity of the machines is estimated to lie between 1500-2300 m3 each day. Some transportation machineries such as those in the Viru mine produce minimum amounts of carbon dioxide compared with other mines (Sabanov & Pastarus, 2006).
As already mentioned, the goal of this investigation is to evaluate the impact of the oil shale mining on the environment particularly specific to the Estonian environment. The results can be modeled to explain the economic rationale of investing the recovery of oil from oil shale for chemical and industrial adoption for use throughout the world (Sabanov & Pastarus, 2006).
A research was conducted to typically evaluate the process by collecting data descriptive of the emission of gases during the excavation process and unit processes. Unit processes provided detailed data about underground mining and are specific to the technology and machinery used in the process. It is important to understand a typical description of unit processes to actualize the essence of the process.
A comparative study of old and new technologies specifically used in the mining of oil shale indicates a variation both in power consumption and emissions to the environment. The old technology used in Viru is dependent on electricity (Sabanov & Pastarus, 2006).
The Estonian mining and transportation process involves blasting the parent rocks using emulsion explosives that are charged by hand. That follows the loading process using powerful LHD machines linked with chain conveyers which are diesels powered. The conveyers typically move the rocks from the mine to the collection drift belt. In the transportation environment, the mine is moved to the enrichment point by cars for crushing and further processing. It is at the enrichment point that the oil shale rocks undergo destructive distillation through the thermal processing method. The end products are suitable for use in the chemical and power production industries. A tabulation of the processes and the primary unit consumption are tabulated below (Sabanov & Pastarus, 2006).
Further analysis of the emissions per ton is tabulated below.
In the impact assessment process, a number of impact categories were used as detailed below.
Impact categories
Specific to climate change, the impact categories identified included methane, nitrogen dioxide, and carbon dioxide. On the other hand, ammonia, sulphur dioxide, and nitrogen dioxide belonged to the acidification category. It is important to note that climate change is descriptive of the effects caused by green house gas emissions. On the other hand, acidification typically involves the implications of acids on the earth’s surface including acid fog and acid rain. A reaction between aluminum and other mineral substances with the acids create toxic substances for aquatic organisms and other living organisms (Sabanov & Pastarus, 2006). This process was also influenced by the characterization elements that influenced the intervention values specific to the climate change emissions of carbon dioxide as tabulated below.
By aggregating different acidifying factors, a critical load mass likely to cause harmful effects on the environment based on the quantity of emissions into the environment in excess of permissible values can also be categorized as tabulated below.
Comparatively, the Viru registered less environmental impact than the Estonian mines. However, the Viru mine registered higher concentrations of acid rain than the Estonian mines due to the large presence of SO2 in these deposits.
In conclusion, underground mining has less polluting effects on the environment than above ground mining. In addition to that, transporting oil shale as a raw material for further processing results into acidification due to the polluting effect of gaseous products than underground mining.
Why are Shale Formations in these Areas
In answer to the question, the formation of oil shale was due to the presence of organic matter whose source cannot be identified. At the formation stage, the constituent components of organic matter included algae, land and marine plants and animals, wood, lacustrine algae, and a number of other organic substances. Varied biological admixtures were as a result of environmental depositions which played a critical role in the formation of oil shales. It has been argued that bacterial activities played a significant role in the formation of oil shales, though it is difficult to scientifically verify the argument (Lille, 2003).
When analyzed chemically, the constituent components of the organic matter that form oil shale are largely insoluble organic solvents, though, to a lesser extent, some of the organic constituent components such as bitumen dissolve in organic solvents. Typically, oil shale consists of solid hydrocarbons that include grahamite, gilsonite, and kerite among others. These solid hydrocarbons have varied chemical and physical properties that make its mining an economically viable venture. The economic potential of oil shale deposits is variably connected to the closeness of the depth of the deposits from the surface (Lille, 2003).
Oil shales deposits close to the surface are geothermally immature. The geothermal maturity of oil shale depends on the level of geothermal alternations on organic matter. These modifications vary with depth. At lower depths, geothermal modifications on organic matter lead to the formation of oil and gas which sometimes form the source of crude oil. On the other hand, when organic matter is not deeply buried, geothermal modifications lead to the formation of sedimentary rocks with organic constituents that acts as the source of oil shale, determining the degree of maturity of the oil shale (Lille, 2003).
Oil shale is classified according to the mineral content and age of the kerogens, the petrographic properties of these minerals, the depositional environment, and the precursor organisms the derivative sources of the organic matter. The chemistry of organic compounds plays a critical role in the classification of the resulting organic compounds. Thus a useful grouping of the organic compounds plays a critical role in identifying the molecular and chemical structure of the resulting compounds. These include carbonate rich shale which is rich in calcite and dolomite. Typically, carbonate rich oil shale consists of lacustrine organic rich materials that are commercially difficult to process. The next category of oil shale is siliceous shale.
Siliceous shale is rich in siliceous minerals and less rich in organic minerals in comparison with carbonate shale, but is abundantly rich in opal, grey and other inorganic minerals. The extraction process for siliceous shale is less energy intensive with a higher economic potential when recovered with the ex-situ extraction method compared with other oil shale categories. In addition to that, siliceous shale is less wear and tear resistant to the wear and tear due to the variations in environmental weather. The last classification of oil shale based on mineral content is the cannel shale (Lille, 2003).
Different approaches have been used to classify oil shale. The next classification criterion is based on environmental depositions. These categories include lacustrine, terrestrial, and marine. Lacustrine’s constituent organic minerals include lipid-rich matter that originated from saline lakes and algae that was mostly prevalent in fresh water lakes. On the other hand, marine oil shale’s organic composition is a lipid-rich matter whose source is marine dinoflagellates and acritarchs. The terrestrial category constituted a high hydrogen content rich black coal typically defined by waxes and other materials from vascular plants and some traces of vitrinite with significant amounts of inertinite (Lille, 2003).
The organic matter in oil shale is a derivative of cola petrography that constitutes bitumen, telalginite, and lamalginite. Lamalginite is derived from unicellular algae mostly prevalent as laminae whose biological signature cannot be explicitly recognized. Telalginite and lamalginite have a common distinguishing color of yellow while bituminite which is weakly fluorescent with a less distinct biological structure. Bituminite is characteristically amorphous and of a fine-grained organic mineral matter. Under these categories of oil shale, there are six types of oil shale with significant variations in concentrations unique with each type. However, marinites and lamosites occur in greater concentrations than the rest six.
These compounds are distinctly differentiated by their physical and chemical characteristics. Cannel coal is differentiated by color variations between black and brown. Typically, the constituent component of cannel coal includes waxes, spores, and resins which are derived from terrestrial vascular plants. Oxygen deficient ponds form the basic constituent building materials for cannel coal.
On the other hand, Lamosite is characteristically pale or grayish-brown whose organic signature is defined by lamalginite. The major components that define lamalginite include lacustrine planktonic algae and minor components including bitumen and a variety of organic compounds (Gonza´lez-Vila, Ambles, Rı´o & Grasset, 2000). It is worth mentioning that lamosite prevalently occurs in the Green River oil shale deposits found in the western part of the USA.
On the other hand, the common organic derivatives of Marinite are bituminite and lamalginite. These organic compounds are derived from phytoplankton, largely of marine origin. Trace amounts of telalginite and bitumen are also constituent components of Marinite. Marinite occurs in significant amounts in epeiric seas where disturbance from sea currents are minimal. On a practical scale, these deposits usually occur in thin layers to attract the question about the economic feasibility of exploiting them as a raw material for the production of hydrocarbons. Typically, the Marinite Mississippi belt is 100 meters thick reinforcing the economic feasibility of exploiting these reserves for hydrocarbons (Gonza´lez-Vila, Ambles, Rı´o & Grasset, 2000).
Different geographic features distinctly provide the naming basis for different organic oil shale matter. For example, Torbanite has named after Torbane Hill in Scotland whose organic nomenclature is largely telalginite and algae. These deposits exist in minimal amounts but are of high quality. The following is an illustration of the classification of oil shale in the fig. below.
Countries Already Producing Oil Shale
Countries producing oil shale and relative amounts
Oil shale has been identified in many countries as a potential source of oil. The potential for oil and other benefits that come with the recovery of oil shale has reinforced an urgent need for these countries to develop oil shale despite. That is despite a number of commercial, technological, and environmental challenges. It is however, important to note that a strong need for a cheap, reliable, and sustainable source of oil overlaps other factors in stimulating the drive by the oil shale holding countries to embark on its development. Typically, high world oil prices are undesirable for economic any growth.
With these underlying reasons for development, statistical evidence provides information about a global survey of oil shale reserves for different countries. In addition to that, the report provides detailed information about countries that have embarked in the mining and production of oil from oil shale, respective quantities of oil productions, and the techniques specifically used by each country (Pastarus & Sabanov, 2005).
Despite a global occurrence of oil shale, published figures by the world survey of energy indicate that U.S.A has the largest deposits of oil shale with 626 billion barrels of recoverable oil shale. The US deposits are closely followed by Brazilian deposits that are estimated to be 300 billion barrels. The list is followed by Russia with 41 billion recoverable shale deposits, Zaire with 38 billion barrels, Australia with 17 billion barrels, Canada and Italy with 16 and 13 billion barrels with china estimated to hold up to 10 billion barrels of oil shale. The results are tabulated below.
It is worth noting that different authors, however, provide different figures for different countries. Elsewhere, it is argued that Canada has the largest amount of oil shale deposits in the world. However, a comparative analysis puts the US ahead of other countries in oil shale deposits.
Different countries have had different interests in the development of oil shale. A typical example is the US. In the US, large oil shale deposits have been identified to be prevalent in the regions of Wyoming, Colorado, and Utah. The depositional formations in the US particular the regions mentioned above are illustrated in the Fig. below.
Each of these countries has typically tailored and developed specific methods to develop oil shale typical of the goestratification of the deposits. However, the recovery techniques have dynamically experienced technological evolutions to address emerging challenges.
Different technological approaches have been used to develop oil shale for each of the above countries specific technologies, advantages and disadvantages are discussed hereunder.
US-Mine and Retort
The US has largely been exploiting oil shale through the room pillar surface mining methods until 1980 when new developments in the use of technology experienced full implementation. Typically, the above mentioned methods could allow the extraction of oil shale either from the surface or below the ground through thermal processes at high temperatures. However, the mine and retort method has already been discussed elsewhere (Sabanov & Pastarus, 2006).
Typical considerations for underground and above ground mining are the economies specific to the mining process in the US oil shale deposits. Further discussions on the economic rationale of developing oil shale are found elsewhere in the document.
Advantages
The mining approach has the advantage of being economically viable and has been widely implemented in the US. In addition to that, the recovery process has further advantages that are discussed elsewhere on the page.
Disadvantages
The main disadvantage with the mine and retort technique is the inability to be competitive against other fossil fuel recovery techniques. That is particularly in terms of cost effectiveness and the pollution to the environment of the techniques. One critical disadvantage with the room and pillar method is the inability of the technique to appropriately fit into the mining of thick oil shale deposits. On the other hand, the technique does not sufficiently address the left over wastes that pose environmental damages typically chemical and physical effects discussed elsewhere on the paper (Sabanov & Pastarus, 2006).
Waste deposal is another problem typical of the process. However, these approaches were used until 1980 when evolutions were experienced in technological innovations that addressed various problems to make the mining and recovery process technically, economically, and environmentally viable. In addition to the above mentioned technology, other technological innovations and development with respective development companies have evolved. However, typical of the document, oil shale technological innovations in the US have been discussed elsewhere with the advantages and disadvantages of the respective technologies.
The In-situ Process
On the other hand, another recovery and development technique is the in-situ conversion process. The conversion process is a thermally induced conversion process taking several months to achieve the oil shale conversion. Different companies use different conversion temperatures specific to each technology. A typical example is shell. Shell’s conversion process is ultimately achieved at a temperature of 350 ºC which allows the product to maintain the integrity of its chemical and physical properties. In addition to that, the oil shale temperature remains above 200 ºC and below 350 ºC to ensure the oil window is maintained to ensure no degradation of the resulting product occurs.
Advantages
The In-situ recovery process produces a hydrocarbon mixture that is superior in content compared with the mine and retort product. Typically, the constituent chemicals of the in-situ product include propane and butane with a 30% prevalence rate. In addition to that, other products include kerosene, diesel, naphtha, and other heavy industrial oils.
On the other hand, the economics of the in-situ process is strongly correlated to the efficiency of the thermal destruction process. Reaction temperatures for the recovery of oil shale are achieved by applying heat directly on the oil shale raw material. Different heating technologies have been developed by different companies to achieve an appropriate application of heat on the oil shale. One typical example is Shell. Shell uses electric heaters immersed in boreholes to supply the requisite heat for the recovery process. Shell has applied the electric hating method particularly in the Piceance Basin. Companies such as chevron have been keen in applying the technology in the recovery process.
Typical, the technical advantages of the process include the use of CO2 stream to supply the required heat to initiate the thermal process to the next rocks in the oil shale recovery locality.
Disadvantages
Key disadvantages of the in-situ recovery process stem from the environmental perspective. The heated zones within the oil shale are susceptible to the ingress of water. The ingress adversely affects the recovery process which demands that the water be removed before the recovery process continues. On the other hand, the recovery is susceptible to allowing heavy metals, both organic and inorganic chemicals to seep into underground aquifers causing further contamination on the underground water. The contaminations degrade the quality of water causing undesirable environmental impact. Companies which use the technology include Shell, chevron and other mentioned elsewhere in the document (Sabanov & Pastarus, 2006).
Brazil
A geological of the findings of oil shale deposits in Brazil are identifiably of the Permian period. These formations were of the ancestral group of carboniferous in the group of the amniotes. Typically, the recovery of oil shale from raw shale from in Brazil widely uses the Petro-Six technology. A typical recovery process is illustrated in the diagram below.
The Petrosix retort is illustrated below.
The above diagrams indicate a detailed recovery process for the recovery of oil shale in Brazil. Each of the steps is pointed above with each step of the recovery process typical of the technique shown. In addition to that, the technical components of the system are diagrammed above. Typically, the above representation presets the pyrolysis step of the oil shale typical of the Petrosix technology.
The production process is accompanied by a number of byproducts. Typically, the system allows for the production of fuel gas as a by-product, sulfur which is also a common by-product of other recovery processes. A typical application of the oil shale Petrosix recovery technology in Brazil is one at Irati oil shale field.
A critical evaluation of the Irati recovery process informs that different qualities of produced fuels depend on the retorting technology, different classes of oil shale, and energy demands for each retorting technology. Typically, the influencing parameters include the mechanical strength of the oil shale, kinetics of the oil shale as discussed elsewhere in the document, the chemical composition of the kerogens, and the thermal requirements of the oil shale as discussed elsewhere. The technology has its competitive side as an economically, environmentally, and technologically viable.
Advantages
The technical efficiency specific to the technology has been proven for 30 years. As one of the advantages, the technique has been identified with a technically unparalleled operational efficiency due to appropriate mechanical characteristics. The technology can be modified to address varying operational environments under different working conditions (Sabanov & Pastarus, 2006).
On the other hand, the technology is flexible for use on pilot test programs and to develop small scale oil shale deposits. In relation to the environmental impacts, the consequences have been analyzed and possible mitigations developed to address resulting environmental consequences. However, the technology suffers from the following inherent shortfalls.
Disadvantages
The disadvantages with the technology include waste disposal problems, water contamination by both the resulting organic and inorganic chemicals, and its complexity. In addition to that, large amounts of water are needed.
Russia
Oil shale deposits and production in Russia are dominantly concentrated in Estonia and the Baltic Sea regions. The oil shale recoverable quantities are estimated to cover a total of 50, 000 km2. The Estonian and Leningrad occurrences are of commercial value. However, the Estonian deposits are identifiably the richest in recoverable hydrocarbon content and oil shale resources in the world. The strategic significance of the Estonian deposits reinforced the rationale to conduct an extensive discussion about the deposits in the paper. A critical analysis of the quality of the deposits as a commercially viable venture indicates the deposits lie between 23% and 50% in quality (Sabanov & Pastarus, 2006).
The overburden of the Estonian formation is over 10 m with a bed thickness of over 1.5 meters, and a calorific value of 6.1 MJ K-1 of the recoverable raw shale. The energy rating for Estonian oil shale deposits is averagely 42.2 GJ m-2.
Both surface mining and underground mining are applied in the recovery of oil shale in Estonia and other recoverable deposits (Sabanov & Pastarus, 2006).
The technologies used in the Estonian mines in the recovery of oil shale typically include in-situ processes and the variants of in-situ mining techniques. In-situ mining and its variants have been discussed in detail elsewhere.
The main variant of in-situ recovery process is the true in-situ process that has been applied in the Estonian recovery process which has been discussed elsewhere.
However, the technology is susceptible to a number of advantages and disadvantages as discussed below.
Advantages
The method does not involve mining and the variables that come with the mining process. The variables include rubble, inorganic and organic byproducts, and environmental impact particularly on the quality of runoff water.
In addition to the above benefits, the technology allows for a slow thermal process creating microfractures resulting in enhanced liquid flow. The technology optimizes the recovery of oil and gas and allows for combustible gases to be produced further in depth compared with other technologies. The slow thermal process unique to the true in-situ technology is to enhance the quality of the resulting oil and gas due to the slow healing process (Sabanov & Pastarus, 2006).
Disadvantages
The technology does not allow controlled use of the flame front, allowing for the seepage of toxic byproducts into the ground eventually contaminating ground water.
Zaire
No evidence has been presented about ant explorations, mining, and processing of oil shale in Zaire.
Australia
Oil shale deposits in Australia are prevalent in the New South Wales and the Tasmanian regions. Due to poor forecasts for new crude oil fields and a decline in the production of crude oil, the Australian government as a matter of policy has focused on the exploration oil shale as a potential source of fuel oil and gas. The South Pacific Petroleum company plays a major role in the exploration, testing, evaluating, and the recovery of oil shale (Hettelingh, Posch & Slootweg, 2004).
The South Pacific Petroleum company has learnt from past mistakes made by various companies that had previously endeavored to develop the Australian oil shale resource to recover fuel oil and gas for commercial purposes. Quantities in the Australian are estimated to be 17 billion barrels with different authors giving conflicting figures. The South Pacific Petroleum company had initially started developing the candidate oil shale Stuart deposits (Crawford, 2007).
The South Pacific Petroleum company has identified the Stuart deposits to be suitable for open cast mining. Estimations of the oil shale quality designate the deposits to be rich in hydrocarbon contents and viable for commercial exploitation. In addition to that, the deposits are well served by communication infrastructure as illustrated below. Additional statistical estimates are also illustrated below.
The most appropriate technology identified by the company for the in-situ recovery process is the Alberta Taciuk Processor (ATP) technology. The technology comes with various advantages and disadvantages discussed below (Crawford, 2007). The recovery process typical of the ATP technology is illustrated below.
Advantages
The Australian oil shale is estimated to be containing a moisture content of 19 wt%. Low sulphur productions and cost of production characterize the technology (Schmidt, 2003).
The technical details, facility design, and implementation approach are simple. In addition to that, the technology is self-sufficient in energy, and conveniently processes dry oil shale with efficient heat transfer mechanisms is used. The transfer of solids between different points in the system does not involve moving parts that come with maintenance demands due to wear and tear of mechanical moving parts (Schmidt, 2003).
Disadvantages
The technology shows weaknesses in the modification of control loops and demands the injection of a combination of chemicals and water into the oil shale mass during the mining and extraction process (Schmidt, 2003).
The Top Five Countries Producing Oil Shale
No accurate results are available about the major producers of oil shale. However, the U.S.A, Estonia, China, Canada, and Brazil are major producers of oil from oil shale as discussed elsewhere in the paper.
Technologies
Oil shale retorting
Two basic technologies have of commercial interest have been used for processing oil shale including in situ processing (Holmes, Boss, Datcher & Heming, 1978).
In-situ processing is a conversion process that allows the transformation of oil shale into liquid hydrocarbons and gaseous fuels. A conceptual approach to the in-situ conversion process involves four steps. Typically, the first step involves the construction of a perimeter wall around the area to be retorted, then, subjecting the raw oil shale to electrical heating. The applied heat then appreciates the temperature of the raw shale to the decomposition temperature of the constituent kerogen. The resulting hydrocarbons are then transported to the surface before the disturbance is remediated. The conversion steps are discussed below.
The preliminary step consists of identifying the area to be retorted. Oil shale deposits are identified and available quantities evaluated before commencing the mining and conversion processes. Typically, oil shale deposits that are characterized by a thick formation and enclosed within permeable layers are chosen. The fig. below provides a conceptual view of the recovery process (Holmes, Boss, Datcher & Heming, 1978).
Different generic methods have been applied in practice to recover oil shale from its raw material for processing and conversion into hydrocarbons for use in the market. Typically, these methods fall into three categories with different approaches as discussed below.
True In Situ
Typically, the technique involves dewatering the deposits before converting the deposit into a permeable fluid in the vent of prevalence of water at the mining ground. The permeable fluid is then heated to an appropriate temperature for pyrolysis before the oil and gas are recovered through the wells that have been sunk. The fig below demonstrates the principles typical of the TIS mining approach (Holmes, Boss, Datcher & Heming, 1978).
The recovery process uses wells drilled into the oil shale deposit with injections directed towards the center of the well. The recovery is done by injecting the deposits through the production wells. The recovery process is further optimized by use of highly permeable fluids (Holmes, Boss, Datcher & Heming, 1978).
Modified In Situ (MIS)
One approach to increasing the permeability of the current oil shale deposits is a two stage approach. It involves dividing the deposit into two categories. One category is mined and the other category is blasted into the void created by the mined deposit. The two stage process is illustrated in the figure below (Holmes, Boss, Datcher & Heming, 1978).
Typically, the first step involves digging a tunnel that leads to the bottom of the oil shale deposit with an equivalent amount of shale removed to pave way for a retort. Subsequent drilling of holes through the roof of the newly created room that is equivalent to the height of the proposed retort is done. Each hole is filled with explosives that are later detonated in the second step. These explosions create a chimney shaped full of oil shale granules. The tunnel constructed to provide access to this point is sealed and an injection hole linking the surface to the broken oil shale granules is drilled. Injecting the rubble with burning oil fuel and gas ignites it.
Thus heat resulting from the burning of the upper layer is transferred downwards by the stream of gases. That gradually causes the lower layers to be pyrolyzed causing the resulting oil vapors to pool at the bottom of the retort. Subsequently, the resulting substance is then pumped from the bottom to the surface from this point. Typically, the burning zone advances gradually downwards until it encounters the end of the retort (Holmes, Boss, Datcher & Heming, 1978). At this point, the circulating air stops halting the advancement of the burning zone.
Typical examples where MIS has been used to mine oil shale deposits abound. One such is the Occidental Petroleum (OXY)’s subsidiary, Occidental Oil Shale, Inc. in USA. Five retorts had been developed one after another with different capacities. In all these mining ventures, estimated 40%-60% oil was recovered. Successive retorts were however constructed with mixed result (Holmes, Boss, Datcher & Heming, 1978).
In practice, the MIS approach proved inappropriate for mining oil shale deposits embedded in large oil strata. One approach in attacking this problem was to use solution mining. Solution mining entails the use fluids that are injected to remove soluble compounds stratified within the shale oil crop layers. Then, the resulting honeycomb structure is packed with explosives and detonated and the resulting slurry is used to recover the required oil and gas for the market. Different areas with different geological settings demand the use of specific recovery techniques. A typical example is the use of mechanical underreaming for wall mining purposes.
However, the most prevalently used MIS mining technique in the recent past is the vertical burn patterns. In practice, this technique had been applied by the Fenix and Scisson firms for mining oil shale from the underground. Other techniques developed in the process included horizontal mining. This technique was appropriately identified for use with other techniques that could allow the removal from the ground the huge quantities of strata on the surface before reaching the actual mine (Holmes, Boss, Datcher & Heming, 1978).
Other MIS technologies have been developed with time. One such is the multi-mineral technique (Holmes, Boss, Datcher & Heming, 1978). Typically, this technique is similar to the RISE technique that occurs at different levels of the rise as illustrated below.
The multi-mineral technique involves crushing, screening, and continuously moving the resulting compound to the top. An examination of the mineral contents of the resulting rubble includes large quantities of nahcolite and dawsonite. Typically, temperature control is the key determining factor. The above MIS technique is prepared through a number of procedures as illustrated below.
The preparation stages of the MIS retort technology is illustrated in the above diagram. Typically, the above retorting technique has a great potential of recovering the resulting minerals and fuel. However, this technique has not been used widely to permit a thorough evaluation.
Above Ground Retorting (AGR)
Above ground retorting technologies have significant variations in technical details and operational functionalities, leading to the classification of the technology into four classes. The first class involves transferring heat by conductions through the walls of the retort. The second class involves transferring heat by flowing gases which is usually as a result of burning within the retort chamber. On the other hand, the third class is characterized by heat transfer mechanisms which are achieved by heating gases externally (Holmes, Boss, Datcher & Heming, 1978). The fourth class incorporates the use of a mixture of solid particles to transfer heat. A typical example of multi-mineral retort is illustrated in the fig. below.
A typical example of the above ground retorting technology is evident with the Nevada-Texas-Utah Retort as discussed below.
The Nevada-Texas-Utah Retort is technically limited in meeting modern commercial demands for gas and liquid fuels. The design and construction of the Nevada-Texas-Utah Retort constitute an air supply pipe integrated into a vertical cylinder with a lining that reflects heat away from the surface wall. The bottom consists of a discharge mechanism and the top consists of a flexible charging mechanism.
During its operation, the NTU retort is charged with oil shale after it has been crushed into smaller particles and sealed. The top of the gas burner is set ablaze by allowing the flow of a gas to flow temporarily before being withdrawn. However, at this stage, the burning continues as the flow of air is maintained (Holmes, Boss, Datcher & Heming, 1978).
The Paraho Direct and Indirect Retorts
Resulting modifications of the NTU technology produces Paraho Direct and Indirect Retorts. Typically, the modification procedure involves turning the NTU upside down, making mechanical modifications on the NTU retort with a functionality that allows it to operate continuously. In theory, the Paraho direct retort had a technical and operational functionality similar to the gas combustion technology with projections of being commercialized. Several tests had been conducted using different variables and parameters (Holmes, Boss, Datcher & Heming, 1978). A technical design of the Paraho retort is illustrated with direct and indirect heating modes in the diagrams below.
The input mechanism flexibly allows raw shale to feed into the retort. The raw shale descends vertically downwards. At each stage of the descent, the raw material is heated to pyrolysis temperatures by a stream of ascending within the chamber. An arrangement of tubes within the structure collects the resulting oil and gas and immediately into separation equipments attached to the outside of the retort. The residual carbon is retained by the retorted oil shale. As the shale continues to move vertically downwards within the chamber, it is ignited by the burner bars to allow for further pyrolysis (Gardiner & Sanzillo, 2010).
Cooling of the descending shale occurs at the bottom of the retort when exposed to a stream of recycled gas. Once at the bottom of the retort, the resulting shale exists through the discharge grate at the bottom of the retort (Holmes, Boss, Datcher & Heming, 1978). The resulting shale is moistened and prepared for disposal at this point.
Indirect heating Mode
Different countries have developed different retorting technologies suited to the technical and industrial environment demands specific to the country. A typical example is the Petrosix Indirectly Heated Retort technology that was developed in Brazil in collaboration with other engineering firms from the USA. Technical specifications of the retort technology detail it to measure 18 ft in diameter with an operational capacity of 2,200 ton/d.
Operational differences distinguish the Petrosix retort with other retort technologies by the water discharge mechanism. Typically, the shale resulting from the process is released into a water bath that is transported as slurry to the dumping site. Other technologies include the union B retorts which have been proposed (Holmes, Boss, Datcher & Heming, 1978). These technologies are merited with the operational characteristics and efficiencies tailored to provide continuous and countercurrent retorts as illustrated in the figure below.
Typically, the retorting system is illustrated in the fig. below.
Evolution of oil shale technologies
In the recent past, notable evaluations of oil shale technologies have been experienced and on the rise. That is typically driven by the notion that technological innovation does not occur overnight, but is a process. In addition to that, these innovations are expensive and time consuming successfully reach a commercially applicable level (Crawford, 2008). A technology can only be deemed successful if it is efficient in addressing needs of the users, is economical, and is environmentally friendly. Typically, technologies evolve from the conceptualization stage to a functionally commercial scale in three stages. These evolutions are from the laboratory, to the evaluation or testing stage, and the commercialization phase (Crawford, 2007). The evolution concept is well illustrated in the figure below.
It is worth noting that each phase of the evolution process attracts more risks and uncertainties with increased capital expenditure and investment. The evolution process becomes iterative when failures are experienced anywhere in the evolution process. However, failure demands a lot more investments, rethinking, and redesign.
This is typical of the evolutions that have been experienced in the USA. In particular, new technologies are designed to address the challenges experienced with the use of old technologies and emerging trends in the global climate and economic challenges. The evolutions have further been reinforced by a better understanding of the organic structure and constituent components of oil shale deposits using modern research techniques (Crawford, 2007).
It is worth the argument that a number of companies and governments have already invested significant sums of money in researching developing and testing these technologies. Typically, these research projects are concentrated in the most cost effective access to research and extraction process, techniques for the recovery process of hydrocarbons to from the raw materials, and specific methods used by the prospecting firms in protecting the environment. Other additional issues include upgrading methods and manufacturing methodologies.
One of the most successful technologies in the mining of oil shale from the Alberta deposits had been developed for three years. The successful demonstration led to a successful development of commercial quantities of oil shale.
In practice, the USA had identified the recovery of oil shale to be commercially viable by 1978. An evaluation, after thorough research and experimentation as mentioned elsewhere, had been conducted, aggressive commercialization commenced.
At the time, surface mining had been evaluated and deemed to be commercially viable and of significant economic interest. It was then that a number of surface retorting technologies, discussed elsewhere, were developed and demonstrated to be viable solutions for the mining and recovery of hydrocarbons from oil shale. However, it was necessary to address the challenges that came with the old technologies. These included the need to establish technical reliability of the old technologies and associated costs, identification of appropriate technologies that could be in tandem with public and private investments attractions, and technologies that could meet regulatory constraints and standards (Crawford, 2007).
Advantages and Disadvantages of Technology
Each of the retorting technologies comes with its advantages and disadvantages. For TIS recovery technology, mining is not necessary. In addition to that, there is no disposal problem with spent shale as it is not brought to the surface. On the other hand, a myriad of technical problems and other associated problems with above ground waste disposal are avoided with this TIS technology. On the other hand MIS and AGR technologies involve above ground mining that comes with specific the technical and economic problems of waste disposal.
It is important to note that raw shale, when disposed above the ground, undergoes leaching through water contaminations which eventually allows soluble chemicals such as salts to seep into the ground affecting the quality of underground water. That calls for controls to be effected on MIS and TIS technologies (Holmes, Boss, Datcher & Heming, 1978).
In theory, TIS mining technology places minimal requirements on the surface facilities used in the recovery process. Integral to these requirements are oil recovery equipments, storage facilities, and other spare equipments that may be required in the mining and processing of oil shale. On the other hand, MIS requires more facilities compared with AGR and TIS in the mining and waste disposal methods. That demands more large facilities and has been noted to cause intensive surface disruptions during the mining and production process (Holmes, Boss, Datcher & Heming, 1978).
Oil Recovery
One of the most reliable technologies in the recovery of oil from oil shale is AGR. The technology allows operational parameters to be controlled to maximize oil recoveries. However, due to the difficulty of achieving a uniform distribution of oil shale with the MIS and TIS technologies, it leads to lower exploitation efficiencies of the raw shale. That is basically due to the inability to maintain a uniform burn fronts and the inability to capture heat through the heating systems.
A critical evaluation of the efficiency of the TIS technology indicates discouraging results when projected for large scale commercial scaling. On the other hand, MIS retorting has achieved less than 60% success in the recovery of oil from oil shale. However, the efficiency of MIS technology can be innovatively enhanced by making additional improvements such as the use of steam injections and in other places, the use of hydrocarbon gases (Crawford, 2007).
The main advantage of MIS technology stems from the ability to recover oil from low grade oil shale as a compensatory measure for its disadvantages. In addition to that, AGR and MIS require minimal preparations of the raw material that is used for the extraction of liquid hydrocarbons. The table below provides a comparative summary of the recovery of oil shale both in the first and second stages (Crawford, 2007).
Different Companies, their advantages and limitations are discussed for each respective company below.
Technologies, advantages and disadvantages
The new technologies have been identified to incorporate indirect supply sources of heat, use of direct current to provide the required heat, recycling of hot gases in addition to the transfer of heat between solids, use of micro wave sources of energy, and the incorporation of underground freezewall barriers to adequately protect water from the effects of pollutants. In addition to that, the barriers provide impermeable protection to the underground water and other sources of water affected by the mining process (Crawford, 2007).
A number of benefits have been documented from the use of modern technologies. Typically, new technologies have registered improved operational machine efficiencies. That is evident from the higher yield values per given raw material compared to the use of old technologies. Notably, a significant decline in the cost of capital investment for the mining of oil shale has been registered, allowing the recovery process to be a commercially viable venture. That is also in lieu of projected prices of conventional crude oil (Dyni, 2006).
Other benefits resulting from the use of modern technologies include appropriate monitoring of the impact of resulting activities on the environment and the ability to accommodate control measures to mitigate against adverse environmental effects. These technologies show a high degree of efficiency and reliability particularly with regard to In Situ recovery methods. In addition to that, new technologies identifiably have low water requirements since water can be cleaned and re-used all over again (Crawford, 2007).
Further research on emerging technologies indicate advances in the capture, use and storage of carbon dioxide as one of the by products from the recovery process of oil shale (Crawford, 2007).
A current report from the US government indicates up to 30 companies have moved into the full scale development and use of technology to recover hydrocarbons from oil shale. It is important to note that a significant number of the researched technologies are now in the enter phase of the development process. A profile of more than 25 companies has been provided with continued interest and active participation in the development of oil shale for domestic and industrial applications. According to the information contained in the company profile, detailed information featuring the technologies embraced by each company is provided. In addition to that, information about leases specific to each company and the role of each company in the recovery of oil from oil shale are listed below (Crawford, 2007).
Typical technologies used by each company are tabulated below (Crawford, 2007).
Descriptions
Anadarko Petroleum Corporation
Anadarko Petroleum Corporation produces up to 3.01 billion barrels with major operations concentrated on shores of the United States. Other areas of interest include China and Algeria with special interest in the Gulf of Mexico. To add economic value to the oil shale recovery process, the company has intense interests in the mining of hard minerals in various regions including Wyoming and Utah. The mining company endeavors to minimize the effects on the mining activities on the environment by capturing gaseous products such as carbon dioxide and disposing of carbon dioxide gas appropriately.
Typically, the role of the company in the exploitation of oil shale is that of a resource owner. A number of studies and explorations have been funded by the company. These include the Land Grant oil shales and several other coring undertakings. The following fig details the land holdings that the company operates. Projections have it that the company intends to lease out the land holdings to prospective companies for drilling and other research operations (Crawford, 2007).
The next company in the list is the Chattanooga Corp.
Chattanooga Corp
The company focuses the techniques involved in converting oil shale into synthetic crude oil for domestic and industrial applications. The company’s innovative edge has positioned it as leading developer of new oil shale recovery technologies with the registration of several patents in the processing of the raw material. The company’s main role is to establish partnerships with financial institutions and other interested parties such as governments to allow commercialization of the mining venture (Crawford, 2007).
Typically, the company’s operations rely on the pressurized fluid bed reactor technology. The technology relies on hydrogen heater conversions at relatively low temperature ranges estimated to average 573 ºC. The operating environment characteristic of the technology is non-combustion. However, modifications of the technology are possible to accommodate the raw feed oil shale into the desired hydrocarbon through thermal destruction. The technology is illustrated in the fig. below (Crawford, 2007).
Hydrogen plays a critical role in conveying heat to the reactant and the fluidizing gas. The heat source conveyed by hydrogen is captured from the processing gas that is heated by the fired heater. Typically, the need for natural gas as a heat source is minimized in this arrangement. The shale and sand discharge from the reactor provides a significant source of heat for the combustion air from the heater. In essence, the reactor has a high degree of flexibility allowing it to fit into many economic models.
To keep abreast with the objectives of modern oil extraction technologies and environmental regulatory requirements, the reactor overhead is designed to clean the reactor gases to particulate solids. Cooling and separation of gases and resulting components are achieved through the system. To ensure the sulfur content is kept to a minimum as possible, the resulting hydrocarbon is sparingly hydro-treated.
The process does not complete except for the removal of light hydrocarbons and the remaining hydrogen gas. A mine scrubbing system is employed to achieve the latter objectives. The circulating hydrogen and light hydrocarbons now made deficient of acids and other harmful substances are recompressed upon admission into the centrifugal compressor. The fired heater provides an additional functionality at this point by supplying heat for the steam used to drive the centrifugal turbine. To efficiently optimize the compressor power, a low pressure presence is kept around the process loop (Crawford, 2007).
The purification process of the resulting components proceeds as the resulting substances move through the phases. That provides the connection between the resulting components and the next phase in the process. The purified hydrogen gas is then fed into the compressor for further use. In addition to that, the light gases captured in the process serve to minimize the heating requirements provided by natural gas, making the whole system economically flexible.
The characteristic efficiency of the system results from a reduction of extreme hydrotreating at the initial stages when the system commences operations. As an additional benefit, the system operates to near self sufficiency since the byproducts and gases produced during its operation are used as feedstock for its operations. The sole supply of energy for all operations, therefore, is from its primary plant feedstock (Crawford, 2007).
As technologies evolve with time, one of the more important requirements is to fulfill the environmental obligations that come with its operations. Typical of the latter technology, the need for water is limited and sparingly used. That limits to a significant extent green house gas emissions. In addition to that, the technology provides the flexibility of degrading oil shale waste products making it easy to reclaim the land for future use. Another key benefit for this technology is the ability to reduce the sulfur content up to 99.8% of the product mass (Crawford, 2007).
A close examination of land holdings indicates that the Chattanooga Corporation hardly holds any shale oil land and tar resources.
An analytical study of available data indicates that the Chattanooga Process has had the technical capability to provide a yield equivalent to 51.5 gal/ton and an efficient fluidization of hydrogen (Crawford, 2007).
Further developments indicate that engineering firms have been contracted to develop a commercially viable plant with a projected capacity of 60,000 bbl/day. A fully operational demonstration model has been developed by the Chattanooga Corporation to allow for the integration of the process into other operations.
Chevron
The next company in the series is Chevron. Technologically placed as a leader in innovation and development in the energy sector, Chevron conducts business in the energy sector in over 180 countries in the world. The US branch of the company concerned with the development of energy is Chevron Shale Oil Company (Crawford, 2007).
Chevron plays the role of a resource owner, project, and technology developer. The company emphasizes developing in-situ mining approaches with small scale demonstrations projected to be developed and exploited for commercial scale. The company focuses on the use of crush technology illustrated in the fig. below.
Typically, the crushing technology emphasizes on the use of in-situ processing for the conversion of oil shale into the appropriate hydrocarbon for commercial, chemical, and domestic applications. Chevron’s crush technology is characterized by breaking oil shale into smaller sized rubble to enhance the surface exposure of the resulting kerogen using a series of fracturing machines. The fractured kerogen is chemically processed to the final hydrocarbon product. The recovery process of the resulting hydrocarbon is made complete and later upgraded to the established standards and specifications (Crawford, 2007).
The company is located on a 160 of land under the lease of the U.S. Bureau of Land Management. Once the company successfully demonstrates its technology to be of commercial viability, it is projected to offer up to 5,120 commercial leases. Projected tests of the oil shale recovery technologies are proposed to cover a small number of field and laboratory tests. These tests have no specific timeline for the land lease.
However, it is projected that the tests will be carried in a series with definite results to inform the next phase. The first phase will involve fracturing of the raw shale to produce the first pattern as the feed for the next phase. The next phase is 2 year repetition process of the first phase, leading on the third phase. However, the third phase is concerned with gathering and analyzing the test data to make informed decisions about the viability of investing in the mining and recovering of oil from oil shale. The next company in the series is the common wealth raw materials (Crawford, 2007).
Commonwealth Raw Materials
The above company plays the role of a resource owner and occupies a total of 50 acres of mineral land. Estimated reserves are in the range of 1.5 BBL typically characterized by sandstone deposits (Crawford, 2007).
Technologically, the company is in its initial stages of development in evaluating the oil shale deposits in its areas of operation. The pilot programs focus on the use of EOR technologies. These technologies are proven in various operational respects. The next company of interest is E.G.L (Crawford, 2007).
E.G.L
E.G.L is a resource and technology developer specific to the exploitation to commercial scale of oil shale. Typically, the company has been characterized by innovations in oil shale development technologies. One such success in the innovation is the development of an in-situ recovery process. In addition to that, the company has made advances in establishing a research consortium aimed at testing and validating test results on the commercial viability of the recovery of oil shale with different technologies. These technologies have been developed by different companies to exploit and recover hydrocarbon oil shale for domestic, commercial, and industrial applications.
The consortium will focus on the use of modern technologies such as computer modeling to study the benefits of using specific technologies for the oil shale recovery process. In addition to that, the study will be used for conducting hydrological studies and the impact of the recovery process on the environment (Crawford, 2007). Environmental studies will involve technologies for capturing gases with adverse environmental impact, approaches to managing the water used in the recovery and processing of oil shale, and access to a database of information about oil shale technologies (Crawford, 2007).
An examination of E.G.L’s technologies indicates that it focuses on the use of thermal methods in the extraction process which are integrated with modern proven oil drilling technologies. E.G.L focuses on developing technologies for use in in-situ processing with special emphasis on the closed loop approach. The closed loop approach has various advantages. Typically, the technology has been proven to be energy efficient and environmentally controllable (Crawford, 2007).
The processing of oil shale specific to this technology involves the use of a series of pipes to below the oil shale bed and thermally decomposed with the heat from the underlying pipes. Pipes are vertically positioned to provide a gateway for the passage of oil and gas and transferred through a spider of pipes that are used to create a link between the heating and liquid hydrocarbon production systems. The following fig. illustrates the structure of E.G.L’s technology.
The functionality of the technology is based on conventional and refluxing mechanisms to enhance the movement of heat from source to the destination oil shale retort. To optimize system efficiency, the process uses gases generated from the retort to meet the heat requirements for the extraction and recovery of liquid hydrocarbon from the oil shale. In the process, heat losses are minimized through a heat recovery mechanism from the shale rock. To ensure system stability, heat transfer is achieved through a lateral piping mechanism (Crawford, 2007).
It is important to note that water recovery and use remains to be a critical element in the process. Various water treatment and recovery mechanisms are used to ensure re-use and minimal contamination with the environment. The next company worth considering is the Electro-Petroleum, Inc (Crawford, 2007).
Electro-Petroleum, Inc.
Electro-Petroleum, Inc., company has its facilities located in Coleraine and works with the research institute of the University of Minnesota. It also works in conjunction with the Canadian Government and several oil development companies. A number of field demonstration facilities have been proposed and in the offing (Crawford, 2007).
Typically, the company emphasizes on the use of direct current (DC) for the recovery of hydrocarbons from oil shale. In addition to that, new electrochemical approaches have been devised and patented for the recovery of oil from oil shale. The use of direct current allows for cold cracking of oil shale. Typically, electrically enhanced oil production (EEOP) has experienced recent developments due to the technological and operational benefits associated with the technology. A detailed evaluation of the technology reveals it to be a low cost extraction technique compared with other technologies (Crawford, 2007).
It is important at this point to examine the operational details of the technology to crystallize an understanding of operational efficiency and requirements. Essentially, the technology is characterized by the use of cathodes and anodes which are inserted into wells and through which an electric current is allowed to flow. The cathode forms the negative side of the current while the anode forms the positive side. When an electric current is allowed to flow into the well, it causes a heating effect which reduces the viscosity of the oils allowing for more flexibility for further processing. A conceptualization of the set up is illustrated in the fig. below.
A number of EEOP field tests have been conducted to evaluate the commercial viability of the technology in the Eastern Alberta among other areas. Typical benefits specific to the technology included reduced water usage, low emissions of hydrogen sulphide, higher specific gravity of the crude oil, and higher amounts of gas production. In the evaluation process, comparisons with baseline production approaches were done and the results were as tabulated below (Crawford, 2007).
It is important to consider the effects of Electro-osmosis as an additional technological benefit from the use of EEOP. Integrating the technique leads to the creation of a driving mechanism, enhancing the efficiency of the systems further (Crawford, 2007).
As an additional benefit typical of the EEOP technology, large organic molecules can be reduced into finer particles and the resulting hydrocarbon upgraded by resulting into a lower viscosity coefficient. In addition to the above mentioned benefits, there is marked system efficiency, cost effectiveness, demands limited water supply, and does not require a working fluid in its functionality (Crawford, 2007).
One of the challenges that modern technologies endeavor to address is the impact on the environment resulting from associated activities. One such environmental effect is the green house gas effect. The EEOP technology has been proven to minimize the production of green house gases, a desirable characteristic in the modern age of global warming. Another company involved in the development of oil shale particularly in the USA is Earth Search Sciences, Inc., as detailed below.
Earth Search Sciences, Inc.
The Earth Search Sciences, Inc. focuses on the use of cost effective technologies in the search for oil shale deposits that are of commercial quantities. Typically, the company uses proven technologies that have been identified to be environmentally friendly. The company is in partnership with other companies such as Petro Probe in the search for hydrocarbon deposits of commercially viable quantities (Crawford, 2007).
The technology used at Earth Search Sciences, Inc., involves passing a blast of hot air that has been superheated down a borehole. The oil shale below interacts with the super heated air getting converted into a gaseous matter and transferred to the surface where the recovery of the liquid hydrocarbon process occurs (Crawford, 2007).
In practice, the process has been proven to be much efficient and involves quick product recovery since no mining occurs during the hydrocarbon recovery process. Typically, the mining process involves creating a hole into the oil shale with a conduit pathway built into the drilled hole. In addition to the inlet hole, an effluent hole made at the bottom surface of the hole provides another communication point. The conduits act as inlet and outlet points for the superheated gas that causes kerogen to be created from the raw oil shale and transferred to the surface respectively. At the point of affluence, gaseous products are allowed to escape and an oil recovery is made (Crawford, 2007).
A number of advantages associated with the technology include its self sustaining capabilities, environmental friendliness, and the use of in-situ recovery methods into depths of up to 3,000-plus feet. Close to 94 to 99% of the oil structure remains intact after the mining process. The conceptual structure of the mining process is illustrated below.
An additional benefit is the portability of the system. Typically, the system can be dismantled and reassembled at different points for use at any site with oil shale deposits. The next company is ExxonMobil (Crawford, 2007).
ExxonMobil
ExxonMobil is one of the most established companies in the research and development of oil shale and other aspects of energy development. Typically, the company is solely a resource owner, a project developer, and technology innovator. Typically, the company has concentrated its growth and development of oil shale using an in-situ development process. In an innovative approach, the company emphasized more advanced developments in technology with special emphasis on advanced in-situ mining approaches. The drive for the paradigm shift is reinforced by a focus on cost effectiveness and commercial feasibilities (Crawford, 2007).
A conceptual design of the technology used by ExxonMobil is illustrated below.
Typically, the Electrofrac™ is the candidate technology identified by ExxonMobil as most feasible for in-situ oil shale oil recovery process. The technology employs a fracturing method on oil shale through a thermal in situ process. The thermal effect is further enhanced by use of a conductive material. The fractures are organized in series both vertically and horizontally. The geometry of the setting allows other parts to be visible while other parts remain invisible.
Importantly, electricity is conducted both from top to bottom in the vertical and horizontal settings as illustrated in the diagram. The approach to using this technology as a result of intensive comparative studies and evaluations of various candidate technologies to crystallize the current one as the most feasible. An additional innovative benefit is the use of planar heaters that allow heaters to be used in limited space (Crawford, 2007).
It is important to note that the company has conducted intensive evaluative studies on the technology on a small to a large scale. In addition to that, various other areas for consideration for further detailed research are underway. The following map provides a detailed view of the region under ExxonMobil exploratory and recovery for oil shale (Crawford, 2007).
Extraction methods
Various extraction methods have been developed over the years with varying operational efficiencies. These include pyrolysis, thermal dissolution and hydrogenation. Typically, the component of interest in the organic fractions is kerogen. The constituent components that make kerogen are also dominant in petroleum source rocks, providing a similarity between the organic raw materials for petroleum and kerogens. A geochemical study of the Green River shales was conducted on different samples in the study of the pyrolysis as an extraction method. Typically, these shale deposits were typical of the thermal evolution of type I and type II (Jeong & Patzer, 1983).
Analytically, the Green River basin oil shale deposits consist of 30-36% and 30-40% carbonates and silicate minerals respectively. Three samples taken for study showed similarities in the composition by bulk. The constituent minerals identified included quartz, albite, calcite, and clay. An elemental analysis conducted on the three samples indicated similarities in the organic composition of the samples. Further analysis and density separations conducted on the samples resulted in richer shales without any significant variations in the organic composition. However, variations in the constituent mineral components were typical of the geological source of the each of the oil shale sample analyzed (Jeong & Patzer, 1983).
A thermogravimetric analysis conducted on the samples yielded varied results of the samples used in the analysis as shown below (Jeong & Patzer, 1983).
A differential analysis of the resulting curves leads to the conclusion that two regions exist of high volatility in product release. These occur at 465 ºC and 760 ºC. Markedly, a region of weight loss experienced in the procedure occurs at 200 ºC due to water loss. At 465 ºC, organic pyrolysis dominates. Further analysis of the temperature graph for temperatures below 500 ºC and above 350 ºC indicates a broad mixture of hydrocarbons which cannot be easily separated into constituent specific organic compounds. Other constituent minerals such as silicate minerals did not experience ant organic decomposition in the process. That reinforced the rationale for organic pyrolysis. A further analysis of the thermal behavior indicates thermal decomposition at 730 ºC. However, carbonate free oil shales do not show this property (Jeong & Patzer, 1983).
Another dominating feature specific to the thermal analysis is the 520 ºC carbon transition temperature of the organic kerogen during the pyrolysis process. During the pyrolysis process, other carbonate groups identifiably undergo thermal decomposition at 730 ºC. That typically suggests that the pyrolysis of the oil shale is significantly influenced by the presence of pyrites as a constituent component of the oil shale. However, during the experimentation process, the oil experiences a weight loss at 700 ºC (Jeong & Patzer, 1983). Typically, the weight loss due to the pyrolyzed organics ratio provides information about the pyrolysis yield of specific raw material.
An observation of the pyrolysis yield shows significant rises when the organic content rises accordingly. It is important to note that temperature changes affect the concentrations of calcites in shale. Comparatively, dolomites decompose at lower temperatures than calcites. In the above experimental settings, different samples of oil shale from different locations were subjected to pyrolysis investigations with different results as tabulated below (Sørlie, Bityukova, Sæther, Rudolph-Lund, Kahru, Vallner, Petersell, Razgonjajev & Põllumaa, 2004).
Typically, the carbon decomposition characteristics were made absent during the pyrolysis process. Samples from the eastern region registered 47.4 wt % samples form while elsewhere registered higher percentages. Conclusively, samples for different actions varied significantly in the hydrogen content specific to each shale (Jeong & Patzer, 1983) and (Clough & O’Rourke, 1990).
Problems
Problems with Technology
Over the years, since the discovery and development of oil shale, a number of problems have been experienced with the technologies used in the development of oil shale. Arguably, each technological innovation comes with its problems which need to be addressed. Problems with technology may be common to all regions exploiting oil shale as a resource for the development of hydrocarbons or may be unique to each region. The following is a critical discussion of problems with technology in the recovery of oil shale in China. The discussion helps to crystallize other technology related problems typically experienced in other countries (Chaohe, Dewen & Dexun, 2008).
One of the problems is the ecological damage resulting from the burning of oil shale as a source of power to run the machinery used in the extract of the raw material. In addition o that, further energy demands for the refining process oil puts further demands for energy for the thermal destruction of the raw material. It is important to note that during the mining process, ground water presents very serious technological challenges when attempting to lower the ground water levels to allow for the recovery of the raw material. One challenge experienced with the mining of oil shale is the level of ground water.
When recovering oil shale through the surface mining approach, the water level has to be reduced to a level below the kerogen bearing rock. Engineering equipments used on site use electrical energy generated steam driven generators. Typically, the burning of oil shale to meet the energy requirements for generating heat for the conversion of water to steam comes with a four specific problems (Chaohe, Dewen & Dexun, 2008).
One of the problems includes the corrosion of metal surfaces of the containment used in the radiant transfer of heat. That caused the lifespan of the firebox to be limited hence regular demands for the new replacements. That makes plant maintenance costs to appreciate drastically. Another associated problem with the heat used in the boiler is the effect of ash clogging. It is possible to achieve such high temperatures when pulverizing a coal fired boiler in during the recovery of oil shale to cause the serious effect of ash clogging.
It is important to note that gaseous substances generated during the oil shale conversion process are likely to cause leakages and explode in the process. Such a situation may lead to the destruction of property and lives. Thus, the operating environment becomes a potential risk to life and machinery (Chaohe, Dewen & Dexun, 2008).
During the recovery process, oil shale is subjected to thermal destruction processes to extract hydrocarbon liquids and gases that are important sources of energy. During the recovery process, the enthalpy of combustion of oil shale should not fall below a minimum value. When the hydrocarbon content is low, the calorific value of the brining oil shale may fall below a given value to demand for further injections of additional energy from an external source. That adds to the problems experienced in the mining and extraction process (Chaohe, Dewen & Dexun, 2008).
One typical observation in the above respect is the fluidized bed combustion technology. The combustion intensity of oil shale has been identified to be typically low for the fluidized technology with unparalleled demand for a large operational space. On the other hand, the usage of the technology places demanding requirements for a large sized bed area with the structural complexity adding to the problems. It is important to consider the effects on the environment as a precursor to its destruction (Chaohe, Dewen & Dexun, 2008).
Noteworthy, China has the second largest deposits of oil shale in the world. In addition o that, China has aggressively invested in the mining and recovery of oil shale as a raw material for the kerogens which are the principal sources of liquid and gaseous hydrocarbons. The thermal destruction of oil shale requires the injection of heat energy. The resulting use of heat as a thermal modification tool for oil shale occurs under different technologies. A typical application of the thermal recovery process includes the in-situ conversion technology (Chaohe, Dewen & Dexun, 2008).
The in-situ conversion process demands intensive applications of heat on oil shale before the resulting hydrocarbons are recovered from the ground and transported to an upgrading plant. A typical process for oil shale retorting comes with a number of benefits and disadvantages as tabulated below (Chaohe, Dewen & Dexun, 2008).
On the other hand, the in-situ recovery process involves applying heat directly on the parent oil shale rock to crack and recover the necessary oil. A critical evaluation of the process indicates that the in-situ recovery method is optimally beneficial when making deep oil shale recoveries (Brendow, 2003).
It is important to remember that heat energy requirements for the recovery of liquid hydrocarbons and gases from oil shale can also be met by use of electrical means, fluid heating means as highlighted above, and radiation heating processes.
A comparative evaluation of the in-situ technologies used by different companies discussed in the report is tabulated below.
To understand typical problems with extraction of kerogens from oil shale, it is important to understand the extraction methods used in the development of oil shale to inform an understanding of the problems with extraction below.
Problems with extraction
It is important to briefly discuss about extraction methods before examining problems with extraction of oil shale.
Problems with Oil Shale Extraction
A number of problems are experienced during the extraction of oil shale. The complex nature of oil shale deposits, large energy requirements, large land and industrial infrastructure requirements add to the problems of extracting oil from oil shale. Typical industrial infrastructure requirements include power distribution lines, a network of roads, pollution from the consumption of large amounts of energy derived from burning coal, water storage and piping systems, and water storage facilities.
Other additional problems include ecological disposal of oil shale wastes leading to the contamination of underground and above ground water as discussed elsewhere.
A typical tabulation of the extraction methods and associated problems are illustrated below (Miller, 2007). However, it is worth noting that a few oil shale recovery technologies have been focused on in the detailed tabulations below.
What happens to earth structure after the mining of oil shale
The development and recovery of oil from oil shale has the potential to disturb the natural land formations in the oil shale development locality. Both above ground and underground mining lead to large displacements of earth and related materials creating new structures such as waste deposal sites and earth cavities. However, with modern approaches to oil shale developments, new approaches to landfills and recovery of oil shale development sites to restore the sites have been adopted.
What happens to the environment after extracting?
Each of the extraction technologies suffers from common environmental problems across the board. Some of the environmental impacts have already been discussed elsewhere in this document. Further discussions are centered on additional recovery technologies as discussed below.
Modified In-Situ (MIS)
A typical illustration of the MIS technology is illustrated in the fig below.
Typical of the MIS technology, qualitative environmental factors are characterized by a large carbon footprint with an external power source that is moderate. The demand for water usage is very high with moderate demands for ground and surface water. In addition to that, the potential to impact on the quality of air abounds (Bartis, LaTourrette, Dixon, Peterson & Cecchine, 2005).
Other technologies and potential environmental impacts are tabulated below.
Does it affect the climate change?
Potential impact on climate change is one of the concerns that have emerged as the recovery of oil shale gains momentum (Boak, 2007). Arguments presented on the potential impact on the environment recognize a strong correlation between environmental changes and the oil shale mining and recovery activities. Arguments based on the above information reveal the technologies to be among the contributing sources of carbon dioxide, the chief contributing gases to the green house gas effects (Boak, 2007). Boak (2007). shows that large quantities of carbon dioxide are produced by oil shale industries during the recovery of oil from oil shale.
In theory, models have been developed to explain the expected emissions of carbon dioxide into the environment. Significant research however indicates that the recovery of oil shale comes with large quantities of CO2 productions into the environment. These exhaust are likely to tip the balance of the additional amount of green house gas emissions into the environment with consequent effects (Boak, 2007).
Environmental impact
In addition to that, the potential impact on water as a natural resource, a factor of the oil shale recovery process is a cause for concern. In the following discussion, a critical review of the impact on the climate will be discussed and critically analyzed to crystallize information on the environment. Among the environmental elements typically correlated with the oil shale recovery process include:
- Water
- Geologic Storage
Water
Water is one of the critical and principal substances that enhances the mining and recovery of oil from oil shale. The technologies involved emphasizes on the use of significant amounts of water. Water requirements have been estimated by different authors and tabulated results are shown below.
However, it is worth noting that not all steps in the recovery process demand water, but rather lead to the generation of water. However, the resulting water from oil shale retorting constitutes dissolved inorganic and organic compounds that present further environmental challenges (Brown, 2008). The results of comparative studies by different authors on water requirements for retorting are tabulated below.
Typically, both underground and surface mining have been identified to release large amounts of chemicals and other chemical holding rubble that comes into direct contact with both underground and surface water. Typically, the quality of water gets adversely contaminated and affected with various chemical substances (Brown, 2008). A case study of the effects on oil shale recovery on the quality of water in the oil shale deposits covered by the Colorado River and other US oil shale potential areas will help crystallize the environmental impact stemming from the use of water in the oil shale recovery process (Chan, Duda, Forbes, Rodosta, Vagnetti & McIlvried, 2006). A geological survey of the oil shale bearing regions indicates the existence of a substantial amount of ground and above ground running water. Underground water is usually buried within the oil shale bearing rocks and must be disturbed during the oil shale recovery process (Brown, 2008).
A typical illustration of the discharge process for the surface and underground water is illustrated below.
The above diagram provides a cross sectional area of the drainage system in the Piceance and Yellow Creek Basins. It demonstrates in the diagram different strata of the oil bearing basin. An analysis of the characteristics of the water within the Piceance and Yellow Creek Basins region reveals the deposits to contain large quantities of saline water covering several acres of land and briny water. A typical examination of the above diagram indicates the aquifer system to contain close to 80,000 acre-feet of water. Deeper aquifers are estimated to contain close to 10,000 mg/L of TDS.
To analytically provide further understanding of the environmental impact on water, it is important to discuss the various types of impact for the process. The impact assessment covers both ground water quality and specific impacts and surface water quality and associated impacts.
Ground Water Quality
The impact on the quality of ground water leads to destructive effects on aquatic habitats on local water streams. Runoff water that has been used in the retorting process and surface mines containing oil shale particles as mentioned elsewhere act as agents in transporting the oil shale wastes into the environment. In addition to that, dewatering of the oil shale consumes large quantities of surface water which is discharged into the environment (Brown, 2008). The discharges cause further environmental disturbances ultimately affecting the quality of water. A typical tabulation of the effects is illustrated below (Chan, Duda, Forbes, Rodosta, Vagnetti & McIlvried, 2006).
A typical analysis of the impact on the quality of ground water during the disturbance of oil shale deposits to make recoveries indicates that the hydrochemical conditions of the ground water get significantly modified. The modifying factor with the most significant impact is the retort temperature of the retorting mechanisms. Further analytical results show a strong correlation between the presence of carbon dioxide and the hydrogeological regime in oil shale. Water flow takes the nature of the thickness of oil shale. In addition to that, the sulfate content in the mining ground gains a high prevalence affecting the ultimate quality of ground water.
In conclusion, therefore, it has been demonstrated that the quality of water particularly in the Colorado region is affected by the salinity level in the water, sewerage and other waste water products, and high concentrations of organic and inorganic compounds affect the overall quality of water and consequently the living organisms that depend on the water Chan, Duda, Forbes, Rodosta, Vagnetti & McIlvried, 2006).
Geologic Storage
Though the technologies of storing CO2 are not new, research finding indicate that the storage locations have the potential to cause green house gas effects. That may be due to the probability of the gas leaking into the atmosphere leading to the modifying effect on the environment. Typically, that may also be due to faults that occur along the earth, the possibility of earth movements creating faults allowing CO2 to escape into the atmosphere, and the possibility of brackish water seeping into the underground waterways Chan, Duda, Forbes, Rodosta, Vagnetti & McIlvried, 2006).
Others
Other effects on the environment are directly related to the extent to which oil shale developments disturbs the l rand on which the oil shale recovery occurs. Analytically, topographic changes are arguably some of the consequences related to the disturbance of land. Though the discharged water into the environment is usually treated to remove additional chemicals, the potential for non point discharges are possible since no framework or legal policies have been developed to address the issue Chan, Duda, Forbes, Rodosta, Vagnetti & McIlvried, 2006).
Other issues include the occupational health due to the polluting effect on workers. In addition to that, the derivatives of oil shale are likely to create a further scenario in the employee health. Several suggestions have been fronted and policies designed to address the various environmental issues. Among the suggestions included
Carbon dioxide is one of the principal issues related to the recovery process of oil shale. Typically, scientific research has demonstrated carbon dioxide to be one of the key principal factors contributing to climate changes. Chan, Duda, Forbes, Rodosta, Vagnetti & McIlvried, 2006).
What happens to the earth structure when and after extracting
The mining and extraction of oil shale form the genesis various impacts on the structure of the earth structure. A typical analysis of the resulting structure indicates that the depth of the earth varies with different site characteristics and the overburden, the surrounding environment, infrastructure, waste disposal technologies and policies, and the technology being used in the recovery process. To remove the top soil, all characteristic properties of the overburden have to be determined in advance (Rubenson & Pei, 1983).
Other factors influencing the remaining structure of the earth are the thickness of the overburden, the thickness of the oil shale, the slopes that define the mining landscape, the rate at which the oil shale is produced, and the lifetime of the mine (Ergun, n.d). These parametric factors influence the structure of the earth as typically exemplified in the following illustration.
Typically, the resulting structure is illustrated in the fig below. In the following illustration, the fill develops into a physical structure after the shape of a mountain.
As the mining advances in the direction of the arrow, the total capacity of the mine and resulting backfill advances in size. Typically, the land topology gets shaped up from the resulting deposits (Rubenson & Pei, 1983).
Problems with Development
Various problems are experienced with different development methods across the board. Among the factors that inform the challenges and problems experienced in the mining process is narrowed to the flaw that is experienced in the interlocking of various system wall maintaining reinforcements as illustrated below. Typical problems include water seepage into the structure across braced walls (Ergun, n.d).
The above figure provides an illustration of the inside view, sectional view and the plan view of an in-situ braced walls of the recovery structure (Ergun, n.d). Typical advantages of the approach include wide availability of the pile retaining reinforcements.
Other related problems include the ability of the reinforcements to retain the walls and prevent leakages of water into a retort, the technical challenges of identifying and appropriate materials and wall reinforcement technologies (Ergun, n.d).
Typical Areas with Uncertainties
The major areas of uncertainty in the recovery of combustible fuels from oil shale include the risks associated impacts with the recovery of oil shale. These uncertainties include the unavailability of sufficient amounts of water for the recovery process, social and political views, economic feasibility and certainties about a steady supply of raw oil shale. Typically, oil shale technologies require large amounts of water for the recovery process, putting more stress on the already available water resources. Another area of uncertainty involves regulatory risks with respect to potential for controlled emissions of green house gases including CO2. The requirements for low carbon emissions and other stringent requirements pose serious challenges to the recovery process of oil shale as it is an energy intensive process.
No carbon capture cost estimates have been reliably developed including the commercial viability of carbon capture trading. In addition to that, policies financial incentives, and limitations about carbon capture in the market still add to the uncertainties associated with the oil shale development.
Other areas of uncertainties include limitations to the available technologies, process uncertainties, negative public views and opposition to oil shale development projects, and capital and carbon costs.
Development
Objectives
As new technologies emerge, new challenges in the recovery of oil from oil shale to meet domestic and industrial demands should be addressed. These challenges and associated objectives in the oil shale recovery industry include:
- Ensuring adequate protection for ground water.
- Ensuring the quality of ground water is adequately protected from in-situ mining activities.
- Ensuring the quality of air is preserved during the mining process.
- Ensuring the water is adequately conserved.
- Ensuring that emission of air carbon dioxide and other gaseous products are kept to a minimum compared with emissions from petroleum products.
- Ensuring the recovery process is technologically efficient.
These objectives and challenges have formed the basis for significant improvements in the evolution of the technology used in the recovery of oil shale. It is important to note that the evolving technologies should address the problems and challenges evident in old technologies and modern challenges which come with the mining process. Typically, these challenges are specific to mining methods specifically In Situ (IS) method.
Countries producing oil shale and recovery methods
Different Mining Processes
The physical and chemical properties of oil shales and the depth of formation from the ground typically determine appropriate mining and processing technologies. That allows the recovery process typical to be of commercial value. These mining and processing technologies are characterized by specific units of operations, specific mining methods for the extraction and removal of oil shale from the ground, and typical retorting methods for the destructive conversion of oil shale to liquid hydrocarbons. In addition to that, upgrading methods are used for the conversion process for commercial grade liquid hydrocarbon products.
Different steps in the conversion process, government policies in addition to the potential market for the derived oil shale fuels influence the technology to be used. However, these technologies have characteristic uncertainties that demand for further research to be conducted with each operation (Holmes, Boss, Datcher & Heming, 1978).
Mining
A generalized process is illustrated in the diagram below.
Different mining approaches specific to the depositional level of the oil shale deposit are used. Typically, these include the MIS and the AGR approach. In addition to that, the depth of the crop and associated thickness and spread determine whether surface mining or in-situ strategies are used in the mining and refining processes. Other topographical features, the prevalence of ground water, and the level of overburden typical of the deposits are other influencing factors (Holmes, Boss, Datcher & Heming, 1978).
A critical evaluation of the mining methods implies that surface mining is best suited for oil shale deposits that are close to the surface. The Wyoming and Uinta basins are best suited to surface mining. However surface mining is susceptible to exposures due to surface erosions which create gorges, canyons, gulley, and a host of other geographical features that impede the mining and processing of the oil shale (Holmes, Boss, Datcher & Heming, 1978).
Arguments out of favor with the mining of oil shale and processing of oil shale emphasize the leanness of oil shale in containing additional components as an economic disadvantaged. However, to make the prospects of oil shale an economically viable venture, economists propose the use of massive mining installations for all mining methods. Both mining methods are used at this stage(Holmes, Boss, Datcher & Heming, 1978).
Surface Mining
Surface mining has been identified as an economically feasible method particularly for deposits close to the ground. The mining methods are typically characterized by open pit and strip methods. These methods have undergone several developments, particularly during the last century. Research on both mining methods has shown that dynamic developments for both methods with time have been done (Holmes, Boss, Datcher & Heming, 1978).
An economic evaluation of surface mining suits it for deposits close to the surface and occur in large quantities. These allow for large scale mining with quick recoveries in addition to the exploitative and efficient use of space. Researchers estimate the recovery level to be close to 90% of the oil shale deposit that is characteristically very thick. Further research on the exploitative use of strip mining provides more efficient recovery results.
On the other hand, it has been demonstrated that underground recoveries have been estimated to be close to 60%. That vindicates the rationale for competitive bidding that characterizes open pit methods (Holmes, Boss, Datcher & Heming, 1978). Practical estimates indicate that a recovery through the open pit method is five times more than the underground method. A typical example of the open pit oil shale is illustrated in the fig. below.
The above fig demonstrates a mature open pit that has been blasted and drilled to remove the overburden above the oil shale deposits. To enhance the mining process, the overburden is removed and transported using trucks for disposal. The mining process creates deep holes which extend into the oil shale deposits which are found deeper into the ground (Holmes, Boss, Datcher & Heming, 1978).
An analysis of the forces that act on the walls of the pit indicates that the walls of the pit experience significant forces that act vertically and laterally on the walls due to the overburden. However, to overcome the effects of the pressure, the walls are angled to allow for the distribution and transmission of pressure to minimize the possibility of collapsing. Open pit mining had been proposed as the best approach suited for mining oil shale deposits particularly occurring at block C-a. It was proposed that the mining could begin from the Northwestern part before proceeding to cover the entire region of above ground retorts.
A technique, which involves the removal and refill of the resulting open ground, had been proposed. However, the mining never proceeded, though it had been estimated to be of commercially viable quantities. The impediment was particularly due to the problems typical of the offsite waste disposal plans.
On the other hand, strip mining involves removing the overburden using machines specifically designed to fulfill the technical challenges experienced with this approach. In this case, a massive scraper shovel can be used to fulfill the technical requirements of shifting and filling the scoop into areas that have already been mined. A typical advantage of this approach over the open pit approach is that the disposal occurs on site. However, prospecting firms have not proposed the approach for use in mining within the Green Valley deposits (Holmes, Boss, Datcher & Heming, 1978).
Notably, surface mining is limited by the thickness that characterizes the overburden covering the oil shale deposits. That is typical of the Piceance basin with an overburden reaching up to 2000 ft. These deposits are typically of lean concentrations. However, these deposits are of favorable thickness and body ratio in terms of the economic benefits allowable. Below is an illustration of the open pit mining process. It is important to consider the rationale that reinforces the need to mine oil shale using this method. Established figures indicate different stripping ratios for different mining techniques. A 2:1 ratio is favorable for strip mining while underground mining favorably operates with the ratio of 5:1 (Holmes, Boss, Datcher & Heming, 1978).
The economic rationale of removing large quantities of overburden to recover oil shale in depths close to 2000 ft should be vindicated if a return on investment (ROI) forecast to shows a strong positive trend.
Underground mining
Oil shale deposits may be geologically positioned to demand the underground mining method for the recovery of the raw material. Many underground methods have been proposed in theory but with no significant applications in practice. One of the underground mining methods that have received significant focus is the room-and-pillar method. Typically, this procedure involves creating large sized rooms underground by removing some shale.
This procedure leaves a significant amount of shale to act as the supporting wall for the rooms. Prevalent physical properties of the oil shale walls are determined by the thickness of the oil shale deposits and the thickness of the overburden and the depth of the oil shale. In practice, most of the oil shale deposits are rarely defined by faults, very thick, and of much economic value (Holmes, Boss, Datcher & Heming, 1978). This thickness allows the ore to withstand lateral and vertical pressures and other forces that may be exerted the large rooms created underground. This approach allows a great deal of oil shale to be recovered making the exploitation an economically viable venture. Below is an illustration of the concept of the underground mining method.
Oil Shale Processing
To prepare oil from oil shale for the consumer market, the raw material has to be subjected to a series of processing steps. Typically, the number of processing steps is determined by the ultimate by-products matrix needed. These processes are distinctly classified into TIS (True In Situ) which operates by injecting high temperature fluids into the underground deposits, MIS (Modified In Situ), which involves the use of explosives to create a passage for high temperature fluids, and AGR involving crushing and preparing the oil shale raw material into the precursor material for the processing and extraction of the liquid hydrocarbon as illustrated in the figure below.
The above illustration is a flow sheet for that can be incorporated into the AGR production facility as illustrated in the fig below.
The mining process begins by crushing and preparing the oil shale either for above ground or in-situ processing. These two processes provide oil shale as a raw material that is reduced to appropriately sized particles for heat transfer purposes. It is possible to obtain Nahcolite ore as one of a byproduct at this stage. This step produces water and dust as waste products before entering the next processing step. To prepare the resulting material for subsequent processing, preheating of the resulting components produces a material for pyrolysis. The pyrolysis temperature is approximately 535 ºC, leading to the formation of crude shale oil.
Resulting byproducts from this stage include contaminated water that is of environmental concern, spent shale residue, carbon dioxide which is released into the environment, and to a lesser extent a combination of dawsonite ore and nahcolite.
As a cost benefit measure, the crude oil shale undergoes further upgrading for transportation to the refining point. This step enhances the hydrogen content level of crude shale oil after undergoing a chemical and physical process to remove additional components which may include sulphur and nitrogen. However, in-situ processing does not require further crashing and preparations for the precursor oil shale raw material. Additional waste products include contaminated air and water, and gases that are rich in compounds of sulphur and nitrogen (Holmes, Boss, Datcher & Heming, 1978).
The quality of oil shale syncrude depends on the pretreatment done on oil shale crude material before the final processing is done of the resulting oil shale crude. An onsite or offsite refining process to add hydrogen to syncrude to obtain the final product for the market, such as gasoline and diesel oil defines the last processing step.
A number of political and environmental issue and regulations demand that the resulting byproducts particularly water be treated before reuse in accordance with Federal air pollution standard requirements. Typically, because of the circulatory nature of water used in the refining process, underground sources of water are in danger of getting infected. That is particularly because of the chemical compounds that infect water in circulation. Therefore, additional processing to remove impurities in the air and water for reuse has to be done.
Typical benefits realized with the processing of oil shale includes by products such as ammonia and sulphur for industrial use. Additional by products include retorting residues that form the basic source of soda ash and aluminum (Holmes, Boss, Datcher & Heming, 1978).
Development Methods
A conceptual framework of the development of oil shale is discussed below.
In the above layout, the overburden is 270 m below a nonreactive overburden. On the other hand, the raw oil shale is 320 m thick. In practice, larger cells in the layout have the advantage of accommodating smaller sized oil shale retorts which result in optimal use of heat and energy. However, it is not possible in practice to estimate the actual size of retort to justify an efficient conversion. However, it can be demonstrated that the disturbance per cell is intensive for this technology and needs to be addressed when selecting it for the conversion process. In addition to that, the thickness of the oil shale resource, the resource topography, and related surface features are strong influencing factors in determining the level of disturbance for each of the oil shale cells (Brandt, 2008).
The second stage consists of constructing a freeze Wall. A ring of wells is constructed around the oil shale resource. During the construction and drilling process, a refrigerant is passed to create an internal wall that is vertically positioned around the structure. The wall of the refrigerant is gradually increased to a thickness of 3.1 meters and gradually allowed to stabilize. That allows more wells to be drilled further.
It is important to maintain the freeze wall through the project life, and is estimated to last up to 6.5 years. Each of the recovery cells is isolated by the freeze walls with respect to the permeable layers. These measures ensure that liquid hydrocarbons that are released in the oil shale recovery process ensure that no gases or liquids escape from the cell. In addition to that, no ground water seeps into the cell structure (Brandt, 2008).
The next step is a water removal stage. The process involves filling all the porous parts with water before starting the dewatering process. After the porous rock has been filled with water, mobile water is consequently removed by drilling the middle part of the cell to allow for drainage to occur. At this stage, it is important to remove as much water from the cell as possible because of the difference in the specific heat capacity of water and oil shale. As little water as possible should be left to form the bulk of the raw shale material to enhance the efficiency of the system and recovery process leading to the next process (Brandt, 2008).
Heating forms the next step in the recovery process. Heat supply comes from electric heaters inserted into wells closely drilled into the shale formation. Sufficient space between the wells is provided to allow for an efficient heat transfer within the shale formations. Each of the oil shale formations gets quickly heated due to the arrangements. However, this arrangement appreciates the construction costs of the wells. It is therefore possible for the oil shale to reach up to 500 ºC. The heat supply rate is a parameter that can be varied with respect to varying heat requirements. In addition to that, the efficiency of the recovery process is influenced by the rate of heat transfer to the oil shale.
However, it has been demonstrated that a slow rate of heat transfer enhances the efficiency of the recovery process. It is important to note that the recovery of kerogens is more pronounced at 300 degrees centigrade at a rate of 3 degree centigrade per month to allow for a complete conversion. However, it has been demonstrated in practice that an increase of 3 ºC per day allows for the modification to be achieved at 350 ºC. However, different technologies emphasize on different conversion rates and ultimate conversion periods (Brandt, 2008).
When using the ICP to achieve the conversion of the kerogens to liquid hydrocarbons, elevated pressures form one of the critical components of the process. The difference in pressure between the waste product release pressures and vapor pressure due to the liquid hydrocarbons forms the source pressure for the conversion process. These pressure differences are compensated for by a drop in pressure in the oil wells. However, specific pressures range ahs to be maintained to minimize the possibility of the oil well fracturing. In theory and practice, it has been shown that a pressure difference of ∼0.2 MPa is most appropriate (Brandt, 2008).
Under these operating conditions, assumed to be ideal, heat losses to the overburden are in practice quite minimal. Different models have registered varied pressure differences and operating temperatures. Typical of these changes are shell models which register a temperature of 17 ºC when a level equivalent to 16 m is achieved. It is also important to consider the heat distributions outside of the parameters of the well supplied with heat. Some of the heat is captured and used for the conversion to kerogens while the rest is wasted. This point acts as a precursor to the next stage in the recovery process (Brandt, 2008).
The next phase involves evaluating and putting the recoverable oil in place. Different recovery conditions lead to different yields in the recovery process. At low temperatures and low retorting rates, oil yields are usually low. On the other hand, when high pressures are variably factored into the recovery process, typical yields are equally low. Different companies have registered varied amounts of oil yields based each company’s retorting technology (Brandt, 2008). The following figure illustrates a typical temperature profile of the conversion process discussed above.
The production phase is the next step in the conversion process. This phase characteristically involves cracking of the hydrocarbon chains that form the liquid molecules of the resulting hydrocarbon. At this point, standard hydrocarbon production techniques are used to convert the solid hydrocarbons into liquids for transportation into the surface. That step allows for the restoration and remediation process to set in as the next phase (Brandt, 2008).
In the restoration and remediation phase, flushing of the oil shale with water is done to recover residual hydrocarbons left behind during other phases of the recovery process. It has been demonstrated by Shell that the use of 20 pore volumes of water for flushing reduces the contaminants to a minimal level during the recovery process. At this point, the frozen wall is allowed to reduce into its constituent component, water. That allows for the next upgrading and refining phase. It is important, at this point, to desalinate and remove any vapor pressure that may characterize the recovered hydrocarbon.
The products are chemically modified for use in industry and other uses as combustible fuels. Reported findings indicate a high concentration ratio of H: C ratio of ∼1.9:1. This phase consumes less hydrogen than a typical crude processing approach. All the development phases are examined here. Typical input and output estimates can be done, different intensities of energy inputs, and corresponding oil and gas outputs. Typically, low and high input values are factored into the investigation. The lifecycle recovery process consists of the following assessment steps (Brandt, 2008).
Construction of the freeze wall
Each of the cells is scaled to a commercial size incorporating a casing temperature of -40 ºC. The resulting temperature is assumed to be appropriate for a stable wall. The temperature and pressure profiles are illustrated above.
The resulting profile indicates the energy transfer and movement within the cell walls. When the construction of the freezer wall is completed, effective heat removal is achieved in the complete lifetime of the cell under a steady state model. Typically, the energy transfer between the walls assumes an average value of the axis temperature of the setting. Calculations indicate that the amount of energy requirements to maintain the freeze significantly surpasses energy requirements to achieve the initial freezing (Brandt, 2008).
Heating
The next level in the recovery process is heating. Heating is steadily applied to allow the bulk of the raw oil shale matter to reach the shale decomposition temperature. Once the conversion temperature has been reached, further heat transfer is blocked and further application of heat ceases. The production of oil is a first order reaction under a nonisothermal model. During the conversions process, the shale undergoes a uniform change in temperature for a given unit time. Different models register different oil yield temperatures. Based on the Campbell model, the appropriate temperature for hydrocarbon yields is 330 ºC.
However, the model assumes that pressure does not adversely affect the hydrocarbon yields in the conversion process. Other models are based on the complex decomposition of kerogens that emphasize on the penalties due to pressure variations, allowing for an appropriate application of the Campbell model to explain the conversion process (Brandt, 2008).
It is important to recognize the fact that heat sources to meet heat requirements in the conversion process is based on the enthalpy of retorting projected to be equivalent to 414 and 446 MJ/. An analytical detail of the lifecycle process is tabulated in the table below.
In the mathematical estimates, the heat transfers due to the underburden and overburden are variations that are influenced by the temperature of the oil shale a vital parameter. Typically, the temperature transfer is likely to incur losses due to the porosity of the unretorted shale. In this model, energy losses due to the overburden and underburden contribute to additional energy requirements needed to fulfill the conversion process (Brandt, 2008).
Generation of Electricity
An aggregate of the produced hydrocarbon and natural gas are burned with 45% efficiency in a gas turbine cycle. However, to fulfill the energy requirements in the conversion process, additional heating is provided by electricity generated from an external source. However, external electricity sources are approximated to be 33% efficient (Brandt, 2008).
Recoverable oil shale
To obtain actual estimates of the oil shale deposits, the depth of the deposit and the heated area are multiplied together and the heated area is expands in each direction by 3 m. The heat transfer in different directions at the latter transmission rate is to accommodate additional energy requirements for the recovery process.
A study of practical observations of the development methods conducted to inform the study was the Island method.
The Island method is a partial excavation method typical of the in-situ recovery approach that is structurally characterized by supporting walls which are put in place after the initial recovery wall has been constructed. Practical applications of the method are in large scale excavations sites. Descriptive of the approach is its central location during the construction process allowing surrounding areas to be excavated with a resulting frame created used to offer support to the walls of the created structure (Brandt, 2008).
Development methods views
Individual point of views about the development of oil shale resources can only be informed by making observations about practically established approaches to development. Typically, In-Situ development methods by far have attracted much attention and research due to the overall benefits both technically have been realized from the use of the method. Typically, the method has been identified to accommodate different recovery techniques while allowing the technologies to address problems associated with the extraction of oil from oil shale.
Political Point of View
Different countries have expressed and implied different political positions in relation to the development of oil from oil shale. A typical example is the United States. For the US to secure sustainable, secure and reliable sources of fuel for its military, the country needs to invest in the development of oil from oil shale. In addition to that, the West regards the petro dollars earned by the Middle East countries to principally go into supporting terrorism activities. However, if oil shale is developed and becomes a sustained supply of oil, the support for terrorists will wane, reducing the threat from terrorists. However, other countries like China need to develop oil shale for a sustained supply of oil to meet the exponential demand for oil.
Prospects for development
Economic and energy supply benefits of oil shale development
Research into the development of oil shale reveals that significant amounts of liquid hydrocarbons and gas have been produced to reinforce the rationale for future developments of oil shale. According to studies by Holmes, Boss, Datcher and Heming (1978), it is projected that the recovery of combustible hydrocarbons from oil shale is estimated to replace 16% of the imported oil in the US. Further research on the prospects indicates further development however points out that the difficulty of estimating the overall impact on world oil prices. A typical example that informs the study is based on the US as a case study as discussed below.
In the US
A number of countries have been keen in identifying the rationale of developing oil shale fields to extract hydrocarbons for domestic, chemical, and industrial use. That has been reinforced by the ever increasing demand for energy, exponential rise in prices, political instabilities of countries with crude petroleum deposits such as the political revolutions currently evident in these countries, environmental challenges such as the effects of global warming and waste disposal, and long term maintenance of the quality of water (Andrews, 2008).
The prospects for oil shale development are driven by the prospects and policies of prospecting countries. Each of the countries has different policies specific to the infrastructure for the recovery of the oil shale and the associated technology, safety issues and the relationship with the environment (Bartis, LaTourrette, Dixon, Peterson & Cecchine, 2005). One of the countries that have made strides in the recovery and development of oil shale in the United States as detailed below.
One of the driving forces behind oil shale development in the US is the strategic significance associated with its exploitation and development. Typically, a marked contribution to the US government’s goals, both domestically and abroad, adds the impetus to the role of the government in the exploitation and development of oil shale. It is important to consider access to land and other alternative land uses as an additional role of the government in the development of oil shale. In addition to that, the government will have to incur expenditure for permitting land leases and in putting in place the requisite infrastructure for the oil shale development (Bartis, LaTourrette, Dixon, Peterson & Cecchine, 2005).
It has been projected that under a competitive operating environment, the recovery of oil shale without any government subsidy could be economically beneficial on several fronts. Typical of the benefits include gains by the government in the form of taxes. Additional benefits include royalty payments to the government, the creation of new jobs in the oil shale recovery industry and associated benefits resulting from the supply chain of inputs into the oil shale industry. Though the net effect of shifting from other industries into the whole oil shale chain cannot be determined with precision, yet projected shifts could cushion any adverse effects likely to be caused by the entry of oil shale into the energy supply sector (Bartis, LaTourrette, Dixon, Peterson & Cecchine, 2005).
It is projected that the consumer will ultimately benefit from reduced oil prices both in the domestic and in the world market upon the entry of oil shale products into the energy sector and related industries. That reinforces the rationale for government support in the mining and processing of oil shale as a substitute source of hydrocarbons. It is projected that the production of hydrocarbons from oil shale is bound to reduce trade deficits besides providing the US military with a reliable and secure source of fuel.
Calculations based on estimated production of 3 million barrels of oil per day are projected to provide up to one billion barrels a year. These calculations and projections are based on a 30 year timeline and estimated future and, infact, current oil prices per barrel. That is in comparison with the cost incurred in importing crude oil from other countries (Bartis, LaTourrette, Dixon, Peterson & Cecchine, 2005).
Other economic benefits likely to influence the projected return on invested the capital. The economic feasibility of investing in the industry is further accelerated by the projected revenue, of up to $ 50 billion that can be distributed among industry investor, the supply chain and base support services and support infrastructure, employees in the oil shale industry, and gains to the government in the form of levied taxes.
Projections have it that, if the production remains at 3 million barrels per day, the aggregate effect will be a $20,000 billion generation of economic profits above the expenses incurred on the capital investments and other industry expenditure. That is in addition to loyalties and other bonus payments, half of the projected profits of 20,000 billion $ ends in government hands, gradually benefiting the public. Typically, benefits due to resource depletion, environmental damages due to the permanent destruction of land to the land owner are of the challenges that influence the benefits to land owners for adequate compensation (Bartis, LaTourrette, Dixon, Peterson & Cecchine, 2005).
Other benefits include an impact on the employment of well trained and qualified personnel in addition to significant productivity gains experienced in the coming years. It is estimated that up to 50,000 people will find employment in the oil shale industry when the mining and recovery of liquid hydrocarbons assumes a commercial operational scale.
However, it is important to note that the mining and processing will have to attract significant infrastructure and capital investments. Typical of surface retort mining technology, several workers, in this case of up to 70,000 employees will find direct employment. Further projections on an increase in employment levels will result from the ripple effects caused by re-spending effects, supplier effects, and employment offers by the government. The supplier effects are projected to create employment in industries that manufacture equipments used in the mining and recovery of oil from oil shale. In addition to that, support services associated with the construction of oil shale plants are additional benefits that come with the construction of oil shale plants (Bartis, LaTourrette, Dixon, Peterson & Cecchine, 2005).
It is also worth noting that jobs are projected to be created in other industries due to the revenue generation when employees spend their earnings. However, macroeconomic factors significantly influence the level of employment and unemployment levels. It is important to note that, these effects significantly influence the monetary policy of the federal government of the US and the reaction rates from other parts of the economy (Holmes, Boss, Datcher & Heming, 1978).
Oil producing regimes embrace policies that are in stark violation of human rights and suppression of the pursuit for democracy. More earnings from crude oil producing countries perpetuate their human aggrandizing policies from the earnings of exporting petroleum products. This is evident from the riots that have engulfed the Middle East oil producing countries and other African countries particularly Libya in the quest for democracy.
Another benefit projected to be gained by the US government is a reliable resource of fuel for the US military. In addition to the reliability of the oil shale as a source for the much in demand hydrocarbons, countries that do not embrace democracy and other human rights will find a narrow market and thinning out revenue from the export of petroleum products and related hydrocarbons. Typically, the internal politics of a country are overly influenced by the revenue generated from the export of oil by oil producing countries (Bartis, LaTourrette, Dixon, Peterson & Cecchine, 2005).
Researches on the effects of petrodollars on the political views held by oil producing countries against the US are bound to reduce if the authoritarian oil producing regimes receive less money from the sale of their products. Thus, anti-American sentiments are bound to reduce.
Strong arguments in favor of the development of oil shale as a source of oil for domestic, chemical, industrial, and military have been in the offing. Typically, it has been argued that if the US government does not reduce the kind of trade deficits experienced in the recent past, there is the possibility that its economy can be easily destabilized by its political foes. That is further impelled by the fact that trade deficits shift American assets into foreign hands with political objectives in direct conflict with US policies. That allows foreign interests to dominate the US economy making it susceptible to foreign manipulation.
On the other hand, opponents of the economic projections of producing oil from oil shale on the trade deficits of the US argue to the contrary. They argue that injecting funds and investment into the production of hydrocarbon liquids from oil shale does not stimulate real economic growth by creating wealth for the nation. They argue that investments that create national wealth by far outweigh the benefits derived from investing in oil shale developments.
On the other hand, the US government finds the policies geared towards increasing domestic production of oil from oil shale to allow for a reduction on the overdependence on imported oil (Bartis, LaTourrette, Dixon, Peterson & Cecchine, 2005).
That is projected to reduce the risks associated with sending US troop into foreign soils particularly into Persian Gulf countries. In addition to that, it minimizes the susceptibility of the government to national security risks. In addition to that, the policy of investing in domestic oil shale exploitation is projected to increase the domestic supply of oil and lead to a big increase in the conservation of energy.
Another argument in favor of domestic oil production strategies from oil shale deposits includes the reliability for oil for the US military. However, it is sanguine to argue that some oil producing countries of the world are friendly to the US, assuring of a sustained and reliable supply in the event of a confrontation. Notwithstanding, it is also important to note that a likelihood of such a friendly source getting disrupted in the event of a war of military confrontation can affect the supply chain and consequently, the resulting prices. In addition to that, the possibility of a willing seller willing buyer strategy prevailing in the oil market, yet the US military needs to rely more on domestic oil resources than the oil floated for sale in the world market. That is mainly due to the risks associated with procuring oil for the military from the international market (Bartis, LaTourrette, Dixon, Peterson & Cecchine, 2005).
In conclusion, therefore, it is worth the argument that the investment on oil shale production comes with a host of benefits to the investor, the domestic market, and other industry consumers. Direct economic benefits from the production of liquid hydrocarbons from oil shale can be realized from cost effective production technologies. In addition to that, it is worth realizing that investing in the production of oil from oil shale is projected to cause higher employment levels, higher government revenue from taxation, and a chain of economic benefits due to support industries and services in the production of oil shale (Bartis, LaTourrette, Dixon, Peterson & Cecchine, 2005).
On the other hand, a number of security benefits are expected to be realized by both the US government and the military. That could be reinforced by the sustainable supply of fuel for the US military and industries that consume liquid hydrocarbons. In addition to that, access to, and development of federal land are also some of the associated benefits derived from oil shale development (Holmes, Boss, Datcher & Heming, 1978).
As a political development, it is important to examine in detail critical policy issues that have to be bone in the development of oil shale in the US.
Policy issues
Among the potential areas influencing the policy formulations with respect to the mining and development of oil shale in the western world include social and environmental issues. During the development of oil shale, a number of environmental issues that directly bear a social impact on the areas under development need to be addressed through appropriately formulated policies. Social issues are propelled by the quest for the usage of land in and the resulting impact of the usage on the affected communities, the effect on the air and water quality, and the effect on the ecological setting of the area under development. It is the approach that the government’s policy makers use to address these issues that reinforce the support for the development project to go forward (Holmes, Boss, Datcher & Heming, 1978).
One of the challenges that the government policy makers have to contend with is land use and the degree to which land can be disturbed in development of the oil shale. A typical example can be drawn from discussions elsewhere on land use, in particular, the Green River oil shale formation. An assessment of land use within this region reveals a number of activities which include recreational activities, the rearing of sheep and cattle, fishing purposes and to a significant extent for hunting, and to a large extent for oil shale drilling and processing. On the other hand, a number of habitats are prevalent in this region and policies need to be formulated to address the land take issues. Other issues of major concern include air and water quality as mentioned elsewhere, opportunities for action in the development of oil shale, and air quality challenges (Holmes, Boss, Datcher & Heming, 1978).
The prevalence of oil shale deposits through the world is very high. Therefore, a number of issues and opportunities influence to a large extent prospects for oil shale development as discussed below.
Other prospects for development
The development of oil shale takes various dimensions if ever the aim is to achieve commercial quantities. In addition to that, the world oil prices, the political scene and the instability of oil producing countries are other considerations to be bone in mind when endeavoring to bring to reality any prospects for future developments. It is important to consider the prospects of alleviating the energy supply of oil shale mining countries in a comparatively cost effective way. In addition to that, the ability to optimize benefits and minimize the risks associated with commercial scale productions, an appropriate financial mix for optimal levels of productions, and major obstacles to the commercialization of the production of oil from oil shale.
It is therefore of critical importance to make informed decision about the best option to settle on when making an entry into the commercial production of oil from oil shale. Typical of the necessary variables to consider in the investment portfolio includes the capital requirements to meet the production of oil shale at different operational levels, associated risks and corporate regard for associated risks, cost effective incentives and subsidies, and projected costs that may be required in the short term to keep an industry afloat (Holmes, Boss, Datcher & Heming, 1978).
Research findings with respect to the prospects of investing in the oil shale industry demonstrate a number of facts and issues that have caused stagnation in growth in the oil shale industry. Large capital costs impede to a significant extent investment in the industry, regulations and controlled access to federal land, inability to model future oil prices due to unpredictable oil price fluctuations, and environmental regulations and policies by designate governments.
The economic rationale, as mentioned and discussed on the American model elsewhere includes the creation of employment, reliable oil supply, attraction of capital and financial investments, and a range of other benefits. However, to achieve the economic benefits and other associated benefits, it is important to consider the development of various oil shale technologies, to investigate the commercialization of the technologies, and typical approaches to cost effectively deploy the technology.
A clear understanding of the actual meaning of commercialization is vital in crystallizing various issues in the discussion. Commercialization is a process by “which private industry adopts a technology for commercial use after most of the technical uncertainties affecting its economic feasibility have been resolved” (Holmes, Boss, Datcher & Heming, 1978). Different countries have different approaches for implementing commercialization programs of oil shale production. A typical example is the US. In the US, commercialization is the responsibility of private firms without any intervention from the federal government.
However due to the dynamic political environment and other intervention measures, direct government involvement has experienced a significant rise in the past several years. That has also been driven by the need for the government to stimulate accelerated growth and development in technologies that lead to the development of oil shale into a commercially viable scale. The government plays a critical role in the research and development (R&D) basically aimed at resolving technical problems associated with any specific technology before going into large scale commercial application.
Well known examples of government intervention include a Second World War synthetic rubber program deployed through a government sponsored program that became exceptionally successful against negative prospects. In addition to that, recent trends indicate increased government interventions while the role of private firms has increasingly been minimized to the advertising and operating mining and recovery facilities. However the commercialization pace is currently influenced by the Government which plays a critical role in planning on technology investment in collaboration with the private sector that plays the key role of adopting or rejecting any proposed oil shale recovery technology. However, a close investigation of Government intervention, particularly federal intervention is necessary to crystallize the rationale for the intervention (Holmes, Boss, Datcher & Heming, 1978).
Why Government Intervention
Oil shale exploitation and recovery is an enterprise that has social, political, and environmental ramifications with serious implications on both the government and the private sector. It is important for the government to critically consider the ramifications on the society due to its failure to ensure secure oil and other forms of energy supplies. In addition to that, it is the sole responsibility of the Government to ensure appropriate technologies are used to in the recovery process to ensure minimum effects on the environment, minimal effects on price appreciations, and ensure that the exploitation of oil shale for the production of hydrocarbons comes with a host of desirable social benefits.
Typically, government intervention could ensure the society is cushioned against political and economic events that may unravel to the disadvantage of the society such as a rise in terrorism (Holmes, Boss, Datcher & Heming, 1978).
Active involvement in the industry by the government stimulates interest in the industry by private investors due to the inspired confidence in the ability for the investment to accrue profits. It is important to note that the risk and uncertainties inherent in the oil shale industry are some of the factors that raise the concern for private companies to invest in the industry. Typical of the risks and uncertainties associated with the oil and shale industry include failure to conduct accurate estimates of the operating and capital costs in relation to projected revenue and accruing profits, the probability of the investing company not to recoup the initial investment given the probability of severe price fluctuations, and the probability for an adverse impact on project economics due to government bureaucracy in failure to meet dynamically evolving environmental regulations.
It is important note that Government intervention may stimulate interest or discourage development in new technologies depending on the perspective or approach of the government on the application of penalties on the production of oil from oil shale. It should be noted that Government regulations and policies are critical components in influencing the final take oil shale developments. Typically, it is important to note that Governments should ensure market forces are allowed a free play to allow productive investment economic forces into play (Holmes, Boss, Datcher & Heming, 1978).
Commercial impediments
Any new technology must come with a number of challenges and problems experienced during the development and implementation stage. These problems are typical of the applicability in the commercial scale, operational efficiency, and technical capabilities. In additions that, the rationale of applying a particular technology is strongly correlated to the economic benefits projected to be gained from the use of that technology, the environmental friendliness, and other benefits projected to be derived from its application.
One of the problems associated with the development of oil shale is the technical difficult of scaling demonstration facilities into commercial sized technologies. Typically, a failure to scale up such a technology may lead to financial losses and associated losses. In essence these technologies come with associate problems specific to their functionalities. A number of technologies discussed above include in situ technology and underground technologies (Holmes, Boss, Datcher & Heming, 1978).
Cost of oil shale facilities
The cost of oil shale facilities varies significantly from one estimating agency to another. In particular, there are no oil shale facilities that are readily manufactured for sale, but are developed by interested companies in the recovery of oil shale. In addition to that, oil shale facilities cannot be compared with already existing crude oil refining facilities as common processes such as hydrotreating are few. However, some oil shale facilities are projected to come at significant low costs such as the Shell’s ICP technology. However, being an energy intensive technology, the ultimate cost appreciates significantly (Andrews, 2006).
What are the Economic & Energy Supply Benefits of Oil Shale
Economic Benefits
Governments and energy firms in the world have projected various economic and energy supply benefits as the force behind the large investments in the development of oil shale. Projections on economic benefits at different levels are modeled on production forecasts to provide an analysis of the cumulative gains in the short and long terms. However, it is important to note that the economic benefits cannot be generalized but specific to the technology used in the recovery process and other variables.
The potential for economic benefits can be argued from an economic model based on accumulative data for 30 years as illustrated below (Carolus, Crawford & Mohan, n.d). The tabulation shows that, alone in the United States, the revenue generated to the Federal treasury from oil shale is bound to hit a $48 billion mark as direct revenue. In addition to the revenue benefits, the contribution to the GDP is estimated to reach $ 1.3 trillion.
The benefits are bound to translate into $ 325 billion worth of avoided imports for the 30 years projected period. It is also estimated that 300,000 jobs will be created with the use of low cost oil production technologies. Typically, the public is bound to benefit indirectly through lease bonus payments, corporate income tax, and royalties (Carolus, Crawford & Mohan, n.d).
As mentioned above, employment benefits are bound not only to remain concentrated in regions producing oil shale, but also attract expert personnel with highly paying jobs. Additional benefits are bound to result indirectly to industries that provide inputs to the production process (Carolus, Crawford & Mohan, n.d). However, statists on the benefits of employment may cause a reduction from other sectors, hence is difficult to accurately project.
In the domestic front, if the production costs cover costs on the return on capital and if the costs are lower cost than prevailing market prices, the oil shale will be a potentially competitive source of combustible hydrocarbons and gas. Economic model estimates indicate that the economic benefits will outdo prevailing benefits when relying on imported crude oil as a source of energy.
Another economic benefit likely to result from oil shale production is a reduction in world oil prices. Typically, it is projected that if the production quantities of combustible hydrocarbons appreciate significantly, it is likely to tip the balance in demand for crude oil eventually triggering a drop in global oil prices.
The above economic projections apply to a significant extent on the US economy. However, many countries have heavily invested in the mining and recovery of combustible oil and gas from oil shale with projected economic benefits similar to the American model. That is largely because oil shale deposits have been discovered to be in abundance and of commercial value in many parts of the world.
Energy Supply Benefits of Oil Shale
A sustained supply of energy could potentially impact on the certainty of the hydrocarbon and gas market in the world today. Different countries see the recovery of combustible hydrocarbons and gas from oil shale as a sustainably stable supply of energy available domestically. That is particularly due to large tracts of land under oil shale with the potential for commercialized exploitation (Bartis, LaTourrette, Dixon, Peterson & Cecchine, 2005).
Cost of oil shale facilities
The cost f oil shale facilities vary with the technology under consideration. It is also worth noting that different companies have taken an in-house approach of developing, testing, and deploying their technologies. That limits the availability of the technologies in the market (Holmes, Boss, Datcher & Heming, 1978).
Refinery processes
Small pilot studies have been conducted to study different approaches to the refinery process for oil shale. Further studies have been conducted with several computer simulations done to provide additional data on the efficiency of different refining approaches. These processes include catalytic, thermal, and additive refinery methods. Thermal refinery processes are characterized by coking which is a severe treatment of the raw shale or a relatively mild thermal process. The mild thermal process reduces the pour point of the resulting oil. On the other hand, severe thermal treatments lower to a significant extent the pour property of the resulting oil. Typically, the viscosity characteristics also reduce significantly under the extreme thermal treatment conditions (Holmes, Boss, Datcher & Heming, 1978).
The catalytic process demands the application of hydrogen as a catalyst. The viscous properties of the resulting oil are reduce to a significant extent. Additional benefits typical of the catalytic process are the formation of ammonia.
On the other hand, mild thermal treatment causes the sulfur and other elements to be maintained while the viscosity and pout point reduces significantly.
During the catalytic refinery process, additional blending of chemicals is added to enhance the production process. It is therefore important to briefly discuss about these chemical processes (Holmes, Boss, Datcher & Heming, 1978).
Visbreaking
Typically, the technique involves exposing the crude oil shale to temperatures of 900 F and maintaining a steady state of the temperature before cooling commences. The resulting liquids and gases are recovered. The average content of oxygen, nitrogen, and sulfur remain undisturbed. Though the technique reduces the pout point of crude shale oil to 400 F, it is energy intensive makes it a disadvantage to using (Holmes, Boss, Datcher & Heming, 1978).
Catalytic Hydrogenation
A catalytic reaction of hydrogen and oil shale leads to the production of hydrogen sulfide and additional molecular chains of atoms. Typical chemical substances produced from these reactions are of highest quality though disadvantaged by high costs. It is important to evaluate the refining properties of refinery systems that influence their design. Typically, these are characterized by total refining processes.
Total refining processes
Typical defining characteristics which parametrically determine the design of refinery equipment include the ratio of the constituent substances in the final product and the practical limitations imposed by the technologies of the facility. However, the first requirement has no significant variations with conventional petroleum processing facilities. On the other hand, the second requirement is dictated by technological innovations and refinery configurations (Holmes, Boss, Datcher & Heming, 1978).
The economic desirability of an oil shale refining facility could demand thorough investigations coupled with computer simulations, a detailed investigation of the amount of oil shale deposits to guarantee sustained supply of the raw material, and an evaluation of existing facilities to offset the costs and risks associated with setting up new facilities. The parametric units of refining oil shale include catalytic cracking, reforming, coking which includes hydrotreating, hydrocracking, and distillations.
Different refining schemes have been developed with time. However, these configurations significantly differ from one another particularly in the arrangement of the thermal catalyzing elements. One of the approaches is where the whole components of the catalytic process are obtained from the whole raw shale product and a distillate of the catalytically processes raw shale is obtained (Brandt, 2008).
One advantage with the first approach is that the eventual properties of the resulting end product can be controlled. On the other hand, the second approach allows for the production of high quality hydrocarbons. Schematic views of the refinery techniques are illustrated below.
Is oil shale competitive?
Oil shale as a competitive resource for the production of combustible hydrocarbons and gas cannot be disputed. The rationale for oil shale as a competitive resource is evident from the immense resources companies have invested in the mining of oil shale as a resource for hydrocarbons adds weight to the competitiveness. As discussed elsewhere, typical examples abound of companies which have invested in oil shale recovery technologies. In the US, over 20 in the US with various proven and tested technologies have already invested in various tested and proven technologies as being efficient and economically feasible (Holmes, Boss, Datcher & Heming, 1978).
What are economic negative effects of establishing the industry
Establishing an oil shale industry comes with negative social and economic effects. Typical of the negative economic benefits effects are the trail of benefits and jobs importers and personnel in the crude oil industry will suffer. If the oil shale industry gains momentum to overtake the importation of crude oil from oil exporting countries, the loss in jobs, social services that were offered by crude oil importing countries as part of their social corporate responsibility, and benefits will be adversarial in the short and long term.
What are the water needs for oil shale industry?
The production and recovery of oil shale to obtain the final hydrocarbon come with associated water needs that have to be addressed. However, the water requirements for the production process vary with the kind of technology under consideration (Carolus, Crawford & Mohan, n.d). Practical and theoretical generalized estimates indicate that an equivalent of 3 barrels of water is needed for each barrel of oil shale.
Typically, the water requirements are specific for each retorting technologies. However, other technologies have been proven to be net producers of water during the oil shale recovery process. A typical oil shale production facility working at a capacity of 2.5 MMBbl/d requires an equivalent of 315 million gallons of water daily. The calculated estimates translate to 0.42 acre feet with variations depending on the technology is used, the location, and the recovery and processing technique in use.
A typical case is the mining of oil shale in the Colorado basin. The Colorado oil shale deposits have been evaluated and found to contain very high water content in comparison with other deposits elsewhere. Generally, oil shale deposits contain an average of 2.5 gallons of water per ton. The Colorado deposits contain an average of 35 gallons of water per ton. Much of the water can be recovered and reused to support the mining and other reclamation activities during the mining of oil shale. By incorporating the water refining technologies, the connate water can be refined to remove dissolved organic and inorganic substances.
A key advantage of mines with high water contents is that the water can be reclaimed for use reducing water requirements further. In addition to that, support activities can be sources of water for the reclamation process (Carolus, Crawford & Mohan, n.d).
Additional costs on water result if the refining of oil shale occurs locally. In addition to that, indirect water requirements could add to the additional water requirements to be met (Gavrilova, Randla, Vallner, Strandberg & Vilu, 2005). Additional water requirements are tabulated in the fig. below.
The above tabulations indicate water processing requirements for specific mining technologies as mentioned above (Brown, 2008). However, different authors provide different details for water requirements as illustrated in the fig. below.
However, both figures illustrated the need for water from the mining and other oil shale recovery processes. The estimates vary to a significant extent. However, the order of magnitude for the oil shale water requirements assumes a similar trend for both estimates. Analogically, therefore, the amount of surface water available for the recovery process has to reduce with time in both quality and quantity, with a similar trend significant for ground water notable (Gavrilova, Randla, Vallner, Strandberg & Vilu, 2005).
A theoretical and practical evaluation of ground water has to be conducted to determine typical approaches to the water management as analytically provided below. Each of the water following provides a framework for the deposits of water and the main characteristics of the ground water are provided (Gavrilova, Randla, Vallner, Strandberg & Vilu, 2005).
In addition to that above estimates and information, it is also important to address the predevelopment water budget as illustrated below (Gavrilova, Randla, Vallner, Strandberg & Vilu, 2005).
Will the cost of obtaining water limit the size of the oil shale industry, what’s the environmental impact of needing that much water (developing water resources)
According to the water rights in the United States, the process of mining can be impeded if to a significant extent if no local supplies of water occur in the designate mining area. Water has overly limited a full venture into the mining of oil shale in the past years.
Ways to Not Destroy the Environment When Starting this Industry
Oil shale production will entail disturbing the oil shale depositional land (Brown, 2008). Typically, the mining process leads to the surface disturbance of large tracts of land either when making direct recoveries or drilling wells for in-situ recovery process.
No technology can be used without causing disturbance on the environment and other environmental resources. That is typically because of the use of additional surface facilities such as water pipes, storage facilities particularly for materials proven to be hazardous to the environment.
All mining and extraction process for oil shale requires certain amounts of water and additional variables such as air and external energy sources. The mining process has the potential to attract additional requirements on the local infrastructure and landscape. If the oil shale deposits are large and attract a large number of companies into a same region, pressure on the social infrastructure will be an additional effect. In addition to that, there will be pressure for the expansion of the local infrastructure to meet the requisite demand for infrastructure.
Mitigations
However, there is need to ensure the environment is overly protected from the destructive effects mentioned above. One such strategy is for a regulatory framework that controls access to water and land resources as is typical of the United States. In the United States, as a cases study, regulations have been signed into various laws such as the Public Law 109-58. The law regulates commercial leasing programs of oil shale deposits under the national environmental policy guidelines.
On the technological aspects, different companies have to expose their mining and refining technologies to rigorous tests to evaluate their compliance with established legal compliance standards and requirements. Different countries have different standards that companies have to evaluate their technologies against.
A typical regulatory body is the department concerned with the reclamation of land and Natural resource. The department is overly responsible for water quality control where discharge from areas where mining takes place must meet certain requirements. In addition to that, surface water requirements have to be met as an additional water quality control measure.
As a further measure to protect water, water being the principal element in regulating the environment, infiltration rates have to be controlled and appropriate continuous monitoring below.
Is it worth developing with all the negative effects?
Despite the negative effects of developing oil shale, projected benefits such as a sustainable and secure source of combustible liquid hydrocarbons, gas, and byproducts reinforce the rationale of developing oil shale. Typically, the rising cost of oil from petroleum products, political instabilities of petroleum holding countries, unstable global oil prices, and adverse effects on global economies add to the impetus for the research and development of oil shale.
On the other hand, legislation, new technologies which address the problems and issues such as water treatment, improved oil shale waste disposal mechanisms, and limited amounts of water needed for use with new technologies have further reinforced the rationale for investing in the development of oil shale. Despite the hopeful projections in the development of oil shale to extract combustible fuel and gas, governments and companies need to make further investments research and development particularly for new technologies that are more water efficient and with better oil recoveries. In addition to that, the technologies need to be cheaper.
References
Andrews, A. 2008. Developments in Oil Shale. CRS Report for Congress. New York: Andrew.
Andrews, A. 2006. Oil Shale: History, Incentives, and Policy. CRS Report for Congress. Congressional Research Service. New York: The Library of Congress.
Bartis, J. T., LaTourrette, T., Dixon, L., Peterson, D.J. & Cecchine, G. 2005. Infrastructure, Safety, and Environment. Oil shale development in the United States Prospects and Policy Issues.
Brandt, A.R. 2008. Converting Oil Shale to Liquid Fuels: Energy Inputs and Greenhouse Gas Emissions of the Shell in Situ Conversion Process. California. Berkeley: University of California.
Brendow. K. 2003. Global Oil Shale Issues And Perspectives Synthesis Of The Symposium On Oil Shale Held In Tallinn (Estonia). World Energy Council. 20 (1), pp 81-92. Geneva: Estonian Academy Publishers.
Boak, J.2007. CO2 Release from In-Situ Production of shale oil from the Green River On the western United States. Colorado: Colorado School of Mine.
Brown, E. G. 2008. Comments on the Oil Shale and Tar Sands Leasing Draft Programmatic Environmental Impact Statement. Argonne National Laboratory. Argonne IL 60439.
Chaohe, F., Dewen, Z. & Dexun, L. 2008. BMain Problems in development and Utilization of oil shale and status of the In-Situ Conversion process Technology in China.Colorado School of Mines, Colorado. New York: Sterling Publishing Co Inc.
Carolus, M., Crawford, P., Mohan, H. n.d. Economics, Barriers, and Risks of Oil Shale Development in the United States. New York: Soho Publishing.
Chan, M., Duda, J., Forbes, S., Rodosta, T., Vagnetti, R. & McIlvried, H. 2006. Emerging Issues for Fossil Energy and Water. Investigation of Water Issues Related to Coal Mining, Coal to Liquids, Oil Shale, and Carbon Capture and Sequestration. New York: Sterling Publishing Co Inc.
Clough, G. W. & O‟Rourke, T.D., 1990. Construction Induced Movements of In-situ Walls. Proc., ASCE Conf. on Des. And Perf. of Earth Retaining Struct., Geotech. Spec. Publ. No. 25, ASCE, New York, 439-470.
Crawford, P. M. 2007. Overview of Emerging Oil Shale Technologies. The Colorado Energy Research Institute and the Colorado School of Mines.
Crawford, P. M. 2007. Secure Fuels from Domestic Resources the Continuing Evolution of America’s Oil Shale and Tar Sands Industries. Profiles of Companies Investing Today to Secure America’s Energy Future.New York: HarperCollins.
Crawford, P., 2008. INTEK Inc., Advances in World Oil Shale Production, Presented at the 2008 Society of Petroleum Engineers Annual Technical Conference and Expo September 22nd, 2008. Denver, Colorado.
Dyni, J.R., 2006. Geology and resources of some world oil-shale deposits: U.S. Geological Survey Scientific Investigations Report 2005–5294. Web.
Ergun, M. U. n.d. Deep Excavations. Department of Civil Engineering. Ankara: Middle East Technical University.
Gardiner, D. & Sanzillo, T. 2010. Investor risks from Development of oil shale and Coal-to-liquid. Web.
Gavrilova, O., Randla T., Vallner, L., Strandberg, M., Vilu R., 2005. Life cycle analysis of the Estonian oil shale industry. Project: Institute of Chemistry, Tallinn University of Technology, Institute of Geology, Tallinn University of Technology, Estonian Fund for Nature. 11. 145..
Gonza´lez-Vila, F.J., Ambles, A., Rı´o, J.C. & Grasset, L. 2000. Characterisation and differentiation of kerogens by pyrolytic and chemical degradation techniques. Journal of Analytical and Applied Pyrolysis 58–59, 315–328.
Hettelingh, J-P, Posch, M., Slootweg, J., 2004. Critical loads and dynamic modeling results. CCE Progress Report 2004, Coordination Center for Effects, RIVM Report 259101014, Bilthoven, Netherlands, 134.
Holmes, J.C., Boss, S. K., Datcher, D. M. & Heming, J. 1978. An Assessment of Oil Shale Technologies. Washington: U.S. Government Printing Office.
Jeong, K.M. & Patzer, J.F. 1983. Indigenous Mineral Matter Effects In Pyrolysis Of Green River Oil Shale. Gulf Research & Development Company. Piasburgh: Wnnsyivada.
Kleinberg, R. 2007. Oil Shales. Working Document of the NPC Global Oil & Gas Study. New York: HarperCollins.
Lille, U. 2003. Current Knowledge on the Origin and Structure of Estonian Kukersite Kerogen. Brisbane: Estonian Academy Publishers. Oil Shale, 20 (3), pp. 253-263.
Miller, G.A. 2007. Some Perspectives of various methods of oil shale extraction Piceance basin Colorado. Colorado School of Mines Golden, Colorado: Colorado School of Mines Golden.
Nikitin, O. & Sabanov, S., 2005. Immediate roof stability analysis for new room-and-pillar mining technology in “Estonia” mine. Proceedings of the 5th international scientific and practical conference. 262-269.
Pastarus J.-R. & Sabanov S. 2005. A method for monitoring working mining block stability in Estonian oil shale mines. Proceedings of the Estonian Academy of science. Engineering journal: 59-68.
Rubenson, D. & Pei, R. 1983. Oil Shale in the Piceance Basin. An Analysis of Land Use Issues. Web.
Sabanov, S & Pastarus, J.R., 2006. Environmental Impact Assessment for Estonian Oil Shale Mining Systems. Tallinn University of Technology, Department of Mining. Tallinn: Estonian Academy Publishers.
Schmidt, S. J., 2003. New Directions for Shale Oil: Path To A Secure New Oil Supply Well Into This Century. Brisbane: Estonian Academic Publishers. 20 (3), pp. 333-346.
Smith, J.W., 1983. The Chemistry Which Created Green River Formation Oil Shale. Symposium On Geochemistry And Chemistry Of Oil Shale And Petroleum Chemistry, Inc. American Chemical Society Seattle Meeting, Presented Before The Divisions Of Fuel Chemistry, Geochemistry.
Stevens, R. F., Dinneen, G. U., & Ball, J. S., 1952. Analysis of Crude Shale Oil. Report of Investigations 4898. United States Department of the Interior. New York: United States Department of Interior.
Sørlie, J.-E., Bityukova, L., Sæther, O.-M., Rudolph-Lund, K., Kahru, A., Vallner, L., Petersell, V., Razgonjajev, A., Põllumaa, L. 2004. Estonia, the oil shale industry. Risk based environmental site assessment of landfills. Report. 216.
Volkov, E., Gerasimov, G., Ter-Oganesian, G., Samuilov, E. 2010. Investigation of Flash Pyrolysis of Kukersite Oil Shale. Estonian Academy Publishers. 27 (4), pp. 281–296.
Yun-lai,B, Yingcheng,Z, Long, M, Jun, W. W & Yu-hu, M., n.d. Geological Characteristics and Resource potentials of Oil Shale in Ordos Basin, Center China. Lanzhou 730020: Gansu.