Introduction
A project is a short-term activity with a specific start and end date, and it involves change and uncertainty, which increase the risk of failure. Projects should be accomplished on time and per the budget and quality for the manager to succeed. All tasks necessary for the project’s success are targeted, and risk scanning is managed in advance to identify potential difficulties and resolve them before they become a challenge. Consequently, project managers can help with issue solving, alternate viewpoints, sponsor direction, tracking and reporting, and communicating with all parties involved (Gijzel et al., 2019). Many researchers have studied project management; however, only a few studies have uncovered new methods for evaluating sustainability. Financial, natural and social control aspects ensure successful incorporation of sustainability into project management.
Research Question
This research question will be the centre of attention in this study:
- How can sustainability be successfully integrated into project management?
The response will be obtained from the secondary data the researcher will collect and analyse. The following sub-enquiries will serve as support for responding to the research question:
- Which are the factors that promote sustainability in projects?
- How can the choice of project management measures be effectively realised?
- What are the crucial elements of sustainable project business policies?
Aim and Objectives
Aim
This proposal aims to integrate sustainability in project management, an essential profession, to promote a thriving economy and society. Project managers are qualified and have the technical skills necessary to help integrate sustainable and essential initiatives (Thürer et al., 2018). Expert researchers have identified several aspects of sustainability and policies and procedures for selecting various strategies to incorporate feasibility into projects.
Objectives
- To establish how sustainability can be successfully integrated into project management.
- To determine factors promoting sustainability in projects.
- To evaluate how the choice of project management measures can be effectively realised.
- To identify the crucial elements of sustainable project business policies.
Literature Review
Literature on recommendation systems, including how this study fills in the knowledge gap, will be presented in this paper. The study’s topic was selected from current research for the literature review. The unique research questions and objectives will guide the investigation. Using a review of the existing literature, it will be possible to identify a research gap in sustainable project management for practical analysis.
Sustainability in Projects
Research presented by Vrchota et al. (2020) defines sustainability in project management as the formulation, administration and delivery of a project-systematised framework of policies, resources, activities, resources or establishments. Sustainability deliberations are measured in the project’s conclusion and effect (Ahmed, 2019). The six essential sustainability principles in project management include stabilisation or coordination of social, ecological and economic welfare; brief and incessant orientation; local and global exposure; morals and ideals; responsibility and transparency; and spending revenue, not investment. Projects that adhere to high ethical and social standards should be accomplished.
Project management associations have produced codes of ethics and standards of practice that emphasise the importance of ethical standards in plan development. A company’s policies and decisions will impact the environment and society if outlined in a detailed blueprint and valuable plans made for the projects. Policy and process failures should be held against the company (Adams, Martin, and Boom, 2018). Project managers should open up and be proactive in communicating with all partners, including environmental and social impact controllers, to achieve sustainable development (Thacker et al., 2019). This information should be restricted to what is necessary to complete a project.
The inclusion of financial, natural and public variables in managing projects does not permit a comprehensive focus on sustainability for project management. Martens and Carvalho (2017) conducted a factual investigation of Brazilian industry based on triple bottom line parameters. In their research, the authors found that a successful triple bottom line strategy mostly depends on the project’s design and perspective, which may differ from one plan to another (Ciccullo et al., 2018). To assess and connect the probable sustainability in most projects, a gap is investigated as sufficient to produce widely acknowledged sustainability variables.
Choice of Sustainable Project Management Measures
Increasing attention is being paid to the link between sustainable project management and scholarly debate internationally. When it comes to sustainable project management, it can be determined that the project manager’s key position allows them to impact a wide range of components significantly (Adabre and Chan, 2019). Short duration projects have some constraints when introducing sustainability into their successful management. While considering where sustainability fits into the project’s life cycle, it is important to keep in mind the production process and final deliverable stages. Mavi and Standing (2018) advocated that sustainability should be incorporated into every level of the project’s lifecycle. All stakeholders should take into consideration efforts to achieve sustainable project management.
In project management, the iron-triangle approach is often used to identify measures. Time, quality and cost are the three restrictions represented by the iron triangle (Blanco-Portela et al., 2018). Additionally, the stage-gate process assesses a project’s performance based on time, quality, uncertainty and cost. While deciding on project management strategies, it is important to consider sustainability’s environmental and social aspects.
If the project is to succeed, it should be located in a place that can support it for the long term. International economies have recently been quite diplomatic about the losses and profits; therefore, it has become necessary to determine and analyse the regional, national and international sustainability implications. Organisations’ factors include legislation and regulations worldwide, all stakeholders, global vendors and international customers to keep up with the competition. Products, materials and resources can be sent to multiple locations around the United States or worldwide as part of a project’s overall scope. From the project’s perspective, it is always important to consider its scale, whether regional, national or worldwide (Gemünden, Lehner, and Kock, 2018). Sustainable project planning can be obtained by taking the correct steps towards it. The iron-triangle approach is a standard project management tool for the well-timed integration of sustainability.
Time, quality and money all fall under the umbrella of the iron triangle and form essential measures of sustainable project management. Additionally, the project’s accomplishment regarding its time, quality, improbability and cost parameters is also considered in an impending approach. Choosing project management procedures should always mull over the sustainability criteria. Akkermans et al. (2020) examined decision-making as the most critical and analytic part of green construction projects to reject and counter numerous dangers and obstacles. Decision-makers require boosting their understanding and abilities in critical areas and subjects to carry out successful long-term projects (Neutzling et al., 2018). For sustainable project management, it can be shown that selecting suitable measures or taking into account the relevant decisions is critical.
A decision maker’s ability to establish the appropriate judgments is a distinguishing trait. It must be constantly improved to achieve high productivity and success rates in the activities performed for sustainable project management (Olawumi and Chan, 2018). Recognising the importance of collaborative relationships is crucial in forming successful partnerships (Escrig-Olmedo et al., 2019). Previous studies looked for various antecedents like shared awareness, collaborative culture, technologically driven inter-organisational systems and supplier-buyer cooperation to increase collaboration.
Sustainable Project Business Strategies
Maintaining long-term value and advantages in project management is a considerable challenge. Using crucial project management elements, environmental, economic and social sustainability can all be measured. The importance of infrastructure projects, product sustainability and the development process cannot be overstated (Marchese et al., 2018). Sustainable project management is required when infrastructure initiatives encounter differences and include partners with diverse interests and expectations. Possessing authority over a project helps move it forward and achieve its goals (Lotfi et al., 2022). Nevertheless, more adaptable project management approaches geared toward sustainability should be adopted to ensure the long-term viability of projects, particularly infrastructural ones. Sustainability in project management greatly benefits from tight supervision over the implementation phase of infrastructure development. The element of sustainability should be considered in the project’s execution, project control methods and mutual agreement amongst the stakeholders.
Project sustainability is the focus of current research, which incorporates the plan into the development management process. Researchers have studied and evaluated project management’s sustainability-related performance criteria (Fewings and Henjewele, 2019). However, little emphasis has been paid to developing project control methods and practices to ensure sustainability, particularly in infrastructural schemes (Martins et al., 2019). Sustainable plan management, or sustainability in project administration, has just a few commonly acknowledged explanations in the literature.
The notion of sustainability may be divided into three main linked and crucial groups from sustainable project activities and management perspectives. The three criteria are environmental friendliness, economic stability and social wellbeing. While ecological and social sustainability may be considered less important in the initial phases of the project, they become more important as the task evolves (Souza and Alves, 2018). Even yet, it is widely agreed that the triple-bottom-line approach to sustainable project management, which incorporates environmental, social and financial considerations, is an excellent way to go. Nowadays, corporate leaders are more concerned with achieving long-term business goals, ethics and universal values than just attaining short-term project objectives (Levy, 2018). Sustainability should be included in project management processes rather than just focusing on quality, cost, and time. It is imperative that all infrastructural projects, especially those that significantly influence natural resources and communities, be evaluated holistically for their sustainability before implementation.
Methodology
Research Method
Data from secondary sources will be examined qualitatively, and research findings will be thoroughly analysed. As a result, qualitative research methodologies will evaluate the most crucial components of implementing sustainability into project management. To demonstrate whether a project leader impacts the way sustainability is implemented as part of the project management process, the originality of the research presented will be enhanced by using a qualitative method that looks at earlier ideas and studies by various researchers (Sharp and Munly, 2022). The literature on the link between sustainability and project management will be analysed using a qualitative approach.
Data Collection
The researcher will gather secondary data for this study, including books and periodicals. When it comes to collecting data, utilising a secondary strategy is more efficient than using a primary one (Largan and Morris, 2019). Data collection methods may be prohibitively expensive in terms of both time and money in some cases. Google, EbscoHost, Emerald and Science Direct databases will be used to gather data for this project. The keywords that the researcher will search for in the literature are sustainability, corporate social responsibility, project management, and the integration of sustainability into project management. The researcher will only look at sources that use the terms provided during this investigation. A secondary data set will be used to look at the current literature on a remarkably similar issue to answer the questions posed in the study proposal.
Limitations
A researcher may not use secondary data exhaustively because it was obtained for a different purpose in the past. Because of this, the secondary data may not meet current requirements. Secondary data sources offer vast information, but volume does not always indicate suitability. Typically, secondary data is slanted in favour of the person who obtained it because someone else collected it. In other words, it may not successfully meet the needs of a different researcher.
Reliability
All of the data gathered will be adequately and objectively analysed to ensure that the conclusions of the proposed research project are accurate. Recent peer-reviewed publications and books will be reliable data sources.
Validity
To obtain the most accurate answers to the research questions, the researcher will have to employ proper data collection techniques for this project. The researcher’s experiences will correlate with past studies’ data for the proposed research.
Data Analysis
The information gathered in the proposed study will be translated into variables to improve the qualitative analysis and understandably report the findings. A thematic presentation of the study’s findings will help answer the specified research questions. The researcher will undertake qualitative analysis and evaluation of the incorporation of sustainability into project management (Crossman, 2019). Qualitative approaches have no predetermined or required methods for generating conclusions, unlike quantitative procedures. Therefore, the researcher’s critical thinking will play a significant role in the study’s data analysis.
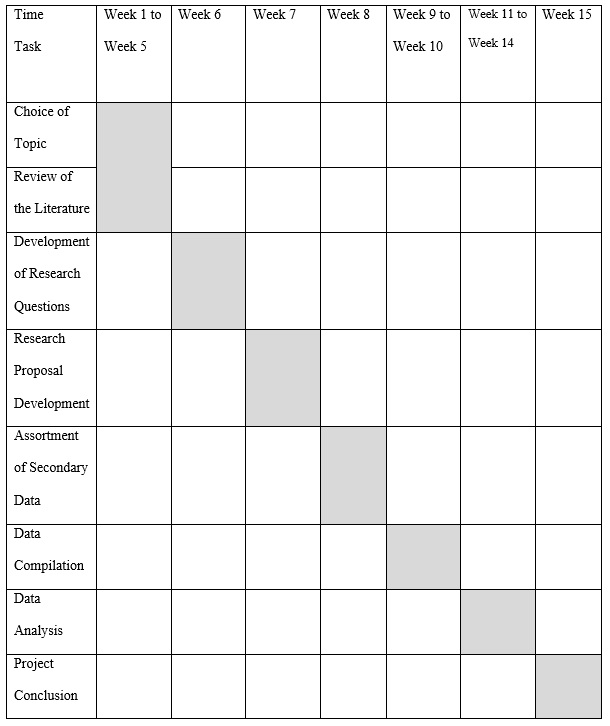
Conclusions and Recommendations
Conclusions
Projects should be accomplished on time and follow the manager’s financial plan and quality to succeed. Financial, social and natural control aspects should be integrated to use present resources judiciously, and consideration should be given to future generations worldwide. This study aims to integrate sustainability in project management, an essential profession, to promote a sustainable economy and society. The qualitative research method will use credible information from recent journals and books. Data from the secondary sources will be examined qualitatively, and research findings will be thoroughly analysed.
Recommendations
To ensure the research’s credibility, the researcher should check that all sources they plan to use are current before beginning data collection. In the future, researchers should look into how people feel about integrating sustainability into project management through other research methodologies like primary data collection and quantitative analysis.
Reference List
Adabre, M. and Chan, A. (2019) ‘Critical success factors (CSFs) for sustainable affordable housing’, Building and Environment, 156, pp. 203-214. doi: 10.1016/j.buildenv.2019.04.030
Adams, R., Martin, S. and Boom, K. (2018) ‘University culture and sustainability: designing and implementing an enabling framework’, Journal of Cleaner Production, 171, pp. 434-445. doi: 10.1016/j.jclepro.2017.10.032
Ahmed, S. (2019) ‘A review on using opportunities of augmented reality and virtual reality in construction project management’, Organisation, Technology and Management in Construction: An International Journal, 11(1), pp. 1839-1852. doi: 10.2478/otmcj-2018-0012
Akkermans, J. et al. (2020) ‘Bridging the fields of careers and project management’, Project Management Journal, 51(2), pp. 123-134. doi: 10.1177/8756972820910605
Blanco-Portela, N. et al. (2018) ‘Sustainability leaders’ perceptions on the drivers for and the barriers to the integration of sustainability in Latin American higher education institutions’, Sustainability, 10(8), pp. 2954-2966. doi: 10.3390/su10082954
Ciccullo, F. et al. (2018) ‘Integrating the environmental and social sustainability pillars into the lean and agile supply chain management paradigms: a literature review and future research directions’, Journal of cleaner production, 172, pp. 2336-2350. doi: 10.1016/j.jclepro.2017.11.176
Crossman, A. (2019) Understanding secondary data and how to use it in research. Thoughtco.
Escrig-Olmedo, E. et al. (2019) ‘Rating the raters: evaluating how ESG rating agencies integrate sustainability principles’, Sustainability, 11(3), pp. 915-923. doi: 10.3390/su11030915
Fewings, P. and Henjewele, C. (2019) Construction project management: an integrated approach. 3rd edn. Oxford: Routledge.
Gemünden, H., Lehner, P. and Kock, A. (2018) ‘The project-oriented organisation and its contribution to innovation’, International Journal of Project Management, 36(1), pp. 147-160. doi: 10.1016/j.ijproman.2017.07.009
Gijzel, D. et al. (2019) ‘Integrating sustainability into major infrastructure projects: four perspectives on sustainable tunnel development’, Sustainability, 12(1), pp. 6-11. doi: 10.3390/su12010006
Largan, C. and Morris, T. (2019) Qualitative secondary research: a step-by-step guide. Newcastle upon Tyne: Sage.
Levy, S. (2018) Project management in construction. 7th edn. New York, NY: McGraw-Hill Education.
Lotfi, R. et al. (2022) ‘A robust time-cost-quality-energy-environment trade-off with resource-constrained in project management: a case study for a bridge construction project’, Journal of Industrial & Management Optimisation, 18(1), pp. 375-396. doi: 10.3934/jimo.2020158
Marchese, D. et al. (2018) ‘Resilience and sustainability: similarities and differences in environmental management applications’, Science of the Total Environment, 613, pp. 1275-1283. doi: 10.1016/j.scitotenv.2017.09.086
Martens, M. and Carvalho, M. (2017) ‘Key factors of sustainability in project management context: a survey exploring the project managers’ perspective’, International Journal of Project Management, 35, pp. 1084-1102. doi: 10.1016/j.ijproman.2016.04.004
Martins, V. et al. (2019) ‘Knowledge management in the context of sustainability: literature review and opportunities for future research’, Journal of Cleaner Production, 229, pp. 489-500. doi: 10.1016/j.jclepro.2019.04.354
Mavi, R. and Standing, C. (2018) ‘Critical success factors of sustainable project management in construction: a fuzzy DEMATEL-ANP approach’, Journal of Cleaner Production, 194, pp. 751-765. doi: 10.1016/j.jclepro.2018.05.120
Neutzling, D. et al. (2018) ‘Linking sustainability-oriented innovation to supply chain relationship integration’, Journal of Cleaner Production, 172, pp. 3448-3458. doi: 10.1016/j.jclepro.2017.11.091
Olawumi, T. and Chan, D. (2018) ‘Identifying and prioritising the benefits of integrating BIM and sustainability practices in construction projects: a Delphi survey of international experts’, Sustainable Cities and Society, 40, pp. 16-27. doi: 10.1016/j.scs.2018.03.033
Sharp, E. and Munly, K. (2022) ‘Reopening a can of words: qualitative secondary data analysis’, Journal of Family Theory & Review, 14(1), pp. 44-58. doi: 10.1111/jftr.12443
Souza, J. and Alves, J. (2018) ‘Lean-integrated management system: a model for sustainability improvement’, Journal of Cleaner Production, 172, pp. 2667-2682. doi: 10.1016/j.jclepro.2017.11.144
Thacker, S. et al. (2019) ‘Infrastructure for sustainable development’, Nature Sustainability, 2(4), pp. 324-331. doi: 10.1038/s41893-019-0256-8
Thürer, M. et al. (2018) ‘A systematic review of the literature on integrating sustainability into engineering curricula’, Journal of Cleaner Production, 181, pp. 608-617. doi: 10.1016/j.jclepro.2017.12.130
Vrchota, J. et al. (2020) ‘Critical success factors of the project management in relation to industry 4.0 for sustainability of projects’, Sustainability, 13(1), pp. 281-284. doi: 10.3390/su13010281